- 您的位置:
- 标准下载网 >>
- 标准分类 >>
- 航空工业行业标准(HB) >>
- HB/Z 29-1981 电化学抛光工艺
标准号:
HB/Z 29-1981
标准名称:
电化学抛光工艺
标准类别:
航空工业行业标准(HB)
标准状态:
现行-
发布日期:
1982-01-30 -
实施日期:
1982-09-01 出版语种:
简体中文下载格式:
.rar.pdf下载大小:
6.72 MB
相关标签:
工艺

部分标准内容:
中华人民共和国第三机械工业部指导性技术文件
电化学抛光工艺
HB/Z29-81
中华人民共和国第机概工业部
指导性技术文件
电化学抛光工艺
HB/Z29-81
本文件规定了金属(包括钢、不锈钢、镍基合金、铜及铜合金、铝及铝合金)零件的电化学抛光工艺方法。
电化学抛光是指金属零件在特定条件下的阳极电化学加工方法,主要目的是使金属表面平整光亮。
1.应用范圈
1.1用作零件的精饰加工,从而使零件表面平整光亮,并能提高零件的反射系数和耐蚀能力。
1.2降低零件磨擦系数。
1.3作为电镀、氧化和焊接前的准备工序。1.4对用机械方法难以达到要求的弹性元件<波纹管、弹簧片、弹簧等》进行弹性和尺寸的修正。
1.5如呈现锻铸件、焊接件和加工零件上的各种冶金缺陷<如裂纹、松孔、熔渣、孔隙等,以供检验零件之用。
1.6用于制备金相试片。
2.工艺流程
2.1钢、不不锈钢、镍基合金零件电化学抛光工艺流程:2.1.1
电化学抛光前验收
有机溶剂除油按需要进行)
化学或电化学除油
热水洗
冷水洗
冷水洗
电化学抛光
2.1.10冷水洗
2.1.11冷水洗
第三机械工业部
六二一研究所
1982年9月1日
四三O厂
二二一厂
共12页
第2页
冷水洗
冷水洗
热水洗
2.1.19检验
HBZ29-81
注:①工序2.1.7和2.1.8根据零件表面状况视需要进行。电化学抛光后需要氧化,电镀的零件不进行工序2.1.17、2.1.18和2.1.20
②经吹砂的零件只进行工序2.1.3和2.1.9~2.1.20。2.2铜及铜合金零件电化学抛光工艺流程:2.2.1
电化学抛光前验收
有机溶剂除油《按需要进行》
化学或电化学除油
热水洗
冷水洗
予腐蚀
冷水洗
电化学抛光
冷水洗
冷水洗
冷水洗
冷水洗
涂油《按需要进行)
注:电化学抛光后需进行电镀、氧化的零件不进行工序2.2.15和2.2.18。铝及铝合金零件电化学抛光工艺流程:2.3
电化学抛光前验收
机械抛光(按需要进行)
有机溶剂除油<按需要进行)
化学除油
热水洗
冷水洗
冷水洗
电化学抛光
冷水洗
2.3.12冷水洗
冷水洗
2.3.16拆卸
2.3.17检验
主要工序说明
3.1电化学抛光前的验收
HB/Z29—81
电化学抛光前零件的表面质量应符合HB-5034-77的规定。3.2有机溶剂除油
按零件表面油污程度可分别选用石油醚、汽油等有机溶剂进行除油。3.3装挂
共12页
第3页
零件用专用或通用夹具进行装挂,夹具与零件应接触良好,该工序可移至电化学抛光前进行。
8.4化学或电化学除油
3.4.1钢铁零件化学除油溶液成份和工作条件如下:氢氧化钠
磷酸钠
碳酸钠
水玻璃
总碱度
<以NaOH计)
3.4.2钢铁零件电化学除油溶液成份和工作条件如下:氢氧化钠
磷硫钠
碳硫钠
水玻璃
总碱度
电流密度
(NaOH)
NagP0,12H20)
(Na2CO3·10H20)
(以NaOH计)
60~80克/升
20~40克/升
20~40克/升
3~10克/升
65~100克/升
70~90℃
除净为止
30~50克/升
20~30克/升
20~30克/升
3~5克/升
40~60克/升
60~80℃
3~10安培/分米2
阴极3~5分钟
共12页
第4页
电极材料
HB/Z29-81
阳极1~5分钟
钢板或镀镍钢板
注:①弹性或薄壁零件及>140公斤/毫米“的钢零件不允许阴极除油。②锡焊件不允许阳极除油。
③局部电化学抛光零件,当用蜡或可剥性塑料绝缘时,应在室温下进行除油。3.4.3铜及铜合金化学和电化学除油溶液成份:氢氧化钠
磷酸钠
碳酸钠
水玻璃
总碱度
(NasPO.12H.0)
<以NaOH计》
化学除油工作条件:
电化学除油工作条件:
电流密度
电极材料
5~15克/升
30~60克/升
20~25克/升
3~5克/升
15~30克/升
60~80℃
20分钟以内
50~80℃
1~5安培/分米
阴极3~10分钟
阳极30秒钟以内
钢板或镀镍钢板
注,局部电化学抛光的零件应当用蜡或可剥性塑料绝缘时,应在室温下进行除油。铝及铝合金化学除油溶液成份和工作条件如下3.4.4
磷酸钠水玻璃
合成洗衣粉
3.5腐蚀
50~70克/升
25~30克/升
8~12克/升
75~90℃
3~15分钟
3.5.1未经吹砂的碳钢零件可在下列任意一种溶液中进行腐蚀:盐酸
盐酸含量的0.4%
3.5.1.2盐酸(HC1,比重1.19)硫酸
50%以上<体积比》
10分钟以内
100~150克/升
100~150克/升
0.3~0.5克/升
10分钟以内
HB/Z29—81
注,①弹性或薄壁零件及0%<140公斤/毫米的钢零件不允许进行腐蚀。③膚蚀后的零件在下列溶液中进行除挂夹和接触铜:铬酐
(CrOs)
不锈钢零件在下列溶液中进行腐蚀:硝酸
氢氟酸
(HNO,比重1.42)
镍基合金在下列溶液中进行腐蚀:3.5.2
《HNOs,比重1.42)
氟化钠3.5.3铜及铜合金零件予腐蚀
共12页
90~150克/升
20~30克/升
除净为止
250~300克/升
90~110克/升
5~8分钟
50~60克/升
110~120克/升
3~5克/升
40~50℃
1~5分钟
具有氧化皮、氧化色的铜及铜合金零件在下列溶液中进行予腐蚀:盐酸
或盐酸
(H2SO4,比重1.84)
注:铍青铜零件表面有氧化皮时,可先在下列溶被中进行疏松氧化皮:氢氟化钠
3.6出光
bzxz.net
550~600克/升
2分钟以内
20~30克/升
50~80克/升
1~2分钟
450~500克/升
100~110℃
30~60分钟
3.6.1为了清除铝及铝合金除油后表面的腐蚀残余物可在下列溶液中出光:硝酸
《HNOs,比重1.42》
300~500克/升
出光为止
第5页
3.6.2为了除去电化学抛光后零件表面的氧化层,使电镀、氧化,阳极氧化工序正常进行和提高不进行电镀、氧化零件的防护能力,应在下列溶液中进行出光:3.6.2.1铜及铜合金出光溶液
共12页
第6页
HB/Z29—81
(H2S04,比重1.84)
铝及铝合金出光溶液成份和工作条件如下:硫酸
CrO。)
90~150克/升
20—30克/升
5~15秒
65~80克/升
15~20克/升
70~90℃
1~2分钟
镍基合金零件经电化学抛光后表面产生挂灰时,在下列溶液中出光:
3.7电化学抛光
250~300克/升
65~75℃
5~10分钟
3.7.1钢、不锈钢、镍基合金、镍铬合金零件在下列任意一种溶液中进行:3.7.1.1磷酸
溶液比重
阳极电流密度
注,①阴极为Pb-2铅板或铅合金<含锑6一8%>,阴极与阳极面积比为111~8。②此溶液适合抛光普通碳素钢、合金钢、不锈钢、镍基合金、铝及铝合金。3.7.1.2磷酸
柠檬酸
阴极电流密度
30~70安培/分米2
机加表面
吹砂表面
3.7.2铜及铜合金在下列任意一种溶液中进行:3.7.2.1磷酸
溶液比重
14001500克/升
160~200克/升
150~180克/升
70~90℃
12~20伏
25~60安培/分米
0.5~10分钟
730~950克/升
450~700克/升
1~2克/升
1~2克/升
18~60℃
1~5分钟
5~15分钟
10001100克/升
15~30℃
2~6伏
阳极电流密度
阳极材料
3.7.2.2磷酸
铬酐溶液比重
阳极电流密度
阴极材料
HB/Z29—81
Pb-2铝板或不锈钢板
(H,PO,比重1.7)
3.7.3铝及铝合金在下列任意~种溶液中进行:3.7.3.1磷酸
溶液比重
阳极电流密度
第7页
共12页
7~15安培/分米
根据需要而定
1200128。克/升
150~180克/升
20~40℃
8~14伏
30~50安培/分米2
15~20分钟
Pb-2铅板或铅锑合金<含锑6~8%)注:①阴极材料为Pb-2铅板或铅锑合金<含锑6~8%》板。②阴极与阳板面极比为1-1~8。3.7.8.2磷酸
阳极电流密度
阴极材料
150~180克/升
50~90℃
12~20伏
20~30安培/分米2
5~10分钟
100~130克/升
55~85℃
5~12伏
10~20安培/分米2
根据需要定
Pb-2铅板
注:电化学抛光过程中阳极应每隔10~15秒钟换向,1一2秒钟或移动一次。3.8中和
为了避免零件上残留的酸液带入镀槽、氧化槽或防止电化学抛光后的零件生锈,应在下列溶液中进行中和处理:
碳酸钠
3.9干燥
30~50克/升
1分钟以内
用干燥的热压缩空气吹干或在60~70℃的烘箱中烘干零件。共12页第8页
3.10检验
HB/Z29--81
电化学抛光后的零件质量检验按HB5054-77进行。3.11涂油
经检验合格的零件如果不进行电镀或氧化处理的,为防止生锈应随即浸涂防锈油。4.电化学抛光溶液的配制
电化学抛光溶液的配制是先在槽中将铬酐溶于少量水中,待搅拌溶解后,再向溶液中加入所需量的磷酸,然后加入硫酸或甘油。加硫酸时要同时搅拌电解液。待溶液冷却后测量比重,当比重低时应将电解液在90~100℃下加热,使水蒸发以达到规定比重,当比重高时可用水稀释。然后即可通电试抛,表面质量合格后即可正式用于生产。铜件电化学抛光溶液的配制是将规定量的磷酸溶于水中,使溶液的比重达到要求,经试抛合格后即可正式用于生产。
5.电化学抛光溶液的维护与调整电化学抛光是一种阳极电化学过程,在不含硫酸型的高温电解液中,在连续生产的猜况下,由于溶液的挥发及浓缩会使电解液比重增大。在工作过程巾中、电解液中聚集着三价铬和铁、铝离子或铜离子,这将使电解液的粘度增大和导电度降低,使金属表面的平整度及亮度降低,因此,需定期分析并调整电化学抛光溶液。5.1按分析数据添加各种类型电化学抛光溶液中的化学成份。5.2按比重计测量的数据,将电化学抛光溶液调整至最佳比重范围。5.3电解液的再生
电解液的再生是较困难的,目前还没有找到一种较好的、行之有效的方法来处理三价铬和铁离子。一般认为三价铬含量达30~50克/升,铁离子含量超过70克/升时,溶液即失效,需再生或更换。
三价铬可采用直接通电法处理。首先将电解液比重调整到1.68~1.72并加热到70℃以上,阳极用铅板,其面积应尽量大,使阳极电流密度在3~5安培/分米2,阴极面积应尽量小,使阴极电流密度达100安培/分米?左右,通电40安培/小时可使6克/升三价铬氧化成六价铬。一般认为电解液使用寿命为150安培小时/升。6.溶液的分析项目与周期(见表1)表1
化学除油和电化学除油溶液
松皮溶液
出光溶液
钢铁电化学抛光溶液
①磷酸、硫酸、铬酐型
②磷酸、硫酸型
③磷酸、铬酐型
总碱度
氢氧化钠,亚硝酸钠
杂质三价铬和铁
杂质三价铬
杂质三价铬
分析周期
2—4周
按需进行
11~2周
1~2周
1~2周
铜及铜合金电化学抛光溶液
铝及铝合金电化学抛光溶液
出光溶液(铜及铜合金用)
不锈钢蚀腐液溶
镍基合金腐蚀溶液
HB/Z29--81
硫酸铬酐
硝酸氢氟酸
硫酸、硝酸、氟化钠
电化学抛光常见故障及排除方法目
共12页
第9页
续表1
分析周期
2—4周
1—2周
2—4周
杂质铜离子
杂质铝离子
视情况更换
视情况更换
7.1钢、不锈钢、镍基合金电化学抛光常见故障的产生原因及排除方法(见表2)表2
故障特征
零件表面发白,
无光泽
点状腐蚀
电化学抛光表面光泽
但稍带兰彩色
电化学抛光表面无光
泽且有黄色斑点
电化学抛光表面有棕
褐色薄膜
表面光亮但平整度不
电化学抛光表面有白
色条纹
表面无光泽,带有暗
褐色斑点
表面糙粗无光泽呈暗
排除方法
①接触不良
检查装挂夹具使其接触良好,提高②电流密度和电压低,而温度过高、电流密度及电压降低温度使其在正产生化学浸蚀
①电解液中有铬酐的悬浮物
②溶液比重超过1.82
①电解液配制后未经通电处理
②电解液温度低
电解液比重小于1.7
电解液比重过高
抛光时间短,原表面光洁度太低常工艺规范内
用水稀释到规定比重并在90-100℃加热电解液直到酐全部溶解
新配电解液应加热并通电处理试抛,合格后才能用于生产,提高电解液温度到规定范围内
加热电解液,使比重达到规定值将电解液比重稀释至1.74,并在90—100℃下加热1小时
延长抛光时间提高原表面光洁度电解液比重大于1.82
硫酸铬酐含将电解液比重稀释至1.74,并在90量低
-100℃下加热1小时,根据化验结果调整溶液
三价铬浓度大于30克/升
氧化三价铬
三价铁浓度天宇60克/升电解液温更换电解液度过高,阳极电流密度过大,零件将温度和电流密度控制在工艺规范与挂具接触不良。
内检查装夹点,使其牢固
电解液组成不当、对零件起化学腐分析电解液并进行调整部分或全部蚀,溶液中三价铁浓度超过60克/升更换电解液。共12页
第10页
故障特征
零件凹入处、零件与
挂具接触处附近呈银
百色或暗灰色斑点,
条纹。
表面局部有光泽,局
部无光泽且粗糙
表面虽呈光滑半光泽
状态,但复盖一层灰
色或兰色的薄膜
零件表面有条纹状腐
蚀或边缘和孔附近有
采用正确的工艺参数
却长时间抛不亮
零件从槽中取出后立
即出现褐色斑点
HB/Z29—81
生产原因
排除方
续表2
零件在槽中位置不当,电解液中三改善零件在槽中位置,氧化三价铬,价铁浓度超过50克/升,三价铬超部分或全部更换电解液过40克/升
溶液比重低于1.6,电压、电流密度加热电解液使比重提高到规定值,低。
提高电压、电流密度到规定值。合金中含有钒、锰等元素。
三价铬浓度超过30克/升
铬氧化三价
电解液温度高,电化学抛光时间太降低溶液温度缩短抛光耐间,增加长、长时间抛光中间清洗次数少,中间清洗次数。零件装挂位置不正确
改善零件的装夹点
电解液成分不正常、三价铬浓度超分析电解液进行调整,氧化三价铬过40克/升,三价铁超过60克/升以或更换电解液上
电解液中磷酸含量低,电化学抛光经分析后调整电解液延长抛光时间时间太短
7.2铜及铜合金电化学抛光常见故障的产生原因及排除方法(见表3)。表3
故障特征
零件表面无光泽且粗
表面光泽不一致,有
条纹状腐蚀
表面有点状腐蚀<麻
坑、花斑等》
表面无光泽
溶液中混入硫酸
排除方
加入碳酸钡使硫酸根沉淀,过滤后分析校正之
零件与挂具接触不良,零件在槽中检查装夹点,使其牢固,改善零件在槽中位置,缩短抛光时间
位置不对,抛光时间太长
溶液比重过大,抛光时间长,溶液调整溶液比重,缩短抛光时间。长太旧
时间抛光时中间应加强清洗,补添或更换部分溶液
溶液温度过高,比重不在规定之内降低溶液温度测量比重进行调整,添加磷酸或水
铝及铝合金电化学抛光常见故障产生的原因及排除方法(见表4)
小提示:此标准内容仅展示完整标准里的部分截取内容,若需要完整标准请到上方自行免费下载完整标准文档。
电化学抛光工艺
HB/Z29-81
中华人民共和国第机概工业部
指导性技术文件
电化学抛光工艺
HB/Z29-81
本文件规定了金属(包括钢、不锈钢、镍基合金、铜及铜合金、铝及铝合金)零件的电化学抛光工艺方法。
电化学抛光是指金属零件在特定条件下的阳极电化学加工方法,主要目的是使金属表面平整光亮。
1.应用范圈
1.1用作零件的精饰加工,从而使零件表面平整光亮,并能提高零件的反射系数和耐蚀能力。
1.2降低零件磨擦系数。
1.3作为电镀、氧化和焊接前的准备工序。1.4对用机械方法难以达到要求的弹性元件<波纹管、弹簧片、弹簧等》进行弹性和尺寸的修正。
1.5如呈现锻铸件、焊接件和加工零件上的各种冶金缺陷<如裂纹、松孔、熔渣、孔隙等,以供检验零件之用。
1.6用于制备金相试片。
2.工艺流程
2.1钢、不不锈钢、镍基合金零件电化学抛光工艺流程:2.1.1
电化学抛光前验收
有机溶剂除油按需要进行)
化学或电化学除油
热水洗
冷水洗
冷水洗
电化学抛光
2.1.10冷水洗
2.1.11冷水洗
第三机械工业部
六二一研究所
1982年9月1日
四三O厂
二二一厂
共12页
第2页
冷水洗
冷水洗
热水洗
2.1.19检验
HBZ29-81
注:①工序2.1.7和2.1.8根据零件表面状况视需要进行。电化学抛光后需要氧化,电镀的零件不进行工序2.1.17、2.1.18和2.1.20
②经吹砂的零件只进行工序2.1.3和2.1.9~2.1.20。2.2铜及铜合金零件电化学抛光工艺流程:2.2.1
电化学抛光前验收
有机溶剂除油《按需要进行》
化学或电化学除油
热水洗
冷水洗
予腐蚀
冷水洗
电化学抛光
冷水洗
冷水洗
冷水洗
冷水洗
涂油《按需要进行)
注:电化学抛光后需进行电镀、氧化的零件不进行工序2.2.15和2.2.18。铝及铝合金零件电化学抛光工艺流程:2.3
电化学抛光前验收
机械抛光(按需要进行)
有机溶剂除油<按需要进行)
化学除油
热水洗
冷水洗
冷水洗
电化学抛光
冷水洗
2.3.12冷水洗
冷水洗
2.3.16拆卸
2.3.17检验
主要工序说明
3.1电化学抛光前的验收
HB/Z29—81
电化学抛光前零件的表面质量应符合HB-5034-77的规定。3.2有机溶剂除油
按零件表面油污程度可分别选用石油醚、汽油等有机溶剂进行除油。3.3装挂
共12页
第3页
零件用专用或通用夹具进行装挂,夹具与零件应接触良好,该工序可移至电化学抛光前进行。
8.4化学或电化学除油
3.4.1钢铁零件化学除油溶液成份和工作条件如下:氢氧化钠
磷酸钠
碳酸钠
水玻璃
总碱度
3.4.2钢铁零件电化学除油溶液成份和工作条件如下:氢氧化钠
磷硫钠
碳硫钠
水玻璃
总碱度
电流密度
(NaOH)
NagP0,12H20)
(Na2CO3·10H20)
(以NaOH计)
60~80克/升
20~40克/升
20~40克/升
3~10克/升
65~100克/升
70~90℃
除净为止
30~50克/升
20~30克/升
20~30克/升
3~5克/升
40~60克/升
60~80℃
3~10安培/分米2
阴极3~5分钟
共12页
第4页
电极材料
HB/Z29-81
阳极1~5分钟
钢板或镀镍钢板
注:①弹性或薄壁零件及>140公斤/毫米“的钢零件不允许阴极除油。②锡焊件不允许阳极除油。
③局部电化学抛光零件,当用蜡或可剥性塑料绝缘时,应在室温下进行除油。3.4.3铜及铜合金化学和电化学除油溶液成份:氢氧化钠
磷酸钠
碳酸钠
水玻璃
总碱度
(NasPO.12H.0)
<以NaOH计》
化学除油工作条件:
电化学除油工作条件:
电流密度
电极材料
5~15克/升
30~60克/升
20~25克/升
3~5克/升
15~30克/升
60~80℃
20分钟以内
50~80℃
1~5安培/分米
阴极3~10分钟
阳极30秒钟以内
钢板或镀镍钢板
注,局部电化学抛光的零件应当用蜡或可剥性塑料绝缘时,应在室温下进行除油。铝及铝合金化学除油溶液成份和工作条件如下3.4.4
磷酸钠
合成洗衣粉
3.5腐蚀
50~70克/升
25~30克/升
8~12克/升
75~90℃
3~15分钟
3.5.1未经吹砂的碳钢零件可在下列任意一种溶液中进行腐蚀:盐酸
3.5.1.2盐酸(HC1,比重1.19)硫酸
10分钟以内
100~150克/升
100~150克/升
0.3~0.5克/升
10分钟以内
HB/Z29—81
注,①弹性或薄壁零件及0%<140公斤/毫米的钢零件不允许进行腐蚀。③膚蚀后的零件在下列溶液中进行除挂夹和接触铜:铬酐
(CrOs)
氢氟酸
(HNO,比重1.42)
镍基合金在下列溶液中进行腐蚀:3.5.2
氟化钠
共12页
90~150克/升
20~30克/升
除净为止
250~300克/升
90~110克/升
5~8分钟
50~60克/升
110~120克/升
3~5克/升
40~50℃
1~5分钟
具有氧化皮、氧化色的铜及铜合金零件在下列溶液中进行予腐蚀:盐酸
或盐酸
注:铍青铜零件表面有氧化皮时,可先在下列溶被中进行疏松氧化皮:氢氟化钠
3.6出光
550~600克/升
2分钟以内
20~30克/升
50~80克/升
1~2分钟
450~500克/升
100~110℃
30~60分钟
3.6.1为了清除铝及铝合金除油后表面的腐蚀残余物可在下列溶液中出光:硝酸
《HNOs,比重1.42》
300~500克/升
出光为止
第5页
3.6.2为了除去电化学抛光后零件表面的氧化层,使电镀、氧化,阳极氧化工序正常进行和提高不进行电镀、氧化零件的防护能力,应在下列溶液中进行出光:3.6.2.1铜及铜合金出光溶液
共12页
第6页
HB/Z29—81
(H2S04,比重1.84)
铝及铝合金出光溶液成份和工作条件如下:硫酸
90~150克/升
20—30克/升
5~15秒
65~80克/升
15~20克/升
70~90℃
1~2分钟
镍基合金零件经电化学抛光后表面产生挂灰时,在下列溶液中出光:
3.7电化学抛光
250~300克/升
65~75℃
5~10分钟
3.7.1钢、不锈钢、镍基合金、镍铬合金零件在下列任意一种溶液中进行:3.7.1.1磷酸
溶液比重
阳极电流密度
柠檬酸
阴极电流密度
机加表面
吹砂表面
3.7.2铜及铜合金在下列任意一种溶液中进行:3.7.2.1磷酸
溶液比重
14001500克/升
160~200克/升
150~180克/升
70~90℃
12~20伏
25~60安培/分米
0.5~10分钟
730~950克/升
450~700克/升
1~2克/升
1~2克/升
18~60℃
1~5分钟
5~15分钟
10001100克/升
15~30℃
2~6伏
阳极电流密度
阳极材料
3.7.2.2磷酸
铬酐
阳极电流密度
阴极材料
HB/Z29—81
Pb-2铝板或不锈钢板
(H,PO,比重1.7)
3.7.3铝及铝合金在下列任意~种溶液中进行:3.7.3.1磷酸
溶液比重
阳极电流密度
第7页
共12页
7~15安培/分米
根据需要而定
1200128。克/升
150~180克/升
20~40℃
8~14伏
30~50安培/分米2
15~20分钟
Pb-2铅板或铅锑合金<含锑6~8%)
阳极电流密度
阴极材料
150~180克/升
50~90℃
12~20伏
20~30安培/分米2
5~10分钟
55~85℃
5~12伏
10~20安培/分米2
根据需要定
Pb-2铅板
注:电化学抛光过程中阳极应每隔10~15秒钟换向,1一2秒钟或移动一次。3.8中和
为了避免零件上残留的酸液带入镀槽、氧化槽或防止电化学抛光后的零件生锈,应在下列溶液中进行中和处理:
碳酸钠
3.9干燥
30~50克/升
1分钟以内
用干燥的热压缩空气吹干或在60~70℃的烘箱中烘干零件。共12页第8页
3.10检验
HB/Z29--81
电化学抛光后的零件质量检验按HB5054-77进行。3.11涂油
经检验合格的零件如果不进行电镀或氧化处理的,为防止生锈应随即浸涂防锈油。4.电化学抛光溶液的配制
电化学抛光溶液的配制是先在槽中将铬酐溶于少量水中,待搅拌溶解后,再向溶液中加入所需量的磷酸,然后加入硫酸或甘油。加硫酸时要同时搅拌电解液。待溶液冷却后测量比重,当比重低时应将电解液在90~100℃下加热,使水蒸发以达到规定比重,当比重高时可用水稀释。然后即可通电试抛,表面质量合格后即可正式用于生产。铜件电化学抛光溶液的配制是将规定量的磷酸溶于水中,使溶液的比重达到要求,经试抛合格后即可正式用于生产。
5.电化学抛光溶液的维护与调整电化学抛光是一种阳极电化学过程,在不含硫酸型的高温电解液中,在连续生产的猜况下,由于溶液的挥发及浓缩会使电解液比重增大。在工作过程巾中、电解液中聚集着三价铬和铁、铝离子或铜离子,这将使电解液的粘度增大和导电度降低,使金属表面的平整度及亮度降低,因此,需定期分析并调整电化学抛光溶液。5.1按分析数据添加各种类型电化学抛光溶液中的化学成份。5.2按比重计测量的数据,将电化学抛光溶液调整至最佳比重范围。5.3电解液的再生
电解液的再生是较困难的,目前还没有找到一种较好的、行之有效的方法来处理三价铬和铁离子。一般认为三价铬含量达30~50克/升,铁离子含量超过70克/升时,溶液即失效,需再生或更换。
三价铬可采用直接通电法处理。首先将电解液比重调整到1.68~1.72并加热到70℃以上,阳极用铅板,其面积应尽量大,使阳极电流密度在3~5安培/分米2,阴极面积应尽量小,使阴极电流密度达100安培/分米?左右,通电40安培/小时可使6克/升三价铬氧化成六价铬。一般认为电解液使用寿命为150安培小时/升。6.溶液的分析项目与周期(见表1)表1
化学除油和电化学除油溶液
松皮溶液
出光溶液
钢铁电化学抛光溶液
①磷酸、硫酸、铬酐型
②磷酸、硫酸型
③磷酸、铬酐型
总碱度
氢氧化钠,亚硝酸钠
杂质三价铬和铁
杂质三价铬
杂质三价铬
分析周期
2—4周
按需进行
11~2周
1~2周
1~2周
铜及铜合金电化学抛光溶液
铝及铝合金电化学抛光溶液
出光溶液(铜及铜合金用)
不锈钢蚀腐液溶
镍基合金腐蚀溶液
HB/Z29--81
硫酸铬酐
硝酸氢氟酸
硫酸、硝酸、氟化钠
电化学抛光常见故障及排除方法目
共12页
第9页
续表1
分析周期
2—4周
1—2周
2—4周
杂质铜离子
杂质铝离子
视情况更换
视情况更换
7.1钢、不锈钢、镍基合金电化学抛光常见故障的产生原因及排除方法(见表2)表2
故障特征
零件表面发白,
无光泽
点状腐蚀
电化学抛光表面光泽
但稍带兰彩色
电化学抛光表面无光
泽且有黄色斑点
电化学抛光表面有棕
褐色薄膜
表面光亮但平整度不
电化学抛光表面有白
色条纹
表面无光泽,带有暗
褐色斑点
表面糙粗无光泽呈暗
排除方法
①接触不良
检查装挂夹具使其接触良好,提高②电流密度和电压低,而温度过高、电流密度及电压降低温度使其在正产生化学浸蚀
①电解液中有铬酐的悬浮物
②溶液比重超过1.82
①电解液配制后未经通电处理
②电解液温度低
电解液比重小于1.7
电解液比重过高
抛光时间短,原表面光洁度太低常工艺规范内
用水稀释到规定比重并在90-100℃加热电解液直到酐全部溶解
新配电解液应加热并通电处理试抛,合格后才能用于生产,提高电解液温度到规定范围内
加热电解液,使比重达到规定值将电解液比重稀释至1.74,并在90—100℃下加热1小时
延长抛光时间提高原表面光洁度电解液比重大于1.82
硫酸铬酐含将电解液比重稀释至1.74,并在90量低
-100℃下加热1小时,根据化验结果调整溶液
三价铬浓度大于30克/升
氧化三价铬
三价铁浓度天宇60克/升电解液温更换电解液度过高,阳极电流密度过大,零件将温度和电流密度控制在工艺规范与挂具接触不良。
内检查装夹点,使其牢固
电解液组成不当、对零件起化学腐分析电解液并进行调整部分或全部蚀,溶液中三价铁浓度超过60克/升更换电解液。共12页
第10页
故障特征
零件凹入处、零件与
挂具接触处附近呈银
百色或暗灰色斑点,
条纹。
表面局部有光泽,局
部无光泽且粗糙
表面虽呈光滑半光泽
状态,但复盖一层灰
色或兰色的薄膜
零件表面有条纹状腐
蚀或边缘和孔附近有
采用正确的工艺参数
却长时间抛不亮
零件从槽中取出后立
即出现褐色斑点
HB/Z29—81
生产原因
排除方
续表2
零件在槽中位置不当,电解液中三改善零件在槽中位置,氧化三价铬,价铁浓度超过50克/升,三价铬超部分或全部更换电解液过40克/升
溶液比重低于1.6,电压、电流密度加热电解液使比重提高到规定值,低。
提高电压、电流密度到规定值。合金中含有钒、锰等元素。
三价铬浓度超过30克/升
铬氧化三价
电解液温度高,电化学抛光时间太降低溶液温度缩短抛光耐间,增加长、长时间抛光中间清洗次数少,中间清洗次数。零件装挂位置不正确
改善零件的装夹点
电解液成分不正常、三价铬浓度超分析电解液进行调整,氧化三价铬过40克/升,三价铁超过60克/升以或更换电解液上
电解液中磷酸含量低,电化学抛光经分析后调整电解液延长抛光时间时间太短
7.2铜及铜合金电化学抛光常见故障的产生原因及排除方法(见表3)。表3
故障特征
零件表面无光泽且粗
表面光泽不一致,有
条纹状腐蚀
表面有点状腐蚀<麻
坑、花斑等》
表面无光泽
溶液中混入硫酸
排除方
加入碳酸钡使硫酸根沉淀,过滤后分析校正之
零件与挂具接触不良,零件在槽中检查装夹点,使其牢固,改善零件在槽中位置,缩短抛光时间
位置不对,抛光时间太长
溶液比重过大,抛光时间长,溶液调整溶液比重,缩短抛光时间。长太旧
时间抛光时中间应加强清洗,补添或更换部分溶液
溶液温度过高,比重不在规定之内降低溶液温度测量比重进行调整,添加磷酸或水
铝及铝合金电化学抛光常见故障产生的原因及排除方法(见表4)
小提示:此标准内容仅展示完整标准里的部分截取内容,若需要完整标准请到上方自行免费下载完整标准文档。

标准图片预览:
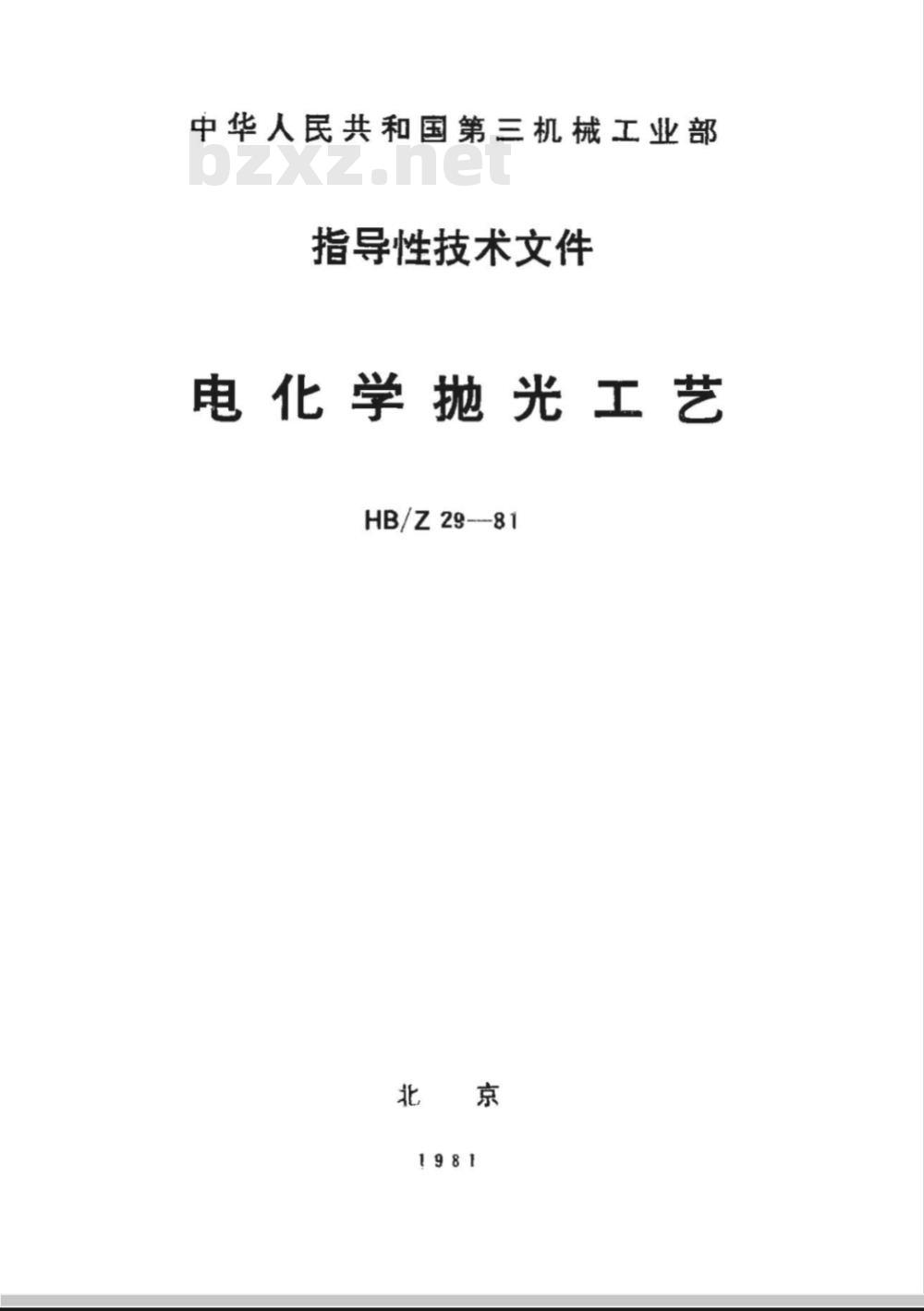
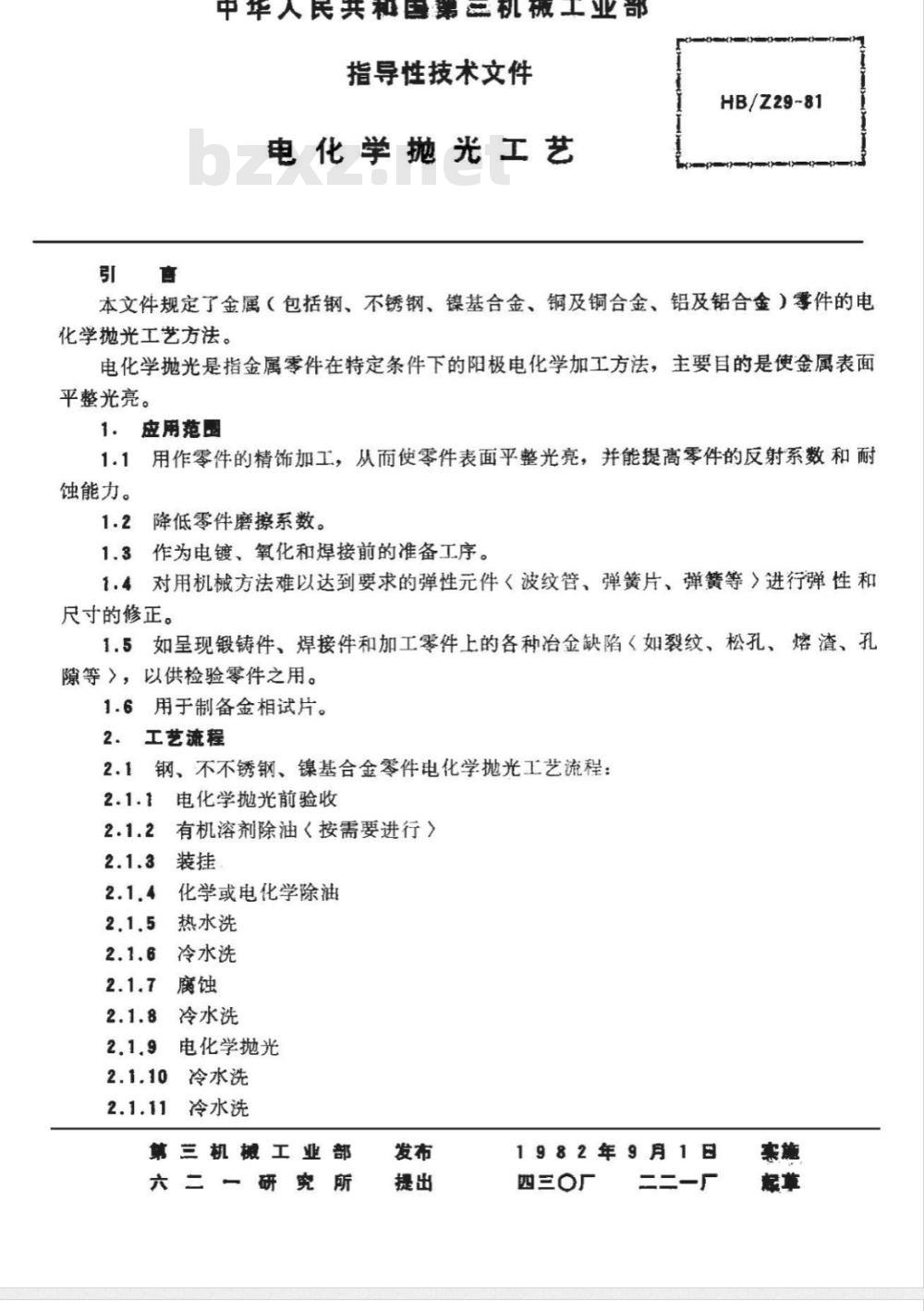
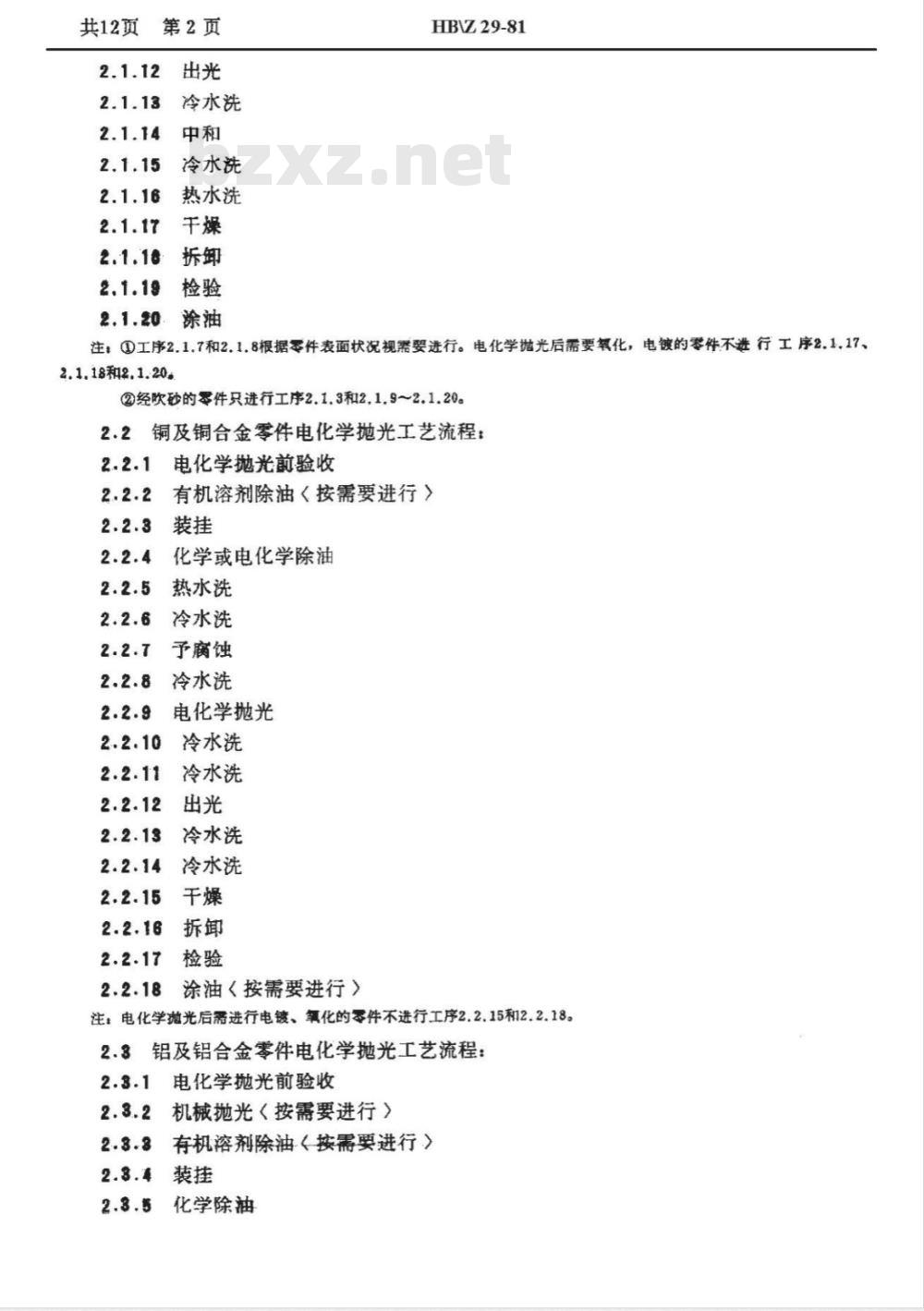
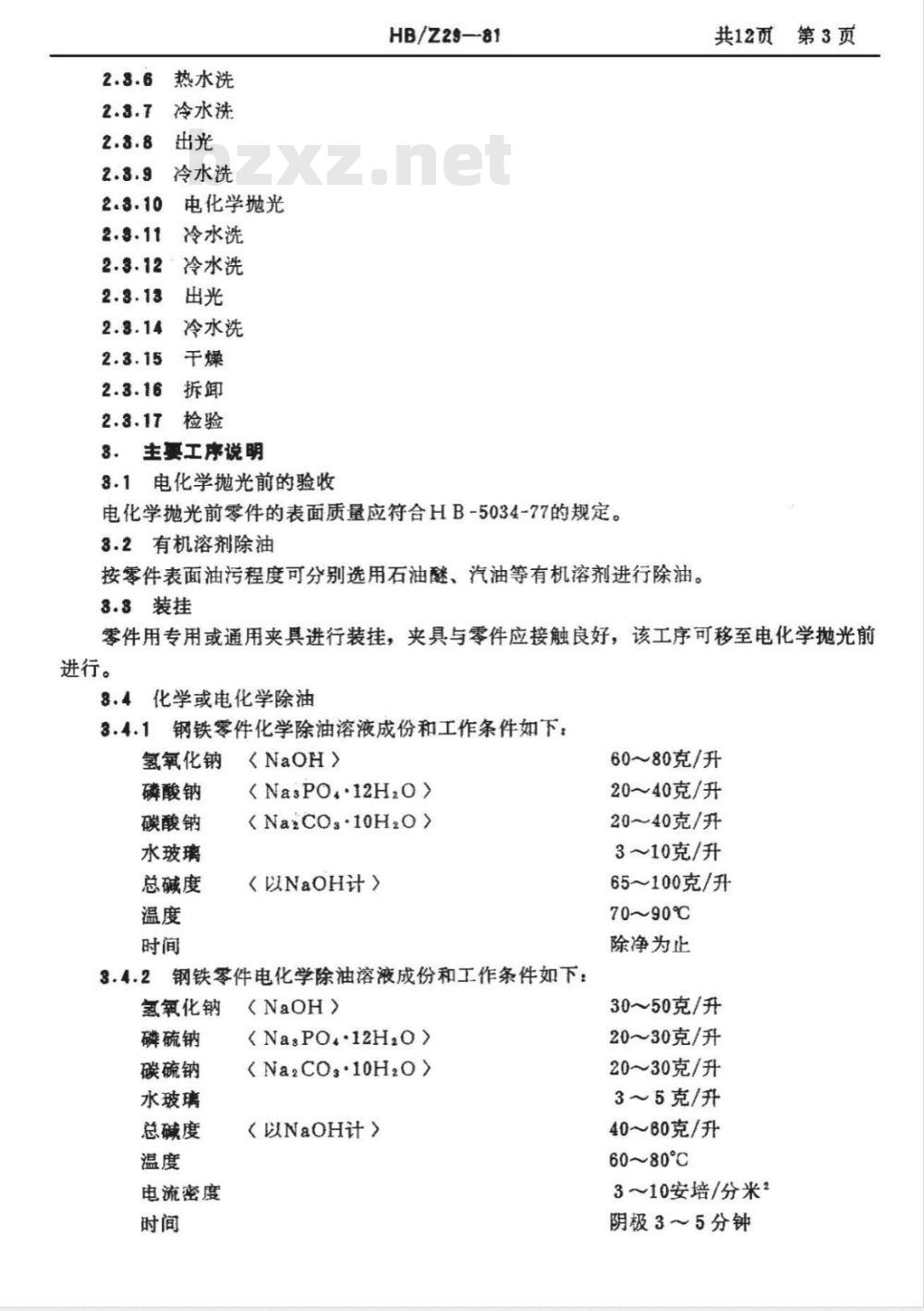
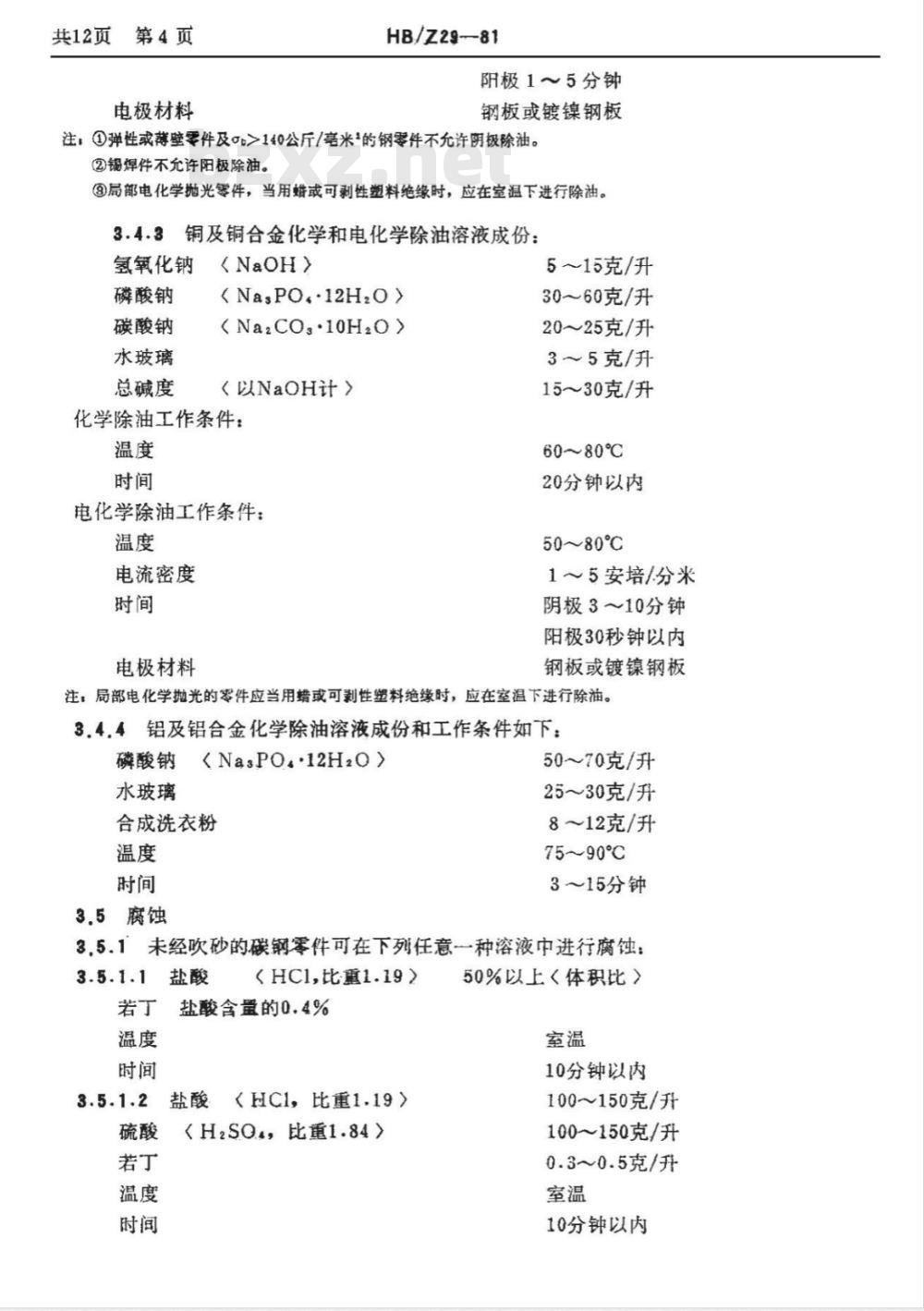
- 其它标准
- 热门标准
- 航空工业行业标准(HB)
- HB2-1972-1983 双盘快卸锁
- HB5453-2004 铝合金化学铣切保护涂料规范
- HB4-1969-2002 扩口式管接头的堵盖
- HB780-1973 1~8级精度用套量头双头光面塞规D>30~80mm
- HB786-1973 1~9级精度用双头组合卡规D=0.1~3mm
- HB2-1971-1983 轻型快卸锁
- HB782-1973 1~8级精度用非全形单头带柄光面塞规D>80~180mm
- HB6025-6027-2008 21MPa无扩口过隔板三通管接头
- HB776-1973 1~8级精度用针式双头光面塞规D=0.1~3mm
- HB1603-1987 球头螺钉
- HB3719-1986 铆枪用平窝头(d=18~30)
- HB4530.18-1991 H型孔系组合夹具压板类件 摆动压板
- HB7146.3-1995 大型系列组合夹具导向件 角铁形镗孔支承
- HB1426-1987 侧向压紧器
- HB4530.13-1991 H型孔系组合夹具压板类件 偏心轮夹紧组件
- 行业新闻
请牢记:“bzxz.net”即是“标准下载”四个汉字汉语拼音首字母与国际顶级域名“.net”的组合。 ©2009 标准下载网 www.bzxz.net 本站邮件:bzxznet@163.com
网站备案号:湘ICP备2023016450号-1
网站备案号:湘ICP备2023016450号-1