- 您的位置:
- 标准下载网 >>
- 标准分类 >>
- 铁路运输行业标准(TB) >>
- TB/T 1400.2-2018 机车用有箍车轮第2部分:轮箍
标准号:
TB/T 1400.2-2018
标准名称:
机车用有箍车轮第2部分:轮箍
标准类别:
铁路运输行业标准(TB)
标准状态:
现行出版语种:
简体中文下载格式:
.zip .pdf下载大小:
18.82 MB

点击下载
标准简介:
TB/T 1400.2-2018.Wheel with tyre for railway locomotive-Part 2: Rough-rolled tyres.
1范围
TB/T 1400.2规定了铁路机车用粗制轮箍和成品轮箍的型式尺寸、技术要求和检验方法、检验规则、标志、包装及防护、质量证明书。
TB/T 1400.2适用于最高运行速度不大于200 km/h及轴重不大于26 t的机车用轮箍的制造、订货和检验。
2规范性引 用文件
下列文件中对于本文件的应用是必不可少的。凡是注日期的引用文件,仅注日期的版本适用于本文件。凡是不注日期的引用文件,其最新版本(包括所有的修改单)适用于本文件。
GB/T 223钢铁及合金 化学分析方法
GB/T 226钢的 低倍组织及缺陷酸蚀检验法
GB/T 228.1金属材料 拉伸试验 第1部分:室温试验方法
GB/T229金属材料夏比摆锤冲击试验方法
GB/T 231.1金 属材料布氏硬度试验第1部分:试验方法.
GB/T4336碳素钢和中低合金钢 多元素 含量的测定火 花放电原子发射光谱法(常规法)
GB/T 6394金属平均晶粒度测定方法
GB/T 9445无损检测人 员资格鉴定与认证
GB/T10561--2005钢中非金属夹杂物含量的测定标准评级图显微检验法
GB/T 13298金属显微组织检验方法
GB/T 15822.2无损检测 磁粉检测 第2 部分:检测介质
GB/T 15822.3无损检测 磁粉检测第3 部分:设备
GB/T20066钢和铁化学成分测定用试样的取样和制样方法

部分标准内容:
中华人民共和国铁道行业标准
TB/T1400.2-2018
代替TB/T1882—2001,TB/T2015—2001,部分代替TB/T2995—2000机车用有箍车轮
第2部分:轮箍
Wheel with tyre for railway locomotive-Part 2: Rough-rolled tyres
2018-07-31发布
国家铁路局
2019-02-01实施
规范性引用文件
型式尺寸
技术要求和检验方法
检验规则
包装及防护
质量证明书
附录A(规范性附录)
附录B(规范性附录)
附录C(规范性附录)
附录D(规范性附录)
轮箍钢氢含量检测方法
轮箍低倍组织缺陷评级图谱
超声波检测方法
磁粉检测方法
TB/T1400.2—2018
TB/T1400《机车用有箍车轮》分为两个部分:第1部分:轮心;
第2部分:轮箍。
本部分为TB/T1400的第2部分。
本部分按照GB/T1.1一2009给出的规则起草。TB/T1400.2—2018
本部分代替TB/T1882一2001《铁路机车用粗制轮箍订货技术条件》、TB/T2015一2001《铁路机车用粗制轮箍型式尺寸》,代替TB/T2995一2000《铁道车轮和轮箍超声波检验》中轮箍探伤部分。本部分与TB/T1882—2001、TB/T2015—2001和TB/T2995—2000相比,除编辑性修改外,主要技术变化如下:
本部分内容结构有所变动,将技术要求与检验方法并为一章:删除了无缘轮箍型式(B型)(见TB/T2015一2001年版的4.1);删除了粗制轮箍外径为846mm1006mm、1106mm、1126mm、1376mm、1506mm、1756mm规格的轮箍(见TB/T2015一2001年版的表1);修改了化学成分中P、S元素的要求(见表2,TB/T1882一2001年版的3.3.1);-增加了Cr、Cu、Mo、Ni、V元素的允许偏差(见表3,TB/T1882一2001年版的3.3.2);修改了冲击性能要求的单位,冲击性能要求的指标进行了相应换算,增加了轮箍20℃冲击的单值要求(见表5,TB/T1882—2001年版的3.5);修改了非金属夹杂物的级别要求(见表7,TB/T1882一2001年版的3.7);-删除了复验规则(见TB/T1882一2001年版的第6章);-增加了规范性附录“轮箍钢氢含量检测方法”(见附录A):-增加了规范性附录“轮箍低倍组织缺陷评级图谱”(见附录B);修改了超声波检测方法(见附录C,TB/T2995一2000年版的第7章);修改了磁粉检测方法(见附录D,TB/T1882一2001年版的4.9)。本部分由中国铁道科学研究院集团有限公司标准计量研究所提出并归口。本部分起草单位:中国铁道科学研究院集团有限公司金属及化学研究所、中国铁道科学研究院集团有限公司标准计量研究所、马鞍山钢铁股份有限公司、中车戚墅堰机车有限公司、中车株洲电力机车有限公司、中车大连机车车辆有限公司。本部分主要起草人:张关震、高俊莉、丛韬、肖峰、黄永巍、冯绍艳罗彦云、高宏宇。本部分所代替标准的历次版本发布情况:TB/T1882—1987、TB/T1882—2001;—TB/T2015—1987、TB/T2015-2001—TB/T2046—1989;
-TB/T2882—1998;
TB/T2995—2000。
1范围
机车用有箍车轮
第2部分:轮箍
TB/T1400.2—2018
TB/T1400的本部分规定了铁路机车用粗制轮箍和成品轮箍的型式尺寸、技术要求和检验方法、检验规则、标志、包装及防护、质量证明书。本部分适用于最高运行速度不大于200km/h及轴重不大于26t的机车用轮箍的制造、订货和检验。
2规范性引用文件
下列文件中对于本文件的应用是必不可少的。凡是注日期的引用文件,仅注日期的版本适用于本文件。凡是不注日期的引用文件,其最新版本(包括所有的修改单)适用于本文件。3钢铁及合金化学分析方法
GB/T223
GB/T226钢的低倍组织及缺陷酸蚀检验法金属材料拉伸试验第1部分:室温试验方法GB/T228.1
GB/T229金属材料夏比摆锤冲击试验方法金属材料布氏硬度试验第1部分:试验方法GB/T231.1
GB/T4336
GB/T6394
GB/T9445
碳素钢和中低合金钢多元素含量的测定火花放电原子发射光谱法(常规法)金属平均晶粒度测定方法
无损检测人员资格鉴定与认证
钢中非金属夹杂物含量的测定标准评级图显微检验法GB/T10561—2005
金属显微组织检验方法
GB/T13298
CB/T15822.2无损检测磁粉检测货第2部分:检测介质
GB/T15822.3
无损检测磁粉检测第3部分:设备GB/T20066
GB/T20123
GB/T20125
化学成分测定用试样的取样和制样方法钢和铁
总碳硫含量的测定高频感应炉燃烧后红外吸收法(常规方法)钢铁
多元素的测定电感耦合等离子体发射光谱法低合金钢
GB/T27664.1—2011
GB/T27664.2—2011
GB/T27664.3—2012
无损检测
超声检测设备的性能与检验第1部分:仪器无损检测
超声检测设备的性能与检验第2部分:探头超声检测设备的性能与检验第3部分:组合设备无损检测此内容来自标准下载网
IS06933:1986铁道机车车辆材料磁粉探伤验收试验(Railwayrollingstockmateria一Magneticparticle acceptance testing)3型式尺寸
3.1粗制轮箍的型式尺寸、尺寸极限偏差及形位公差见图1;成品轮箍的型式尺寸、尺寸极限偏差及形位公差应符合经规定程序批准的产品图样。3.2轮箍的尺寸规格见表1。
TB/T1400.2-2018
注:图中双点划线为成品尺寸轮廊线示意。图1
粗制轮箍型式尺寸
轮箍尺寸规格
外径D,
粗制尺寸
内径d,
宽B,
27 ±2
1:10
成品尺寸
外径D
注:表中所列成品内径尺寸为新轮箍尺寸,检修轮箍尺寸按旧轮心配。技术要求和检验方法
4.1轮箍钢坏
4.1.1要求
内径d
单位为毫米
单位为毫米
箍宽B
4.1.1.1轮箍钢应采用由电炉或转炉方法冶炼并经炉外精炼和真空脱气处理的连铸钢坏或模铸钢锭制造,模铸钢锭应从底部浇铸。4.1.1.2采用模铸钢锭制造轮箍时钢锭应切头处理,切头量应足以消除钢锭两端影响轮箍质量的有害部分。钢锭所有表面不应有影响轧制质量的缺陷。轮箍钢代号和化学成分(熔炼分析)见表2。4.1.1.3
表2轮箍钢代号和化学成分(熔炼分析)化学成分(质量分数)
0.57~0.65
0.20~0.42
0.60~0.90
表2轮箍钢代号和化学成分(熔炼分析)(续)化学成分(质量分数)
注1:轮箍钢水氢含量不应超过2×10Mo
注2:当钢中的C含量大于0.62%时,Mn的含量不应超过0.80%。4.1.2试验方法
TB/T1400.2—2018
Cr+Mo+Ni
4.1.2.1轮箍钢熔炼分析每炉应至少取一个试样,取样按GB/T20066的方法进行,试验按GB/T4336或GB/T223规定的方法进行。4.1.2.2钢水氢含量检测应按附录A规定的任一方法进行。4.2轮箍制造
4.2.1要求
4.2.1.1轮箍应经整体锻造和轧制成型,在热成形加热时,应防止轮箍钢坏过热、过烧。4.2.1.2
轮箍应进行淬火和回火处理。
3轮箍的成品化学成分分析与熔炼要求限值充许偏差见表3。4.2.1.3
表3成品化学成分允许偏差
化学成分允许偏差(质量分数)%
注:成品化学成分与表2规定的成分界限值的偏差。4.2.2成品化学分析取样位置及试验方法Cr
成品化学分析应在轮箍标称直径处(ΦD)的踏面下20mm处取不少于50g的钢屑试样,其分析方法按GB/T223的规定进行。当采用光谱分析时,可使用拉伸试样端部,试验按GB/T4336规定的方法进行。轮箍的成品化学分析也可按GB/T20123、GB/T20125规定的方法进行。当出现异议时,按GB/T223规定的方法进行仲裁。
4.3力学性能
4.3.1拉伸性能
4.3.1.1要求
轮箍拉伸性能应符合表4的规定。表4轮箍拉伸性能
取样位置
抗拉强度R.
950~1130
试样取样其位置如图2所示。
断后伸长率A.0m
断面收缩率Z
TB/T1400.2—2018
金属拉伸试样
4.3.1.3试验方法
图2拉伸试样位置
试验应按GB/T228.1规定的方法进行。轮箍拉伸试样平行长度内直径为15mm,原始标距为其直径的4倍。4.3.2冲击性能
4.3.2.1要求
单位为毫米
轮箍冲击性能应符合表5的规定。冲击试验均采用U形缺口试样,缺口深度2mm。以3个试样试验结果的算术平均值确定。
表5冲击性能
吸收能量KU,
三个试样平均值
推荐只充许1个单值低于平均值。4.3.2.2
取样位置
单值“
冲击性能取样位置见图3。试样应沿着轧制方向切取。R
20℃种击试样
三个试样平均值
-60℃冲击试样
图3冲击试验取样位置
单位为焦耳
单位为毫米
4.3.2.3试验方法
试验应按GB/T229规定的方法进行。4.3.3轮箍硬度
4.3.3.1要求
轮箍硬度应符合表6的规定。
表6轮箍布氏硬度
断面硬度
HBW10/3000
踏面下20mm
处硬度
≥269
轮缘中
部硬度
≤321
踏面(ΦD)下20mm的硬度按3个测点的算术平均值来确定。4.3.3.2试验位置
轮箍断面硬度试验位置见图4。
轮箍表
面硬度
277~341
TB/T1400.22018
表面硬度
HBW10/3000
同一炉号同一热处理批次的
轮箍表面硬度最大差值
粗制轮箍表面硬度测点应与打印标志错开,该位置须经研磨准备,以去除材料的脱碳层。测点处打磨深度不应大于1mm,并不应影响轮箍精加工尺寸。在机械加工后进行表面硬度试验时,布氏硬度压痕可以留在交货轮箍表面。测量轮箍表面硬度的压痕应位于轮箍外侧面上,压痕位置应选在半径比轮箍孔半径大30mm的圆周上。单位为毫米
4.3.3.3试验方法
图4轮箍硬度试验位置
试验应按GB/T231.1规定的方法进行。压头直径应采用10mm。4.4落锤
4.4.1.1要求
轮箍应做落锤试验,落锤试验后,轮箍不应有裂纹、断裂或其他破损现象。4.4.1.2试验方法
试样为交货状态的轮箍,轮箍需垂直放置,以1t重锤冲击轮箍,锤头冲击面应是半径为150mm的圆柱面,底座重量不应小于12t,轮箍受锤击后,所产生的挠度值(以相对于内径百分率表示),不应小于按公式(1)计算值。
TB/T1400.2—2018
式中:
一落锤试验产生的挠度值:
f≥0.60x-
一轮箍外径的数值,单位为毫米(mm);一表4中规定的抗拉强度要求的下限的数值,单位为兆帕(MPa)。重锤的最低落下高度与其冲击功Q(mgh)有关,应按公式(2)计算出来的数值来确定。h≥15q/mg
式中:
一重锤落下高度的数值,单位为米(m);h
轮箍的实际质量的数值,单位为千克(kg);m
重锤的实际质量的数值,单位为千克(kg);一重力加速度的数值,取近似数值为9.8,单位为米每平方秒(m/s2)。g
达到要求的挠度时所需锤击次数需载人记录,落锤试验时的轮箍温度不高于50℃。4.5显微组织、晶粒度和非金属夹杂物4.5.1要求
(2)
轮箍经淬火和回火处理后其显微组织应为细珠光体,可存在铁素体,不应存在影响轮箍性能的上贝氏体,马氏体等其他有害组织。晶粒度不应低于6级。
轮箍非金属夹杂物级别应符合表7的规定。非金属夹杂物级别要求
4.5.2取样位置
A(硫化物类)
B(氧化铝类)
C(硅酸盐类)
D(球状氧化物类)
显微组织、晶粒度和非金属夹杂物的取样位置见图5,试样检验面平行于轮箍的外侧面,每个试样的检验面面积不小于200mm,显微组织和晶粒度检验用图5的1号试样进行,非金属夹杂物检验用图5的1、2、3号试样进行。
图5显微组织、晶粒度和非金属夹杂物检验的取样位置6
单位为毫米
4.5.3试验方法
按GB/T13298规定的方法进行显微组织检验。按GB/T6394规定的方法进行晶粒度检验。按GB/T10561一2005规定的A方法进行非金属夹杂物检验。4.6低倍组织
4.6.1要求
TB/T1400.2—2018
轮箍低倍试片上不应有白点、缩孔残余、分层、裂纹、翻皮、异型偏析和金属异物,一般疏松、中心疏松应小于或等于2级,偏析和非金属夹杂物应小于或等于1级。4.6.2试验位置
轮箍低倍检验试样为轮箍整个截面。4.6.3试验方法
轮箍低倍组织检验按GB/T226规定的热酸浸方法执行,按附录B的图谱进行评定。4.7内部完好性
4.7.1一般要求
轮箍内部完好性应通过超声波检测确定。应对每一个轮箍进行超声波检测。超声波检测应在最终热处理之后进行。4.7.2验收标准
轮箍超声波检测应符合:
a)不应存在大于或等于Φ2mm平底孔当量的内部缺陷。b)不应存在条状缺陷(长宽比大于3缺陷)。c)轴向探伤,检测踏面以下10mm区域时,由缺陷引起的底面回波幅度衰减应小于4dB。4.7.3检测方法
按附录C规定的方法进行检验。
4.8表面状态和表面质量
4.8.1要求
轮箍表面不应有飞边、毛刺、结疤、折叠、裂纹、压人物和缺肉等缺陷。若有上述缺陷,应沿轮箍的圆周方向凿铲和车削,修整痕迹应平缓过渡,满足成品尺寸公差要求。轮箍踏面、轮缘面、内径面和轮心挡表面的清理深度不应超过机加工余量的80%。轮箍内、外侧面上为精加工尺寸时,不应有残留的径向和大于30°的斜向清理痕迹、切向清理痕迹,外侧面不应大于5mm,内侧面不应大于3mm。同一个轮箍内、外侧面凿铲长度不应超过500mm,在一个横截面上不应多于两条铲痕,任何一条铲痕不应达到侧面的边缘。
轮箍表面不应用铸、焊、喷涂、电或化学沉积等工艺进行修整。4.8.2检验方法
粗制轮箍表面质量可用目视检验,成品轮箍表面应采用湿法或干法磁粉探伤,探伤方法见附录D。
经加工后的轮箍表面粗糙度及表面质量的检验方法及所用检测器具应由供需双方认可。5检验规则
5.1组批
轮箍应按批检验。在周期式热处理炉中生产时,每批由同一轮型、同一炉号、同一热处理制度的轮箍组成。在贯通式连续炉中热处理时,可将不同炉号的轮箍按C+1/4Mn当量差不大于0.04%,且同一尺寸的轮箍组批,但每批轮箍个数不应大于200个。7
TB/T1400.2—2018
检验项目及数量
按表8所列项目进行检验,其结果应符合本部分规定表8检验项目及数量
检验类型
试验和检验项目
外形尺寸
熔炼分析(包括钢水氢含量)
成品分析
常温冲击(20℃)
低温冲击(-60℃)
踏面下20mm处硬度
轮缘中部硬度
轮辋表面硬度
同一炉号同一热处理批次的
轮箍轮辋表面硬度最大差值
显微组织和晶粒度
非金属夹杂物
低倍组织
落锤检验
内部完好性
表面质量
检验状态
试验单元
d——试验应在规定的热处理之后进行:同一熔炼炉号的轮箍:
h一同一热处理状态的轮箍:
x——出厂检验项目:
型式检验条件
W——以一个轮箍为一个试验单元:y——型式检验项目。
出厂检验每批抽样数
每包钢水
每包钢水
每10个熔炼炉号取1个
发生下列情况之一时应进行型式检验,检验内容为表8中的全部检验项目:a)
6标志
新产品定型时;
制造工艺、结构、材质等发生重大变化时;同类型所有产品停产2年以上再恢复生产时;连续生产5年时;
生产场地发生变更时。
6.1标志内容
轮箍制造标志内容应包括:
a)轧制月份;
b)轧制年份末两位数;
制造单位标记:
轮箍钢代号:2;
e)熔炼炉号;
f)轮箍顺序号。
TB/T1400.2-2018
6.2标志排列顺序见图6,不应改变标志顺序。无标志或标记不清无法辨认的,不应交货。6.3标志基线至轮箍挡内圈的距离为20mm~30mm,字体高为10mm~15mm,在外侧面加工到成品位置及光洁的粗制轮箍上采用冷打印标志,字迹应清晰可辨,字形、笔画根部不应出现尖角。出厂后冷打印标志轮箍的外侧面不再进行加工。说明:
轧制月份;2——轧制年份末两位数;3—制造单位标记:
一轮箍钢代号;5一
一轮箍顺序号。
熔炼炉号:6
图6轮箍制造标志
7包装及防护
轮箍应采用专用集装箱或用户(买方)与制造单位商定的包装方式运输,运输和存放过程中应防止腐蚀和机械损伤。
8质量证明书
制造单位应对每批轮箍开具质量证明书。8.1
质量证明书应包括以下内容:
制造单位名称;
轮箍规格和型号;
轮箍钢代号;
d)轮箍数目;
熔炼炉号;
轮箍顺序号;
本部分规定的各项检验结果;
出厂日期。
小提示:此标准内容仅展示完整标准里的部分截取内容,若需要完整标准请到上方自行免费下载完整标准文档。

标准图片预览:
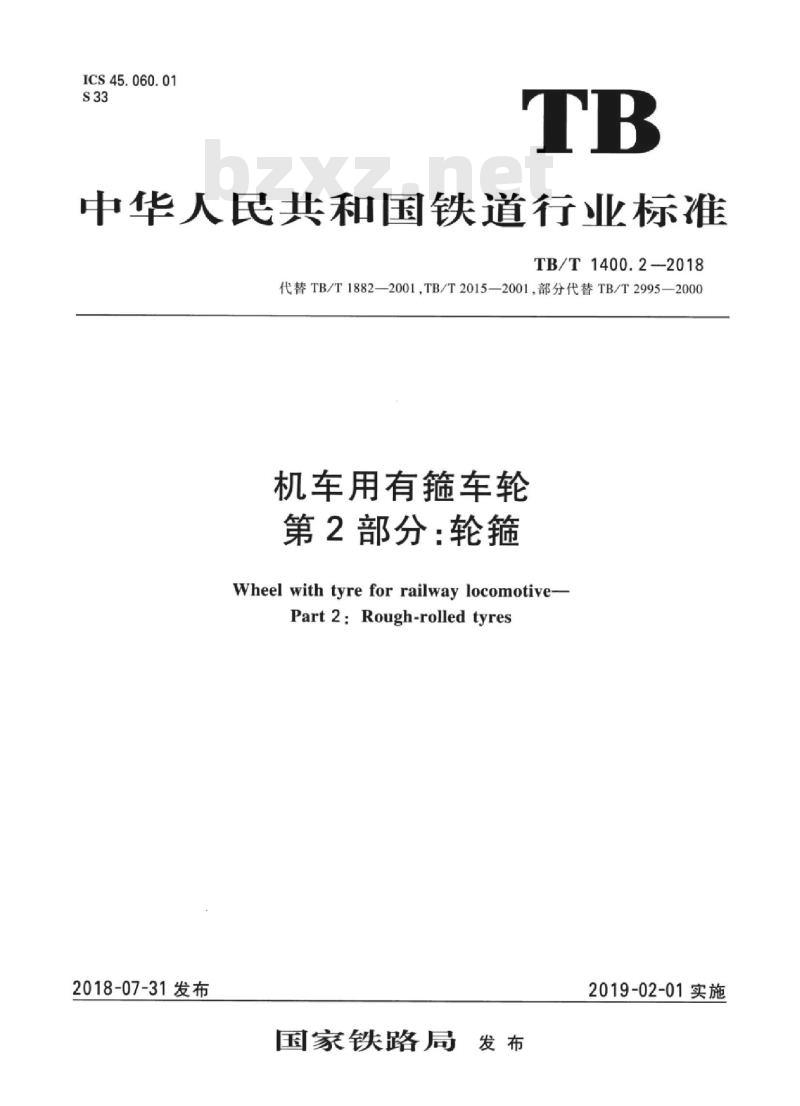
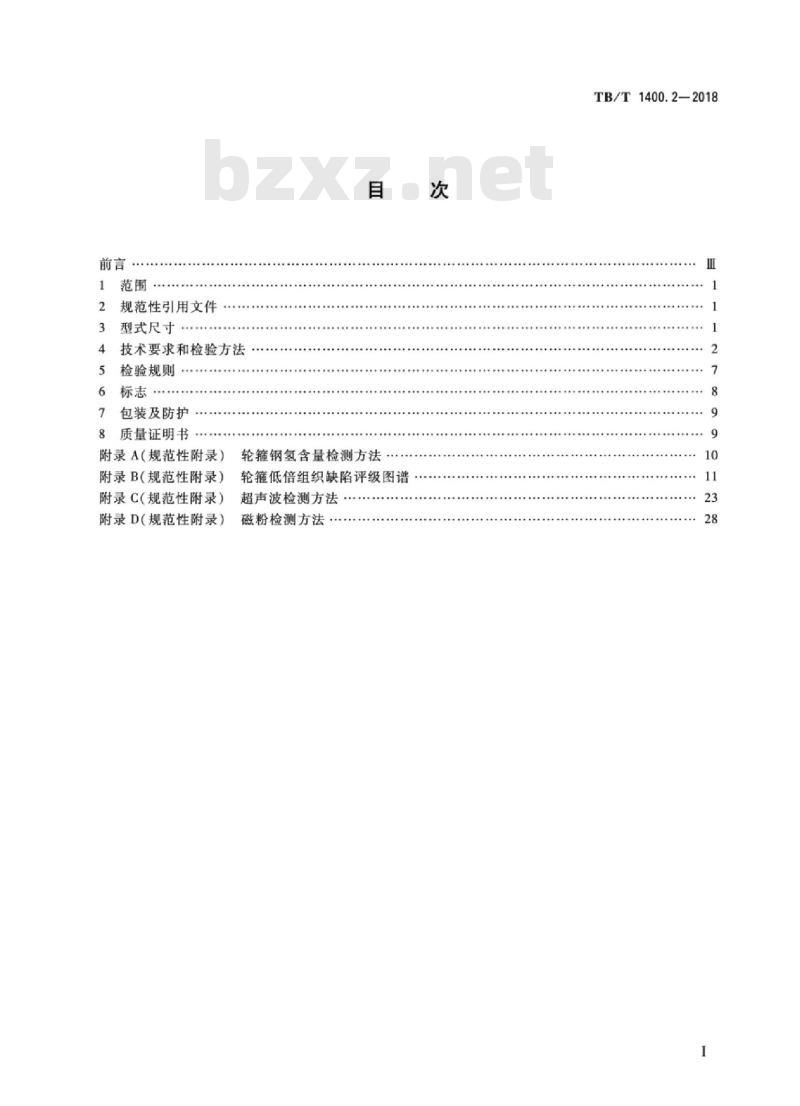
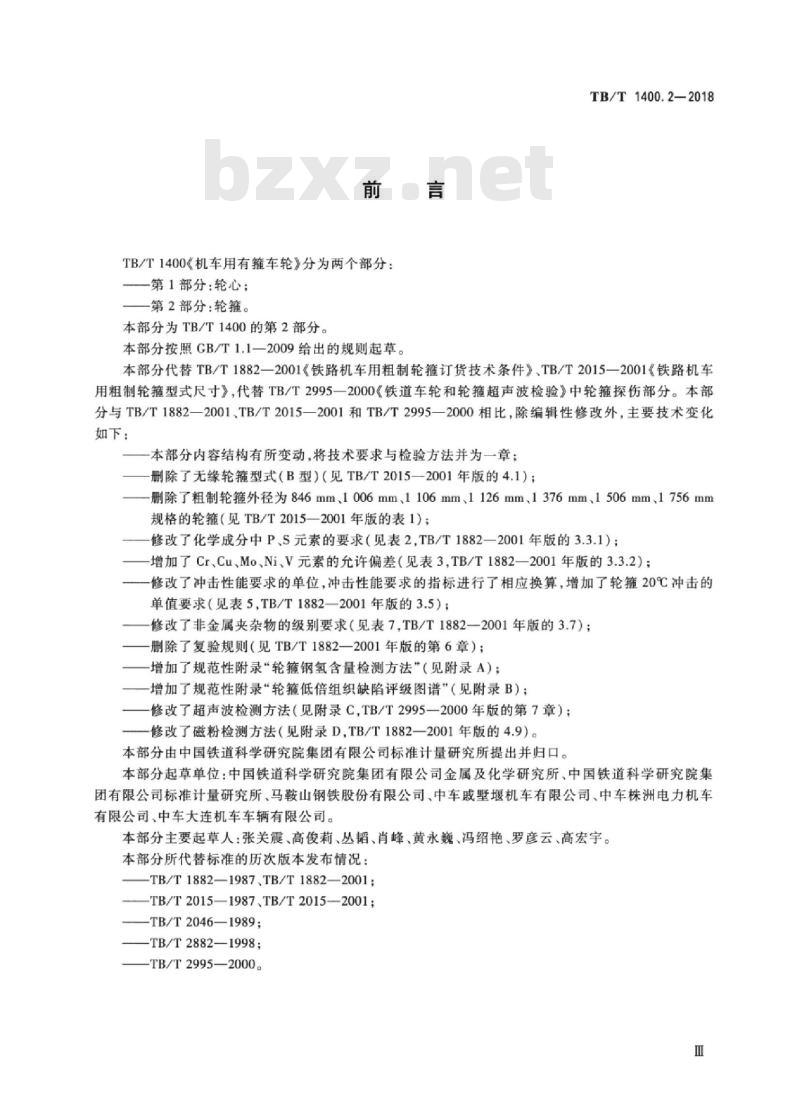
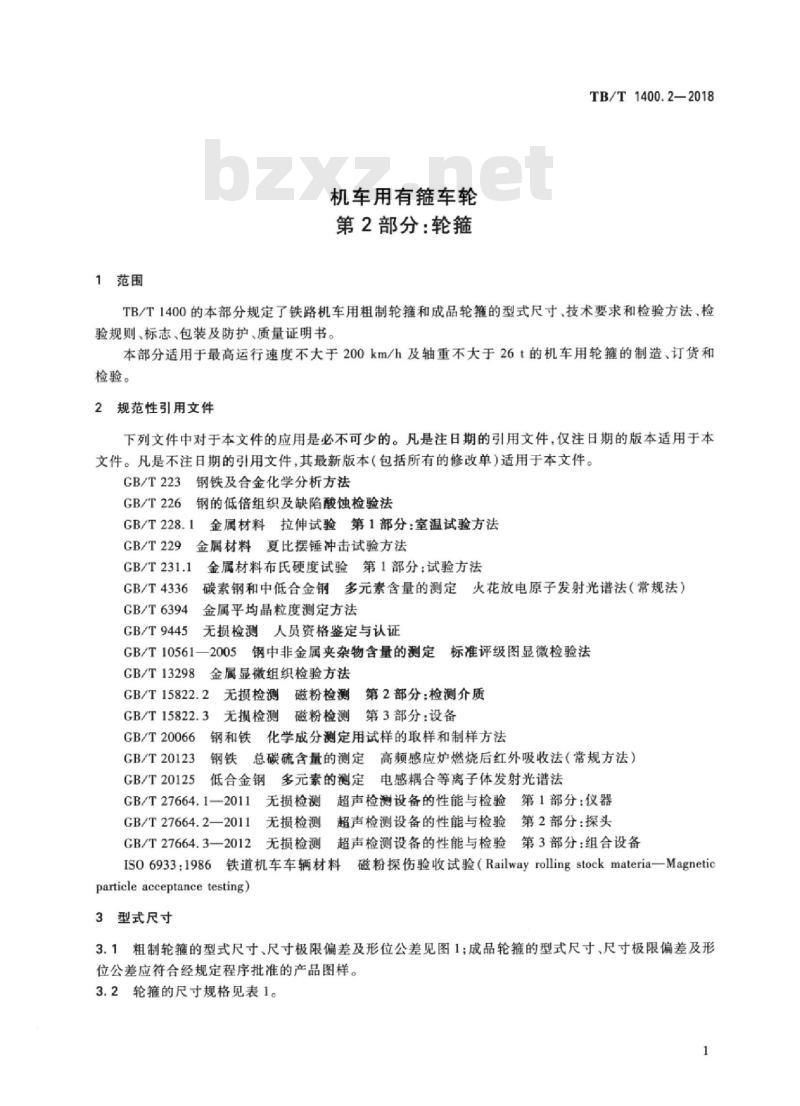
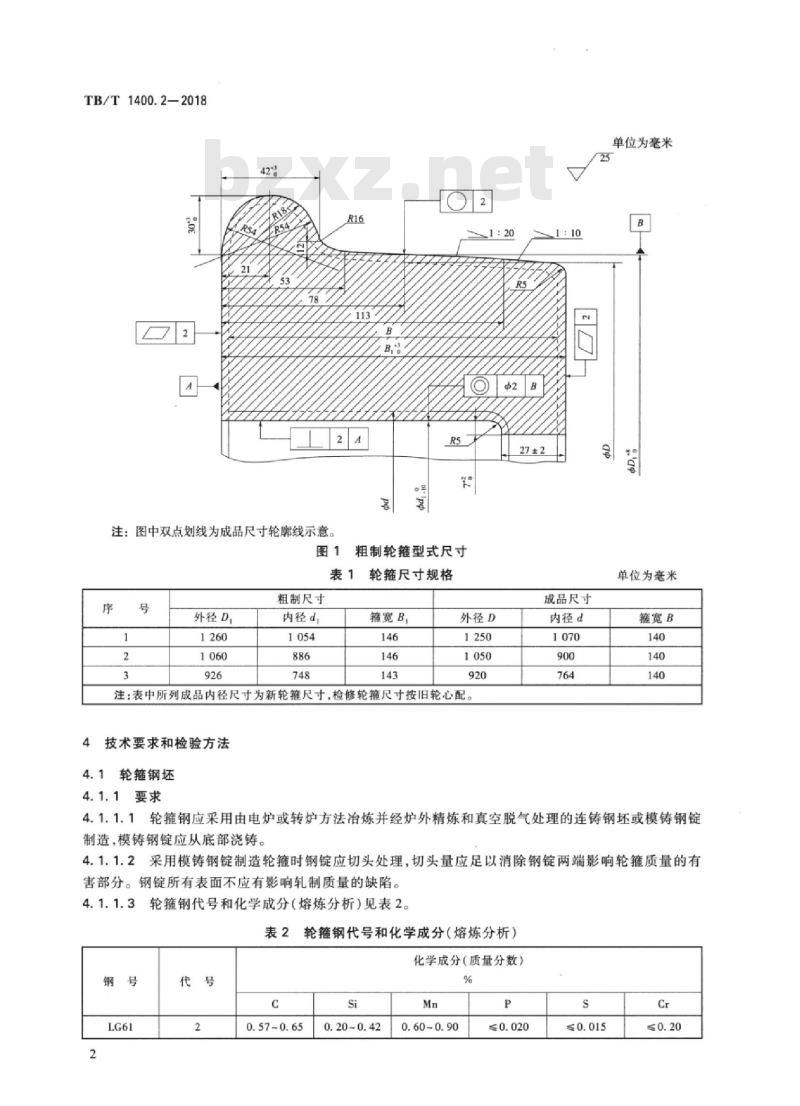
- 热门标准
- TB铁路运输标准
- TB/T3089-2004 铁路沿线斜坡柔性安全防护网
- TB/T2656-2005 铁路中间站光电数字引入柜技术要求和试验方法
- TB/T1632.1-2005 钢轨焊接 第1部分:通用技术条件
- TB/T2345-2008 43kg/m~75kg/m钢轨接头夹板订货技术条件
- TB10427-2011 铁路旅客车站客运服务信息系统工程施工质量验收标准
- TB10424-2018 铁路混凝土工程施工质量验收标准
- TB/T3199.2-2018 电气化铁路接触网用绝缘子第2部分:棒形复合绝缘子
- TB/T2152.27-1990 铁路工人技术标准 机务 接触网工
- TB10415-2018 铁路桥涵工程施工质量验收标准
- TB/T2685.1-1995 铁路环境监测质量控制环境监测指标体系及体系表
- TB/T1670.4-1985 15号车钩钩体上牵引台样板
- TB/T2152.28-1990 铁路工人技术标准 机务 继电保护工
- TB/T2152.29-1990 铁路工人技术标准 机务 高压试验工
- TB/T3353-2014 铁路隧道钢筋混凝土管片
- TB/T2152.33-1990 铁路工人技术标准 机务 给水化验工
- 行业新闻
网站备案号:湘ICP备2023016450号-1