- 您的位置:
- 标准下载网 >>
- 标准分类 >>
- 航天工业行业标准(QJ) >>
- QJ 1906-1990 半导体器件破坏性物理分析及失效分析程序和方法
标准号:
QJ 1906-1990
标准名称:
半导体器件破坏性物理分析及失效分析程序和方法
标准类别:
航天工业行业标准(QJ)
标准状态:
已作废-
发布日期:
1990-02-13 -
实施日期:
1990-12-30 出版语种:
简体中文下载格式:
.rar.pdf下载大小:
2.88 MB
替代情况:
被QJ 1906A-1997代替

部分标准内容:
中华人民共和国航空航天工业部航天工业标准QJ1906-90
半导体器件破坏性物理分析
及失效分析程序和方法
1990-02-13发布
中华人民共和国航空航天工业部1990-12-13实施
中华人民共和国航空航天工业部航天工业标准半导体器件破坏性物理分析及失效分析程序和方法
1主题内容与适用范围
QJ1906-90
本标准规定了半导体器件失效分析前的准备、分析程序、详细的分析方法和分析结果的处理等。
本标准适用于半导体分立器件和半导体集成电路。本标准的破坏性物理分析部分,适用于准备应用和已经应用(但未失效)的半导体器件的质量评定或验收;失效分析部分,适用于对失效半导体器件的分析或质量反馈。2引用标准
GJB548
3术语
3.1缺陷
微电子器件试验方法和程序
在外形、装配、功能或工艺质量等方面与详细技术规范规定的任何不一致现象。3.2可筛选缺陷
可利用有效的非破坏性筛选方法和检验方法别除的缺陷3.3批次性缺陷
由设计、制造过程的差错所造成的(例如:金属化层厚度、键合强度、绝缘材料性能、金属化布线、键合引线之间以及键合引线与芯片边沿之间的间距不当或掩膜缺陷等。)并在多个器件上重复出现的缺陷3.4失效模式
失效模式系指器件失效的表现形式,3.5失效机理
失效机理是导致器件失效的物理、化学变化等内在原因。4破坏性物理分析程序和方法
4.1目的
航空航天工业部1990-02-13批准1990-12-13实施
QJ1906-90
为了检验性能合格的器件是否符合原始设计和工艺的要求,对器件进行解剖、试验和分析的过程称为破坏性物理分析(简称DPA)。DPA程序和方法是为进行破坏性物理分析的器件提供详细技术要求,它们应包括取样、样品制备、试验步骤、接收/拒收标准、拒收批的处理以及试验记录等,通过破坏性物理分析,可以判定器件存在的缺陷,评定器件质量水平4.2分析准备
4.2.1设备
用于破坏性物理分析的仪器、设备应包括:立体显微镜、金相显微镜、X光照相系统、颗粒碰撞躁声检测仪、检漏设备、质谱仪或露点测试系统、测克计、扫描电子显微镜、管芯剪切仪、管壳开启器等,4.2.2破坏性物理分析报告的内容与要求对每个检验批都应写出破坏性物理分析报告,并提供给委托单位的质量控制部门。报告应包括下列内容:
a。记录分析试验中取得的全部特征数据;b。照片应在适当放大倍数下进行拍照,要求能足以清楚地显示器件结构的重要证据和细节。在进行破坏性试验以前,对分析部位的原始特征进行拍照,试验后观测到的缺陷或异常情况应再拍照。彩色、暗场、相衬、干射、对比等显微技术,可用来提高图象的清晰度。当使用扫描电镜进行检查时,报告至少应包括:管芯特征放大照片,氧化层台阶最坏情况的照片,金属化层最坏情况的照片,每张照片应标注报告号,如果需要,还应有器件型号、序号、批日期、放大倍数和观察角等;c.对样品进行破坏性物理分析所得的全部结果,应由专业技术人员进行分析,并决定对样品代表批次的处理以及应采取的纠正措施。4.2.3分析人员
分析人员应有较好的专业基础(如器件设计、制造、测试、可靠性试验、可靠性物理、化学、冶金等)和较丰富的实践经验,最好受过专业培训。4.2.4原始设计资料准备
每份破坏性物理分析的原始资料应附有被检器件的总体结构轮图或示意图,其中包括重要尺寸、各组成元件的位置和有关材料及工艺细节,所提供的原始记录应是现行的,以便能表示出已批准结构的任何改变4.3DPA程序和方法
4.3.1样品选取
如无特殊要求,应从检验批中随机抽取样品,但其数量不得少于2只或多于5只,如果检验批由一种以上器件组成,样品选择应根据器件种类按比例分组,以保证抽样的代表2
性,并且每类器件不少于1只。
4.3.2外部检查
QJ1906-90
记录外壳上的有关标记,在大于10倍的双目立体显微镜下按GJB548的方法2009检查密封、镀层和玻璃填料工艺中的缺陷。4.3.3X射线照相
按GJB548的方法2012进行X射线照相。照相应在开帽前进行。它用来检查管壳内的可动颗粒、芯片粘接和确定内部空腔的形状。也可用于确定开封的切开位置和对有怀疑的缺陷进行非破坏性检查。
4.3.4颗粒碰撞噪声检测
按GJB548的方法2020进行颗粒碰撞噪声检测.用来确定器件管腔内部是否存在可动颗粒。
4.3.5密封性检验
按GJB548的方法1014进行器件的密封性检验.记录器件的漏率(包括细漏和粗漏)。
4.3.6内部水汽分析
按GJB548的方法1018进行内部水汽分析,4.3.7内部检查
用适当的方法打开管壳。开壳操作应特别小心,防止引起内部损伤和沾污,开封后按GJB548的方法2013、2014进行检查。必要时,也可以按方法2010进行检查。4.3.8结构检查
在外部和内部检查中,应评价器件与原始设计文件(见4.2.4条)及其它规定的相符性,对全部器件进行评价,与要求不符的应作为缺陷加以记录。4.3.9键合强度试验
按GJB548的方法2011的试验条件D进行键合强度试验。至少对两个器件的全部内引线进行键合强度试验,应记录内引线断裂或脱开时的拉力及断裂位置。4.3.10扫描电镜检查
为扫描电镜制备样品,按GJB548的方法2018进行检验,键合强度试验中脱开的键合点应进行扫描电镜检查,以确定键合脱开处的界面的特征。4.3.11管芯剪切试验
按GJB548的方法2019,至少对两个样品进行管芯剪切试验,记录使芯片与底座分离的力,以及断裂处的界面状态。4.3.12评价标准
按下列标准进行检验或试验时,如器件出现任何缺陷,该检验批应认为是可疑的,应对每种缺陷进行拍照和测量,并在破坏性物理分析报告中说明。3
检验要求
外部检查
X射线照相
颗粒碰撞噪声检测
密封性检验
内部水汽分析此内容来自标准下载网
内部检查
键合强度试验
扫描电镜检查
管芯剪切试验
原始结构检查
4.3.13可疑批的处理
QJ1906-90
GJB548评价标准
方法2009
方法2012
方法2020
方法1014
方法1018
方法2013、2014必要时用方法2010方法2011
方法2018
方法2019
原始设计文件
对破坏性物理分析的结果进行评价,如果样品中发现有一个或更多的拒收缺陷时,该检验批就应认为是可疑的,并用下列方法处理:距。如果第一个有缺陷的样品缺乏说服力应重新抽样;b.重新筛选;
c.报废;
d.拒收退货。
4.3.13.1重新抽样
如果首次进行破坏性物理分析的样品,其结果缺乏说服力,可按4.3.1条规定重新抽样。待新样品评价后,再作出该检验批的最终结论、4.3.13.2重新筛选
在检验批中发现可筛选缺陷时,应进行百分之百的非破坏性筛选试验来剔除不合格器件,筛选合格品可接收使用。
4.3.14样品保管
当提交单位有要求时,破坏性物理分析的全部样品和破坏性物理分析报告应一同送交委托单位或鉴定单位。
5半导体器件失效分析程序和方法5.1目的
通过失效分析,可以验证器件是否失效、识别失效模式、确定失效机理。根据失效分析结论提出改进器件生产工艺、设计、材料、试验和应用的措施,消除报告中的失效模式或机理,防止其重现出现,
5.2设备
5.2.1电特性测试设备
QJ1906-90
电特性测试设备应包括:特性曲线图示仪、集成电路测试仪、示波器、电流表、电压表、直流电源、小信号发生器、脉冲发生器、电容表等。5.2.2观测设备
观测设备应包括:带摄影装置的立体显微镜和金相显微镜、X射线透视和照相系统等。
5.2.3试验设备
试验设备应包括:高温箱、低温箱、测克计和检漏设备、颗粒碰撞噪声检测仪等,5.2.4解剖工具和辅助设备
解剖工具和辅助设备应包括:管帽开启器、机械微探针、研磨设备及夹具、常用的电工和钳工工具等,
5.2.5化学腐蚀间
化学腐蚀间应有通风柜和清洗池并配有去离子水系统和若干化学药品等。5.2.6先进的分析设备
先进的分析设备应包括:扫描电子显微镜、电子微探针、俄歇电子微探针、离子微探针、红外热象仪、气体质谱仪等。5.3分析人员
见4.2.3条。
5.4失效器件的有关资料
失效分析人员在收到失效器件的同时还应获得以下资料:a。器件经过的试验条件,包括器件经过的可靠性试验和使用时间、电应力、温度等;
b.器件所在系统的条件,包括器件在系统(设备)中的准确位置(包括设备名称、台号、部位)、功能、失效日期、失效地点、器件失效时系统出现的异常现象和判断器件在系统中失效的过程;
c.器件的一般资料,包括器件型号、序号、生产日期、批次、生产厂等,5.5失效分析程序和方法
5.5.1分析程序A
分析程序A是最低限度的分析程序,它由外部检查、电测验证和内部检查组成.按下列顺序进行试验,并把分析结果写人失效分析报告中。5.5.1.1外部检查
在适当放大倍数下用显微镜进行下列检查:a,外引线、电镀层、锡焊或熔焊区;5
QJ1906-90
b.管壳封装材料、密封、标志等;对任何异常现象,应在适当放大倍数下拍照记录。5.5.1.2电学验证
对规定的电参数进行电学测量,必要时应进行高低温性能测试。5.5.1.3补充电试验
为了确定开路或短路,应做下列试验:8。测定各条外引线与衬底间的正向特性,并根据器件原理图和线路结构图进行分析。过大的正向压降则表示电流通路内有开路和高阻;b。在管壳与外引线之间加电压(仅对金属封装或有金属帽或座的封装而言),如有电流通过,则可确定外引线与外壳短路。5.5.1.4内部检查
小心地去掉失效器件的帽或盖,用大于30倍的立体显微镜和金相显微镜检查组装键合及芯片表面细节,对异常现象进行拍照。5.5.1.5可获得的结果
分析程序A可以鉴别出的一部分失效模式或机理如下:8过电应力引起的引线或金属化层的开路或短路;b.表明结特性退化的过量漏电流:c.内引线或金属化焊接区的开路及短路;d。金属迁移;
金属层缺损或剥皮;
f.封装内部的金属腐蚀;
氧化层污染、变色;
氧化层缺陷、裂缝;
i.管芯或衬底的裂缝;
掩膜未套准;
k、电阻变化;
1.时间响应或与频率有关的参数退化;m。键合位置不良;
n。金属钻蚀。
5.5.2分析程序B
5.5.2.1外部检查
按5.5.1.1条进行检查
5.5.2.2电学验证
按5.5.1.2条进行测量,
5.5.2.3补充电试验
QJ1906-90
为了确定开路或短路,应做下列试验:a.测定各条外引线与衬底间的正向特性,并根据器件原理图和线路结构图进行分析。过大的正向压降则表示电流通路内有开路和高阻;b在管壳与外引线之间加电压(仅对金属封装或有金属帽或座的封装而言),如有电流通过,可确定外引线与外壳短路;c.根据需要,用晶体管曲线图示仪对有关的两根或三根外引线之间逐个进行电测量,将测出的特性与同类合格器件的特性相比较,并解释其差别。5.5.2.4X射线照相
当电学验证表明引线开路或短路,或有迹象表明封壳内存在多余物,或失效与温度有关时,应垂直拍摄器件表面的X射线照片。需要时还可从其它方向拍摄。具体方法按GJB548的方法2012进行
5.5.2.5细漏和粗漏的密封性试验密封性试验按GJB548的方法1014进行。5.5.2.6外壳清洗
当有迹象表明外壳被沾污时,应把器件浸人适当的去油溶剂中,随后浸人沸腾的去离子水中,取出后用于氮气吹于燥,重作5.5.2.1至5.5.2.5条规定的分析内容。5.6.2.7内部检查
小心地去掉失效器件的帽或盖,用大于30倍的立体显微镜和金相显微镜检查组装、键合及芯片表面细节,对异常现象进行拍照,如有迹象表明器件内部有多余物,应用干燥情性气体或适当的溶液清除,并说明多余物对器件的影响,如有可能,还应测定多余物的性质。
5.5.2.8电学验证
复测并记录与失效有关的电参数,5.5.2.9真空烘烤
在真空度1.013×10~1.013×10°Pa,温度150~250℃条件下烘烤2h,用微微安表测量漏电流在烘烤前后的变化。5.5.2.10电学验证
复测并记录与失效有关的电参数。5.5.2.11多头探针测试
用多头探针探测器件的有源区,可进一步确定失效部位。用特性曲线图示仪测电阻值,局部开路和短路现象,击穿电压和晶体管的增益参数。用微微安表测微小的漏电流,电容电桥测结电容,为了隔离集成电路中的元件,必须断开有关的金属化互连线5.5.2.12可获得的结果
QJ1906-90
除了在5.5.1.5条中指出的结果外,分析程序B还可以获得以下结论:8.各种密封性问题;
b。X射线照片可以确定以下缺陷:引线位置不良、开焊、管芯或衬底与固定材料中的空隙、多余物;
c.进一步确定失效部位;
d与表面有关参数的稳定性;
e.结、扩散层和元件的质量。
5.5.3分析程序C
分析程序C是在分析程序B完成后再增加金相分析。应按下列顺序试验,并把结果写入失效分析报告,
5.5.3.1器件的总横截面
当外壳、芯片或衬底、键合、密封或结构元件中出现缺陷迹象时,应做以下工作:a。把器件固定在合适的方位,便于横截面的制作;b。制作的横截面应能揭示所需特征,并在需要的地方染色;c.在适当放大倍数下,用金相显微镜的明视场、暗视场或偏振光进行观察和拍照;d。对与失效模式或机理有关的缺陷部位进行拍照记录。5.5.3.2氧化层缺陷分析
当有迹象表明氧化层(或其它电介质)结构异常,氧化层内部或底下有污染,当需要确定这些缺陷的特定位置和结构时,应做以下工作:8。去掉芯片或村底上的键合,并去掉金属化互连线;b.用干涉显微镜在适当放大倍数下观察氧化层缺陷并根据需要拍照;c.需要时应观察和探测半导体接触区(窗口或断面)并记下相应的电特性;d.把芯片或衬底固定在便于制作横截面的方位上,并切开或抛光显示所需特征,需要时应进行PN结染色;
e.对需要记录的部位用适当放大倍数进行显微拍照。5.5.3.3扩散缺陷分析
当有迹象表明存在扩散缺陷、接触金属扩散进人半导体内或半导体内有结构缺陷以及结的几何形状异常时,应做以下工作:8.去掉芯片或衬底上的键合,并去掉金属化互连线。探测接触区,记录相应的电特性;
b.对表面染色以显示PN结外形,需要时应把芯片或衬底固定在便于制作切开横截面或磨角的方位上。去掉氧化层或其它电介质钝化层.按需要进行切磨,以显露重要特征并对结染色(为探讨特定缺陷,可多次切磨和染色).在适当放大倍数下对重要特征拍照,并记录有关电探测结果。8
5.5.3.4可获得的结果
QJ1906-90
按分析程序C进行的失效分析,可进一步提供探测或确定下列缺陷类型:a。氧化层或介质的不完善;
b.氧化层或介质的厚度;
c.扩散的不完善性;
d.PN结的几何形状;
在键合与金属化层界面处的空隙;e.
f.金属间化合物的形成;
g.接触金属扩散进半导体或衬底内;h。金属穿过氧化层(或介质层)的迁移或在它底下的迁移;i。芯片或衬底与管座间的空隙。5.5.4自选测量
根据失效分析目的,在分析程序A、B或C的进行过程中如果仍需要更详细的信息,以便在器件的设计、生产、试验或应用中改进工作,下面的分析技术是在不破坏失效证据的情况下,由失效分析人员自行决定在适当时候将自选测量中的专门技术引人分析程序中,并把所用方法的细节,试验条件和结果列入失效分析报告中。a.残余气体分析
当失效原因可能是表面污染时,应在未开封器件的外壳上开孔对壳内气体取样、分析内部气体的类型和挥发物浓度。其分析结果是漏电流测量及密封性试验的补充资料;b.芯片表面轮廊测量
表面光度仪采用机械方法测定芯片表面的形貌变化。仪器“探测头”沿器件芯片表面移动并记录其垂直运动轨迹。它可定量测定氧化层、介质层或金属层的厚度:c.激光扫描
引线和内部连接完整无缺的器件,打开后可用一小直径激光束在芯片表面扫描,它在有源区PN结上产生光电压,所产生的光电压与结的许多物理特性有关,光电压揭示了表面沟道和反型层的存在,这些沟道和反型层是由于钝化(氧化)层表面、内部或其下面受污染而形成.光电压也能判断电场增强的倍增区、掩膜未对准区、不完善的扩散区和与结特性有关的其它缺陷;
d。红外扫描
用红外探测器对准正在工作的器件芯片表面,逐点进行取样,它可以测出热点和其它热异常现象的位置;
e.扫描电镜和电子微探针
用扫描电镜可方便地进行形貌细节的观察,可分析微米大小的缺陷,并可测定表面电压的变化。扫描电镜配合电子微探针,可进行固态材料成份的分析,9
5.6失效分析报告
QJ1906-90
整理分析试验数据和照片等,写出完整的失效分析报告并送有关部门,失效分析报告的基本内容应包括以下几方面:。原始失效情况的调查;
失效分析情况(包括测试、外观检查、试验和解剖分析的有关数据、照片、示意b.
图等);
c.失效分析结论;
d,提出改进建议。
附加说明:
本标准由航空航天工业部七○八所提出。本标准由航空航天工业部七·七一所和五一一所共同负责起草10
小提示:此标准内容仅展示完整标准里的部分截取内容,若需要完整标准请到上方自行免费下载完整标准文档。
半导体器件破坏性物理分析
及失效分析程序和方法
1990-02-13发布
中华人民共和国航空航天工业部1990-12-13实施
中华人民共和国航空航天工业部航天工业标准半导体器件破坏性物理分析及失效分析程序和方法
1主题内容与适用范围
QJ1906-90
本标准规定了半导体器件失效分析前的准备、分析程序、详细的分析方法和分析结果的处理等。
本标准适用于半导体分立器件和半导体集成电路。本标准的破坏性物理分析部分,适用于准备应用和已经应用(但未失效)的半导体器件的质量评定或验收;失效分析部分,适用于对失效半导体器件的分析或质量反馈。2引用标准
GJB548
3术语
3.1缺陷
微电子器件试验方法和程序
在外形、装配、功能或工艺质量等方面与详细技术规范规定的任何不一致现象。3.2可筛选缺陷
可利用有效的非破坏性筛选方法和检验方法别除的缺陷3.3批次性缺陷
由设计、制造过程的差错所造成的(例如:金属化层厚度、键合强度、绝缘材料性能、金属化布线、键合引线之间以及键合引线与芯片边沿之间的间距不当或掩膜缺陷等。)并在多个器件上重复出现的缺陷3.4失效模式
失效模式系指器件失效的表现形式,3.5失效机理
失效机理是导致器件失效的物理、化学变化等内在原因。4破坏性物理分析程序和方法
4.1目的
航空航天工业部1990-02-13批准1990-12-13实施
QJ1906-90
为了检验性能合格的器件是否符合原始设计和工艺的要求,对器件进行解剖、试验和分析的过程称为破坏性物理分析(简称DPA)。DPA程序和方法是为进行破坏性物理分析的器件提供详细技术要求,它们应包括取样、样品制备、试验步骤、接收/拒收标准、拒收批的处理以及试验记录等,通过破坏性物理分析,可以判定器件存在的缺陷,评定器件质量水平4.2分析准备
4.2.1设备
用于破坏性物理分析的仪器、设备应包括:立体显微镜、金相显微镜、X光照相系统、颗粒碰撞躁声检测仪、检漏设备、质谱仪或露点测试系统、测克计、扫描电子显微镜、管芯剪切仪、管壳开启器等,4.2.2破坏性物理分析报告的内容与要求对每个检验批都应写出破坏性物理分析报告,并提供给委托单位的质量控制部门。报告应包括下列内容:
a。记录分析试验中取得的全部特征数据;b。照片应在适当放大倍数下进行拍照,要求能足以清楚地显示器件结构的重要证据和细节。在进行破坏性试验以前,对分析部位的原始特征进行拍照,试验后观测到的缺陷或异常情况应再拍照。彩色、暗场、相衬、干射、对比等显微技术,可用来提高图象的清晰度。当使用扫描电镜进行检查时,报告至少应包括:管芯特征放大照片,氧化层台阶最坏情况的照片,金属化层最坏情况的照片,每张照片应标注报告号,如果需要,还应有器件型号、序号、批日期、放大倍数和观察角等;c.对样品进行破坏性物理分析所得的全部结果,应由专业技术人员进行分析,并决定对样品代表批次的处理以及应采取的纠正措施。4.2.3分析人员
分析人员应有较好的专业基础(如器件设计、制造、测试、可靠性试验、可靠性物理、化学、冶金等)和较丰富的实践经验,最好受过专业培训。4.2.4原始设计资料准备
每份破坏性物理分析的原始资料应附有被检器件的总体结构轮图或示意图,其中包括重要尺寸、各组成元件的位置和有关材料及工艺细节,所提供的原始记录应是现行的,以便能表示出已批准结构的任何改变4.3DPA程序和方法
4.3.1样品选取
如无特殊要求,应从检验批中随机抽取样品,但其数量不得少于2只或多于5只,如果检验批由一种以上器件组成,样品选择应根据器件种类按比例分组,以保证抽样的代表2
性,并且每类器件不少于1只。
4.3.2外部检查
QJ1906-90
记录外壳上的有关标记,在大于10倍的双目立体显微镜下按GJB548的方法2009检查密封、镀层和玻璃填料工艺中的缺陷。4.3.3X射线照相
按GJB548的方法2012进行X射线照相。照相应在开帽前进行。它用来检查管壳内的可动颗粒、芯片粘接和确定内部空腔的形状。也可用于确定开封的切开位置和对有怀疑的缺陷进行非破坏性检查。
4.3.4颗粒碰撞噪声检测
按GJB548的方法2020进行颗粒碰撞噪声检测.用来确定器件管腔内部是否存在可动颗粒。
4.3.5密封性检验
按GJB548的方法1014进行器件的密封性检验.记录器件的漏率(包括细漏和粗漏)。
4.3.6内部水汽分析
按GJB548的方法1018进行内部水汽分析,4.3.7内部检查
用适当的方法打开管壳。开壳操作应特别小心,防止引起内部损伤和沾污,开封后按GJB548的方法2013、2014进行检查。必要时,也可以按方法2010进行检查。4.3.8结构检查
在外部和内部检查中,应评价器件与原始设计文件(见4.2.4条)及其它规定的相符性,对全部器件进行评价,与要求不符的应作为缺陷加以记录。4.3.9键合强度试验
按GJB548的方法2011的试验条件D进行键合强度试验。至少对两个器件的全部内引线进行键合强度试验,应记录内引线断裂或脱开时的拉力及断裂位置。4.3.10扫描电镜检查
为扫描电镜制备样品,按GJB548的方法2018进行检验,键合强度试验中脱开的键合点应进行扫描电镜检查,以确定键合脱开处的界面的特征。4.3.11管芯剪切试验
按GJB548的方法2019,至少对两个样品进行管芯剪切试验,记录使芯片与底座分离的力,以及断裂处的界面状态。4.3.12评价标准
按下列标准进行检验或试验时,如器件出现任何缺陷,该检验批应认为是可疑的,应对每种缺陷进行拍照和测量,并在破坏性物理分析报告中说明。3
检验要求
外部检查
X射线照相
颗粒碰撞噪声检测
密封性检验
内部水汽分析此内容来自标准下载网
内部检查
键合强度试验
扫描电镜检查
管芯剪切试验
原始结构检查
4.3.13可疑批的处理
QJ1906-90
GJB548评价标准
方法2009
方法2012
方法2020
方法1014
方法1018
方法2013、2014必要时用方法2010方法2011
方法2018
方法2019
原始设计文件
对破坏性物理分析的结果进行评价,如果样品中发现有一个或更多的拒收缺陷时,该检验批就应认为是可疑的,并用下列方法处理:距。如果第一个有缺陷的样品缺乏说服力应重新抽样;b.重新筛选;
c.报废;
d.拒收退货。
4.3.13.1重新抽样
如果首次进行破坏性物理分析的样品,其结果缺乏说服力,可按4.3.1条规定重新抽样。待新样品评价后,再作出该检验批的最终结论、4.3.13.2重新筛选
在检验批中发现可筛选缺陷时,应进行百分之百的非破坏性筛选试验来剔除不合格器件,筛选合格品可接收使用。
4.3.14样品保管
当提交单位有要求时,破坏性物理分析的全部样品和破坏性物理分析报告应一同送交委托单位或鉴定单位。
5半导体器件失效分析程序和方法5.1目的
通过失效分析,可以验证器件是否失效、识别失效模式、确定失效机理。根据失效分析结论提出改进器件生产工艺、设计、材料、试验和应用的措施,消除报告中的失效模式或机理,防止其重现出现,
5.2设备
5.2.1电特性测试设备
QJ1906-90
电特性测试设备应包括:特性曲线图示仪、集成电路测试仪、示波器、电流表、电压表、直流电源、小信号发生器、脉冲发生器、电容表等。5.2.2观测设备
观测设备应包括:带摄影装置的立体显微镜和金相显微镜、X射线透视和照相系统等。
5.2.3试验设备
试验设备应包括:高温箱、低温箱、测克计和检漏设备、颗粒碰撞噪声检测仪等,5.2.4解剖工具和辅助设备
解剖工具和辅助设备应包括:管帽开启器、机械微探针、研磨设备及夹具、常用的电工和钳工工具等,
5.2.5化学腐蚀间
化学腐蚀间应有通风柜和清洗池并配有去离子水系统和若干化学药品等。5.2.6先进的分析设备
先进的分析设备应包括:扫描电子显微镜、电子微探针、俄歇电子微探针、离子微探针、红外热象仪、气体质谱仪等。5.3分析人员
见4.2.3条。
5.4失效器件的有关资料
失效分析人员在收到失效器件的同时还应获得以下资料:a。器件经过的试验条件,包括器件经过的可靠性试验和使用时间、电应力、温度等;
b.器件所在系统的条件,包括器件在系统(设备)中的准确位置(包括设备名称、台号、部位)、功能、失效日期、失效地点、器件失效时系统出现的异常现象和判断器件在系统中失效的过程;
c.器件的一般资料,包括器件型号、序号、生产日期、批次、生产厂等,5.5失效分析程序和方法
5.5.1分析程序A
分析程序A是最低限度的分析程序,它由外部检查、电测验证和内部检查组成.按下列顺序进行试验,并把分析结果写人失效分析报告中。5.5.1.1外部检查
在适当放大倍数下用显微镜进行下列检查:a,外引线、电镀层、锡焊或熔焊区;5
QJ1906-90
b.管壳封装材料、密封、标志等;对任何异常现象,应在适当放大倍数下拍照记录。5.5.1.2电学验证
对规定的电参数进行电学测量,必要时应进行高低温性能测试。5.5.1.3补充电试验
为了确定开路或短路,应做下列试验:8。测定各条外引线与衬底间的正向特性,并根据器件原理图和线路结构图进行分析。过大的正向压降则表示电流通路内有开路和高阻;b。在管壳与外引线之间加电压(仅对金属封装或有金属帽或座的封装而言),如有电流通过,则可确定外引线与外壳短路。5.5.1.4内部检查
小心地去掉失效器件的帽或盖,用大于30倍的立体显微镜和金相显微镜检查组装键合及芯片表面细节,对异常现象进行拍照。5.5.1.5可获得的结果
分析程序A可以鉴别出的一部分失效模式或机理如下:8过电应力引起的引线或金属化层的开路或短路;b.表明结特性退化的过量漏电流:c.内引线或金属化焊接区的开路及短路;d。金属迁移;
金属层缺损或剥皮;
f.封装内部的金属腐蚀;
氧化层污染、变色;
氧化层缺陷、裂缝;
i.管芯或衬底的裂缝;
掩膜未套准;
k、电阻变化;
1.时间响应或与频率有关的参数退化;m。键合位置不良;
n。金属钻蚀。
5.5.2分析程序B
5.5.2.1外部检查
按5.5.1.1条进行检查
5.5.2.2电学验证
按5.5.1.2条进行测量,
5.5.2.3补充电试验
QJ1906-90
为了确定开路或短路,应做下列试验:a.测定各条外引线与衬底间的正向特性,并根据器件原理图和线路结构图进行分析。过大的正向压降则表示电流通路内有开路和高阻;b在管壳与外引线之间加电压(仅对金属封装或有金属帽或座的封装而言),如有电流通过,可确定外引线与外壳短路;c.根据需要,用晶体管曲线图示仪对有关的两根或三根外引线之间逐个进行电测量,将测出的特性与同类合格器件的特性相比较,并解释其差别。5.5.2.4X射线照相
当电学验证表明引线开路或短路,或有迹象表明封壳内存在多余物,或失效与温度有关时,应垂直拍摄器件表面的X射线照片。需要时还可从其它方向拍摄。具体方法按GJB548的方法2012进行
5.5.2.5细漏和粗漏的密封性试验密封性试验按GJB548的方法1014进行。5.5.2.6外壳清洗
当有迹象表明外壳被沾污时,应把器件浸人适当的去油溶剂中,随后浸人沸腾的去离子水中,取出后用于氮气吹于燥,重作5.5.2.1至5.5.2.5条规定的分析内容。5.6.2.7内部检查
小心地去掉失效器件的帽或盖,用大于30倍的立体显微镜和金相显微镜检查组装、键合及芯片表面细节,对异常现象进行拍照,如有迹象表明器件内部有多余物,应用干燥情性气体或适当的溶液清除,并说明多余物对器件的影响,如有可能,还应测定多余物的性质。
5.5.2.8电学验证
复测并记录与失效有关的电参数,5.5.2.9真空烘烤
在真空度1.013×10~1.013×10°Pa,温度150~250℃条件下烘烤2h,用微微安表测量漏电流在烘烤前后的变化。5.5.2.10电学验证
复测并记录与失效有关的电参数。5.5.2.11多头探针测试
用多头探针探测器件的有源区,可进一步确定失效部位。用特性曲线图示仪测电阻值,局部开路和短路现象,击穿电压和晶体管的增益参数。用微微安表测微小的漏电流,电容电桥测结电容,为了隔离集成电路中的元件,必须断开有关的金属化互连线5.5.2.12可获得的结果
QJ1906-90
除了在5.5.1.5条中指出的结果外,分析程序B还可以获得以下结论:8.各种密封性问题;
b。X射线照片可以确定以下缺陷:引线位置不良、开焊、管芯或衬底与固定材料中的空隙、多余物;
c.进一步确定失效部位;
d与表面有关参数的稳定性;
e.结、扩散层和元件的质量。
5.5.3分析程序C
分析程序C是在分析程序B完成后再增加金相分析。应按下列顺序试验,并把结果写入失效分析报告,
5.5.3.1器件的总横截面
当外壳、芯片或衬底、键合、密封或结构元件中出现缺陷迹象时,应做以下工作:a。把器件固定在合适的方位,便于横截面的制作;b。制作的横截面应能揭示所需特征,并在需要的地方染色;c.在适当放大倍数下,用金相显微镜的明视场、暗视场或偏振光进行观察和拍照;d。对与失效模式或机理有关的缺陷部位进行拍照记录。5.5.3.2氧化层缺陷分析
当有迹象表明氧化层(或其它电介质)结构异常,氧化层内部或底下有污染,当需要确定这些缺陷的特定位置和结构时,应做以下工作:8。去掉芯片或村底上的键合,并去掉金属化互连线;b.用干涉显微镜在适当放大倍数下观察氧化层缺陷并根据需要拍照;c.需要时应观察和探测半导体接触区(窗口或断面)并记下相应的电特性;d.把芯片或衬底固定在便于制作横截面的方位上,并切开或抛光显示所需特征,需要时应进行PN结染色;
e.对需要记录的部位用适当放大倍数进行显微拍照。5.5.3.3扩散缺陷分析
当有迹象表明存在扩散缺陷、接触金属扩散进人半导体内或半导体内有结构缺陷以及结的几何形状异常时,应做以下工作:8.去掉芯片或衬底上的键合,并去掉金属化互连线。探测接触区,记录相应的电特性;
b.对表面染色以显示PN结外形,需要时应把芯片或衬底固定在便于制作切开横截面或磨角的方位上。去掉氧化层或其它电介质钝化层.按需要进行切磨,以显露重要特征并对结染色(为探讨特定缺陷,可多次切磨和染色).在适当放大倍数下对重要特征拍照,并记录有关电探测结果。8
5.5.3.4可获得的结果
QJ1906-90
按分析程序C进行的失效分析,可进一步提供探测或确定下列缺陷类型:a。氧化层或介质的不完善;
b.氧化层或介质的厚度;
c.扩散的不完善性;
d.PN结的几何形状;
在键合与金属化层界面处的空隙;e.
f.金属间化合物的形成;
g.接触金属扩散进半导体或衬底内;h。金属穿过氧化层(或介质层)的迁移或在它底下的迁移;i。芯片或衬底与管座间的空隙。5.5.4自选测量
根据失效分析目的,在分析程序A、B或C的进行过程中如果仍需要更详细的信息,以便在器件的设计、生产、试验或应用中改进工作,下面的分析技术是在不破坏失效证据的情况下,由失效分析人员自行决定在适当时候将自选测量中的专门技术引人分析程序中,并把所用方法的细节,试验条件和结果列入失效分析报告中。a.残余气体分析
当失效原因可能是表面污染时,应在未开封器件的外壳上开孔对壳内气体取样、分析内部气体的类型和挥发物浓度。其分析结果是漏电流测量及密封性试验的补充资料;b.芯片表面轮廊测量
表面光度仪采用机械方法测定芯片表面的形貌变化。仪器“探测头”沿器件芯片表面移动并记录其垂直运动轨迹。它可定量测定氧化层、介质层或金属层的厚度:c.激光扫描
引线和内部连接完整无缺的器件,打开后可用一小直径激光束在芯片表面扫描,它在有源区PN结上产生光电压,所产生的光电压与结的许多物理特性有关,光电压揭示了表面沟道和反型层的存在,这些沟道和反型层是由于钝化(氧化)层表面、内部或其下面受污染而形成.光电压也能判断电场增强的倍增区、掩膜未对准区、不完善的扩散区和与结特性有关的其它缺陷;
d。红外扫描
用红外探测器对准正在工作的器件芯片表面,逐点进行取样,它可以测出热点和其它热异常现象的位置;
e.扫描电镜和电子微探针
用扫描电镜可方便地进行形貌细节的观察,可分析微米大小的缺陷,并可测定表面电压的变化。扫描电镜配合电子微探针,可进行固态材料成份的分析,9
5.6失效分析报告
QJ1906-90
整理分析试验数据和照片等,写出完整的失效分析报告并送有关部门,失效分析报告的基本内容应包括以下几方面:。原始失效情况的调查;
失效分析情况(包括测试、外观检查、试验和解剖分析的有关数据、照片、示意b.
图等);
c.失效分析结论;
d,提出改进建议。
附加说明:
本标准由航空航天工业部七○八所提出。本标准由航空航天工业部七·七一所和五一一所共同负责起草10
小提示:此标准内容仅展示完整标准里的部分截取内容,若需要完整标准请到上方自行免费下载完整标准文档。

标准图片预览:
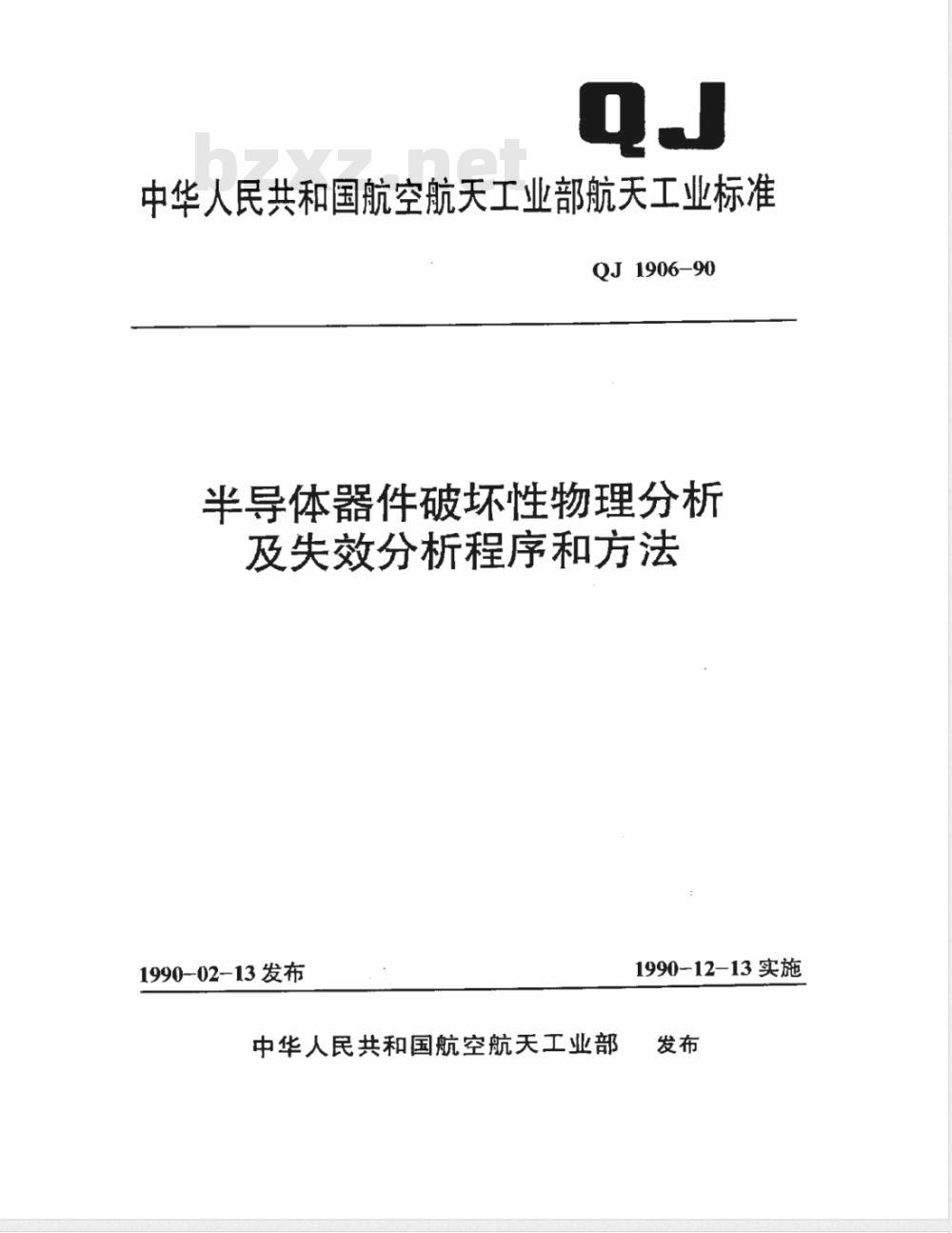
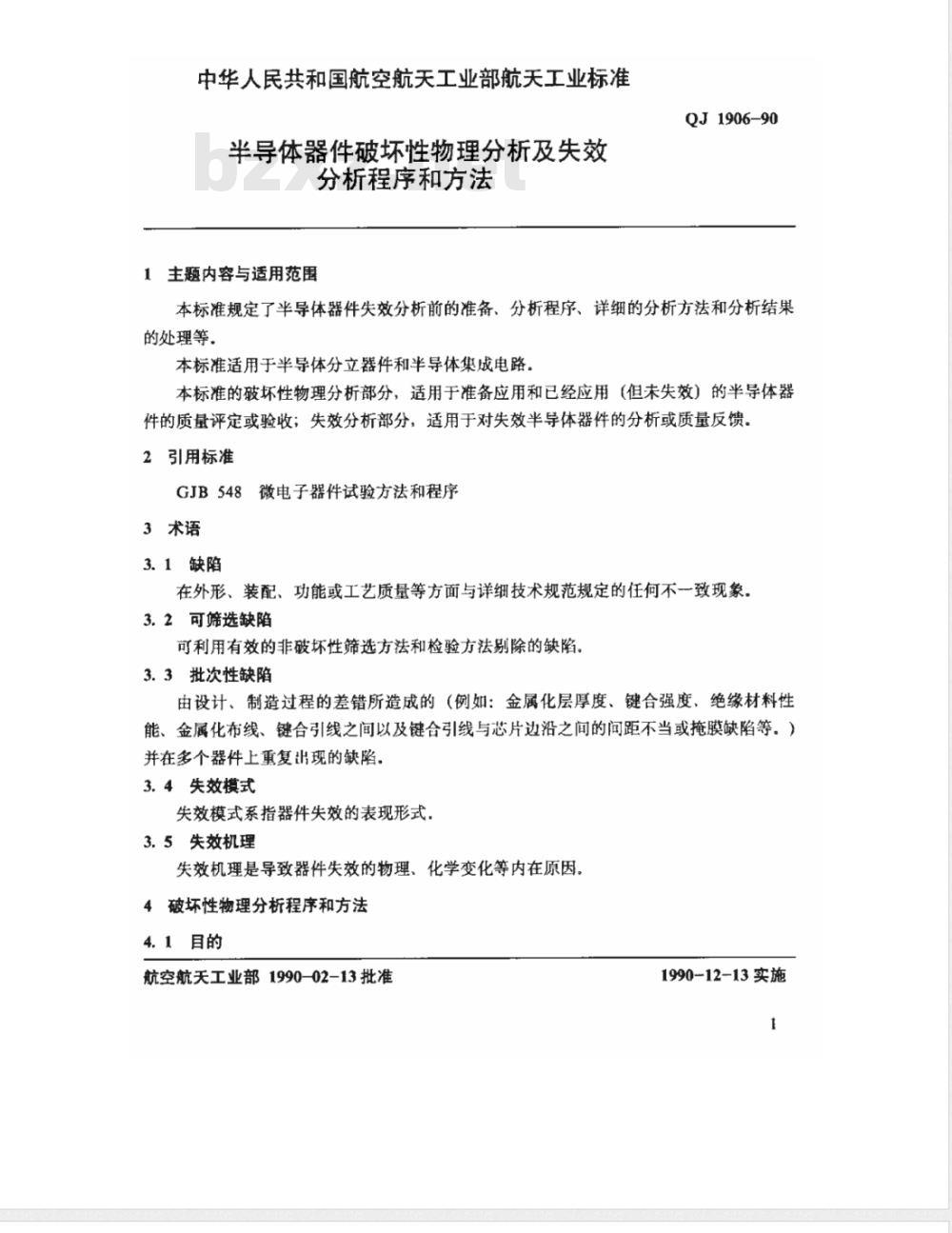
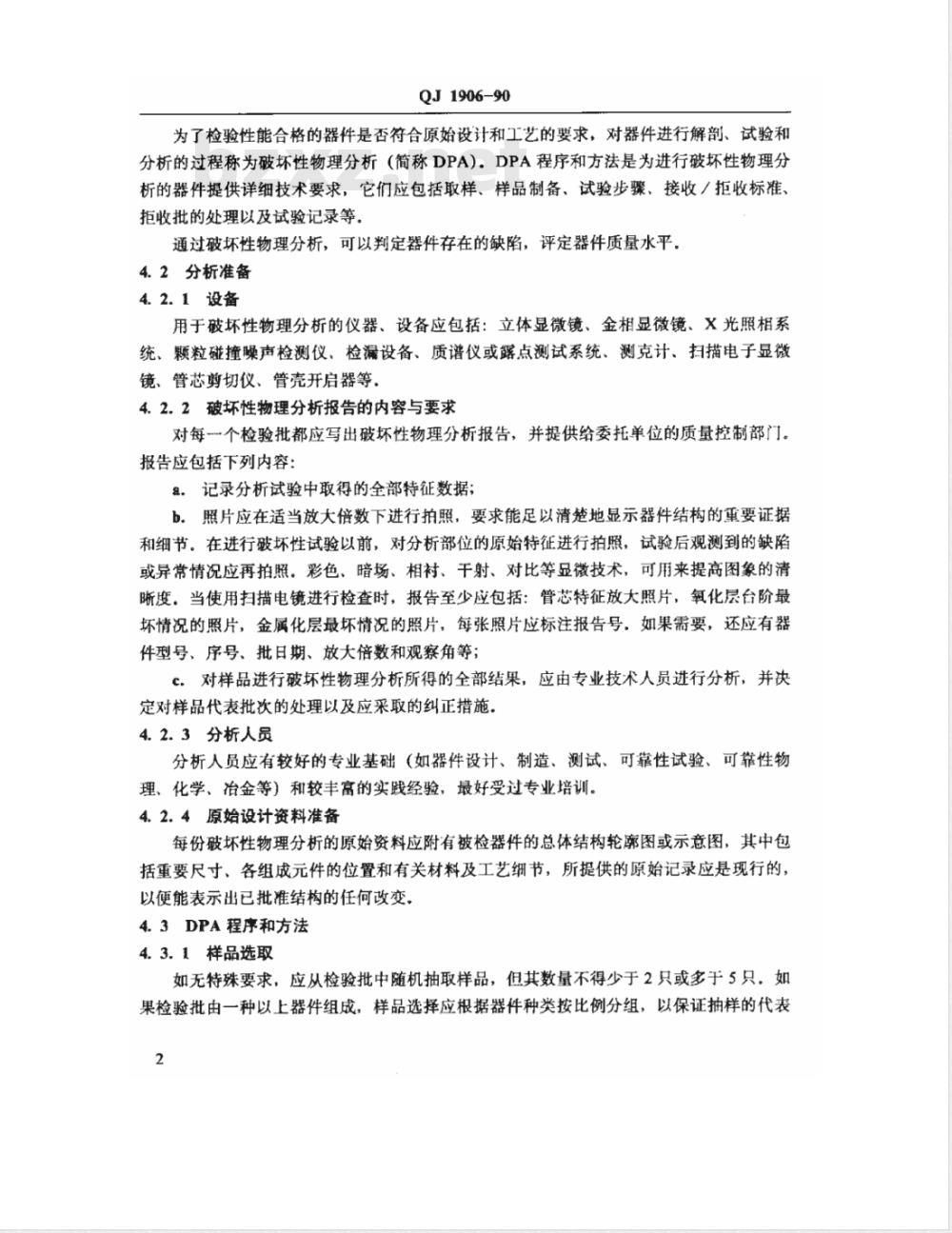
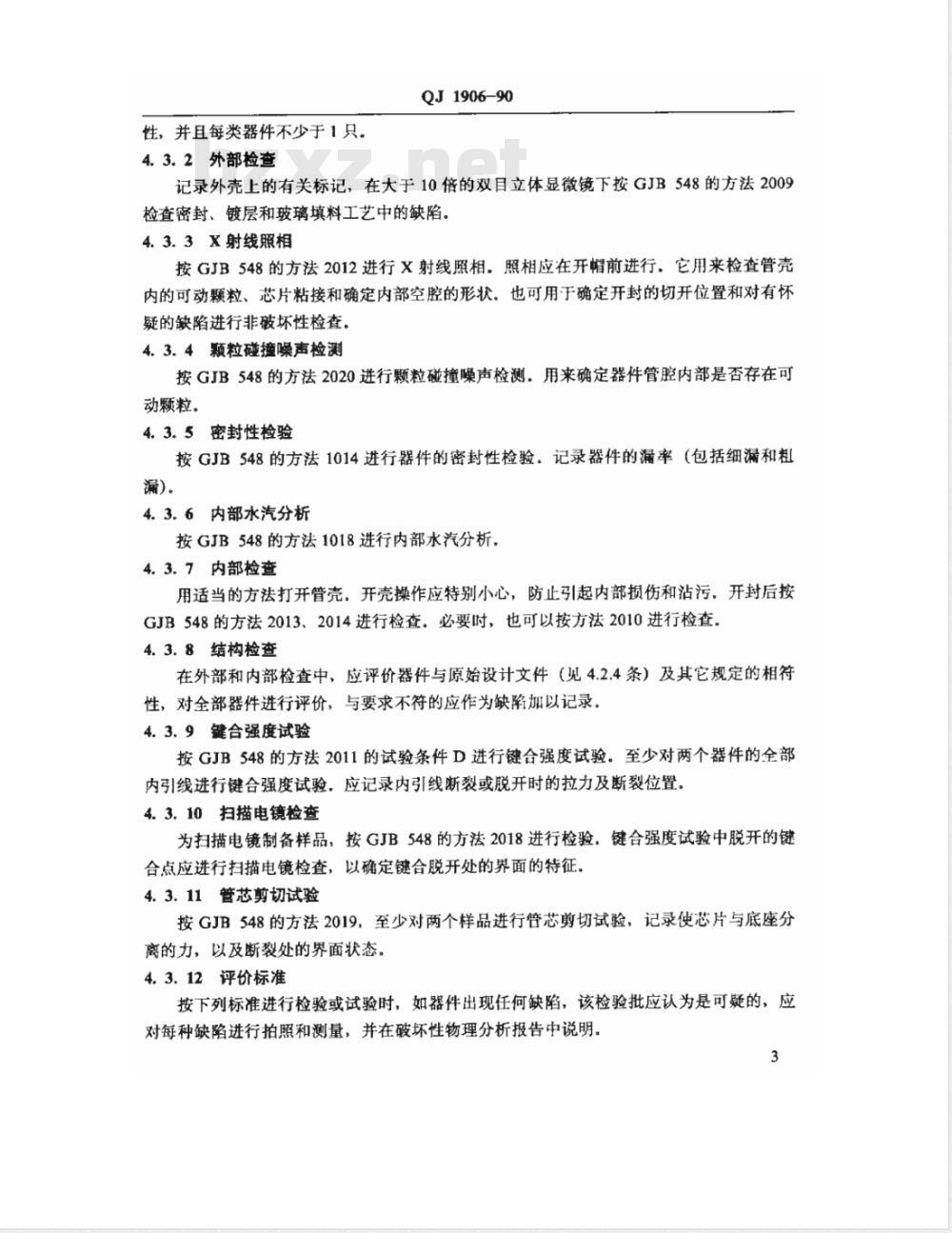
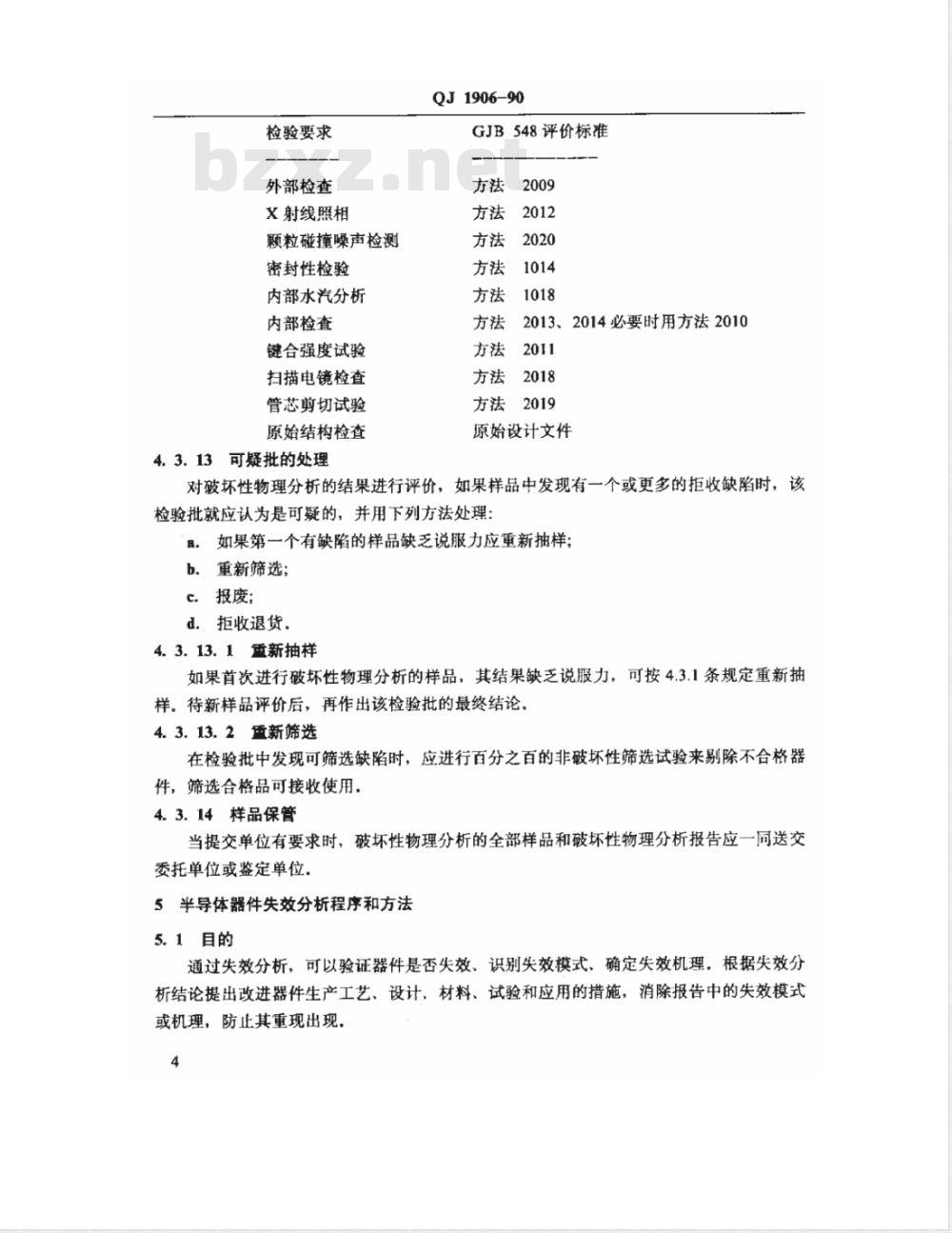
- 其它标准
- 热门标准
- 航天工业行业标准(QJ)
- QJ2616A-2004 石英谐振器筛选要求
- QJ797.2A-1997 机床夹具零件及部件 Ⅱ型胶接安装钻套
- QJ1931.5A-2005 电气简图绘制规则 第5部分:接线图
- QJ1092A-1998 科技档案管理表格
- QJ326A-2004 紧固件包装与贮存
- QJ1181.3A-1995 软磁合金的热处理 铁铝软磁合金的热处理
- QJ3199-2004 固体火箭发动机燃烧室壳体通用规范
- QJ3200-2004 航天产品设计文件标准化审查规定
- QJ2997A-2004 抗剪单齿钛合金环槽铆钉铆接工艺规范
- QJ1279A-1995 红外导引头术语
- QJ908A-1998 电子产品老炼试验方法
- QJ1453A-2004 固体火箭发动机燃烧室药柱通用规范
- QJ1714.1A-1999 航天产品设计文件管理制度 总则
- QJ1145.16A-2007 焊接夹具零件及部件 第16部分:肋板定位器
- QJ1145.35A-2007 焊接夹具零件及部件 第35部分:光面压块
- 行业新闻
请牢记:“bzxz.net”即是“标准下载”四个汉字汉语拼音首字母与国际顶级域名“.net”的组合。 ©2009 标准下载网 www.bzxz.net 本站邮件:bzxznet@163.com
网站备案号:湘ICP备2023016450号-1
网站备案号:湘ICP备2023016450号-1