- 您的位置:
- 标准下载网 >>
- 标准分类 >>
- 铁路运输行业标准(TB) >>
- TB/T 3285-2019 动车组抗侧滚扭杆
标准号:
TB/T 3285-2019
标准名称:
动车组抗侧滚扭杆
标准类别:
铁路运输行业标准(TB)
标准状态:
现行出版语种:
简体中文下载格式:
.zip .pdf下载大小:
4.33 MB
相关标签:
动车组

点击下载
标准简介:
标准号:TB/T 3285-2019
标准名称:动车组抗侧滚扭杆
英文名称:Anti-rolling torsion bar for EMU/DMU
标准格式:PDF
发布时间:2019-03-25
实施时间:2019-10-01
标准大小:4.42M
标准介绍:1范围
本标准规定了动车组抗侧滚扭杆的术语和定义,技术要求,检验方法,检验规则,标志、包装、运输和储存。
本标准适用于最高运行速度为200km/h及以上的动车组用抗侧滚扭杆。最高运行速度为00km/h以下的动车组用抗侧滚扭杆可参照执行。
2规范性引用文件
下列文件对本文件的应用是必不可少的。凡是注日期的引用文件,仅注日期的版本适用于本文件。凡是不注日期的引用文件,其最新版本(包括所有的修改单)适用于本文件。
GB/T224-2008钢的脱碳层深度测定法(IS03887:2003,MOD)
GB/T225-2006钢淬透性的末端淬火试验方法( Jominy试验)(Io642:1999,IDT)
GB/T228.1-2010金属材料拉伸试验第1部分:室温试验方法
GB/T229—2007金属材料夏比摆锤冲击试验方法(ISO148-1:2006,MOD
GB/T230.1金属材料洛氏硬度试验第1部分:试验方法(Is06508-1:2016,MOD)
GB/T1222-2016弹簧钢
GB/T4162-2008锻轧钢棒超声检测方法
GB/T4336-2016碳素钢和中低合金钢多元素含量的测定火花放电原子发射光谱法(常规GB/T6394-2017金属平均晶粒度测定方法
GB/T7704-2017无损检测X射线应力测定方法
本标准按照GB/T1.1-2009给出的规则起草
本标准代替TBT3285-2011《动车组抗侧滚扭杆》。与TB丌3285-2011相比,除编辑性修改外,本标准主要技术变化如下
修改了材料化学成分和力学性能要求(见4.2.1,2011年版的4.2.1);修改了材料淬透性应满足的标准(见4.2.4,2011年版的4.2.6)修改了扭杄的力学性能要求和直扭杆热处理后硬度,增加弯扭杆热处理后硬度(见4.2.8,2011年版的4.2.8)
修改了磁粉探伤要求(见4.2.9,2011年版的4.2.9)
修改了油漆漆膜附着力检验标准版本(见4.2.12、5.9,2011年版的4.2.12、5.9);
修改了强度要求和强度试验要求(见4.3.3、5.14,2011年版的4.3.3、5.13);
修改了原材料检验和组织检验项点(见5.1、5.2,2011年版的51);修改了化学成分检验执行标准(见5.1.1,2011年版的5.1.1);增加了冲击试验温度公差要求(见5.6,2011年版的5.5);修改了表面质量检验(见5.8,2011年版的5.7);
修改了表面喷丸的检验标准和表面残余应力检验执行标准(见5.9,2011年版的5.8);
修改了同一原材料批的说明(见6.1.2,2011年版的6.1.2);修改了进行型式检验的条件(见6.2.1,2011年版的6.2.1);修改了扭杆试样取样位置(见附录A中图A.2,2011年版的附录A中图A.2)。
本标准由中车青岛四方车辆研究所有限公司归口。
本标准起草单位:中车青岛四方机车车辆股份有限公司、株洲时代新材料科技股份有限公司、同济大学、中国铁道科学研究院集团有限公司标准计量研究所、中车长春轨道客车股份有限公司、中车唐山机车车辆有限公司、中车青岛四方车辆研究所有限公司。

部分标准内容:
iiKAacJouaKAa
中华人民共和国铁道行业标准
TB/T3285-2019
代替TB/T3285—2011
动车组抗侧滚扭杆
Anti-rolling torsion bar for EMU/DMU2019-03-25发布
国家铁路局
2019-10-01实施
规范性引用文件
术语和定义
技术要求
检验方法
检验规则
iiikAa~cJouakAa-
标志、包装、运输和储存
附录A(规范性附录)
扭杆试样取样位置
TB/T3285-2019
TB/T3285-2019
iiiKAacJouaKAa
本标准按照CB/T1.1—2009给出的规则起草。本标准代替TB/T3285-—2011《动车组抗侧滚扭杆》。与TB/T3285—2011相比,除编辑性修改外,本标准主要技术变化如下:
一修改了材料化学成分和力学性能要求(见4.2.1,2011年版的4.2.1);修改了材料淬透性应满足的标准(见4.2.4,2011年版的4.2.6);一修改了扭杆的力学性能要求和直扭杆热处理后硬度,增加弯扭杆热处理后硬度(见4.2.8,2011年版的4.2.8);
修改了磁粉探伤要求(见4.2.9,2011年版的4.2.9);修改了油漆漆膜附着力检验标准版本(见4.2.12、5.9,2011年版的4.2.12、5.9);修改了强度要求和强度试验要求(见4.3.3、5.14,2011年版的4.3.3,5.13);修改了原材料检验和组织检验项点(见5.1、5.2,2011年版的5.1);-修改了化学成分检验执行标准(见5.1.1,2011年版的5.1.1);增加了冲击试验温度公差要求(见5.6,2011年版的5.5);修改了表面质量检验(见5.8,2011年版的5.7);修改了表面喷丸的检验标准和表面残余应力检验执行标准(见5.9,2011年版的5.8);修改了同一原材料批的说明(见6.1.2,2011年版的6.1.2);一修改了进行型式检验的条件(见6.2.1,2011年版的6.2.1);修改了扭杆试样取样位置(见附录A中图A.2,2011年版的附录A中图A.2)。本标准由中车青岛四方车辆研究所有限公司归口。本标准起草单位:中车青岛四方机车车辆股份有限公司、株洲时代新材料科技股份有限公司、同济大学、中国铁道科学研究院集团有限公司标准计量研究所、中车长春轨道客车股份有限公司、中车唐山机车车辆有限公司、中车青岛四方车辆研究所有限公司。本标准主要起草人:崔志国、公衍军、姜云玲、刘文松、姜卫星、董博、吕成吉、陈经纬、李培行庞伟婿。
本标准所代替标准的历次发布情况:TB/T3285一2011。I
1范围
iiiKAa~cJouakAa-
动车组抗侧滚扭杆
TB/T3285—2019
本标准规定了动车组抗侧滚扭杆的术语和定义,技术要求,检验方法,检验规则,标志、包装、运输和储存。
本标准适用于最高运行速度为200km/h及以上的动车组用抗侧滚扭杆。最高运行速度为200km/h以下的动车组用抗侧滚扭杆可参照执行。2规范性引用文件
下列文件对本文件的应用是必不可少的。凡是注日期的引用文件,仅注日期的版本适用于本文件。凡是不注日期的引用文件,其最新版本(包括所有的修改单)适用于本文件。CB/T224—2008钢的脱碳层深度测定法(IS03887:2003,MOD)GB/T225一2006钢,率透性的末端率火试验方法(Jominy试验)(IS0642:1999,IDT)GB/T228.1—2010金属材料拉伸试验第1部分:室温试验方法GB/T229—2007金属材料夏比摆锤冲击试验方法(ISO148-1:2006,MOD)GB/T230.1金属材料洛氏硬度试验第1部分:试验方法(IS06508-1:2016,MOD)GB/T1222—2016弹簧钢
GB/T4162—2008
GB/T4336—2016
锻轧钢棒超声检测方法
碳素钢和中低合金钢多元素含量的测定火花放电原子发射光谱法(常规GB/T6394—2017
金属平均晶粒度测定方法
GB/T7704—2017无损检测X射线应力测定方法GB/T10561—2005
钢中非金属夹杂物含量的测定
标准评级图显微检验法(IS04967:1998,产品几何技术规范(GPS)表面结构轮廓法评定表面结构的规则和方GB/T10610-2009
法(ISO4288:1996IDT)
GB/T15822(所有部分)无损检测磁粉检测JB/T10174—2008钢铁零件强化喷丸的质量检验方法IS02409:2013色漆和清漆划格试验(Paintsandvarnishes—Cross-cuttest)3术语和定义
下列术语和定义适用于本文件。3.1
抗侧滚扭杆装置anti-rollingtorsionbarequipment对车辆的侧滚特性有影响的悬挂装置。注:抗侧滚扭杆装置一般包括抗侧滚扭杆和其他部件(如扭臂、连杆组成等)。1
TB/T3285-2019
iiiKAa~cJouakAa-
anti-rolling torsion bar
抗侧滚扭杆
在车体侧滚过程中主要承受扭转载荷,辅助一二系簧平衡稳定车体绕纵向轴线侧滚的部件。注:抗侧滚扭杆为抗侧滚扭杆装置的一部分,分为直扭杆和弯扭杆。3.3
直扭杆straighttorsionbar
抗侧滚扭杆装置中主要承受扭转载荷的直杆体。3.4
弯扭杆bendedtorsionbar
抗侧滚扭杆装置中主要承受扭转载荷的U形杆体。4技术要求
4.1一般要求
4.1.1扭杆应符合本标准及经规定程序批准的设计图样和技术文件的要求。4.1.2扭杆的使用寿命应与转向架的使用寿命相同。4.2材料及制造要求
4.2.1材料化学成分和力学性能
扭杆材料化学成分和力学性能应符合供需双方协商一致的规定,如无特殊要求,宜符合GB/T1222—2016的规定。
4.2.2内部质量
超声波探伤结果不应低于GB/T41622008中AA级的规定。4.2.3非金属夹杂物
扭杆棒料的非金属夹杂物等级应符合GB/T10561一2005的规定,具体见表1。如有其他要求,应在技术文件中明确。
表1非金属夹杂物要求
4.2.4淬透性
≤1.5级
≤1.0级
≤2.0级
≤1.0级
≤1.0级
≤0.5级
扭杆材料的率透性应符合CB/T12222016规定的HH等级要求。4.2.5奥氏体晶粒度
材料的奥氏体晶粒度等级不应低于GB/T6394—2017规定的7级要求。4.2.6扭杆端部镦粗
≤1.5级
≤0.5级
如无特殊规定,扭杆端部应采用锻粗工艺,端部粗时,应注意相关的工艺过程控制,以确保得到连续的纤维流线。
4.2.7脱碳层
脱碳层有以下两种形式:
a)全脱碳层:在扭杆的表层为纯铁素体微观组织;b)部分脱碳层:在扭杆的表层出现铁素体/珠光体或珠光体/马氏体的微观组织。2
iiiKAacJouaKAa
TB/T3285-—2019
不应存在全脱碳层;部分脱碳层的深度不应大于棒料直径的1%,任何情况下部分脱碳层最大深度不应大于0.5mm。
4.2.8扭杆的力学性能
除非另有规定,扭杆的力学性能应符合GB/T1222一—2016的规定,直扭杆热处理后表面硬度应达到47HRC~52HRC弯扭杆热处理后硬度应达到45HRC~50HRC。产品热处理后不应校正,产品表面不应通过焊补、电镀等方式进行修补处理。4.2.9磁粉探伤
扭杆在精加工后,应通过磁粉探伤检测其表面缺陷,不应存在表面裂纹。4.2.10表面质量
扭杆的尺寸、空间形状、形位公差与喷丸前的粗精度等应符合按规定程序批准的设计图样和技术文件要求。扭杆不应存在任何表面缺陷(如夹杂、缺口、工装印、裂纹等)。4.2.11喷丸处理
通过喷丸工艺在扭杆表面产生的残余应力层可以有效地提高其疲劳寿命,图1为典型表面残余应力的分布。
图1有效喷丸残余应力的分布
通过喷丸工艺产生表面残余应力的区域应当是在其使用过程当中主要的受力区域(如扭杆的中间部位,齿面配合区域等)。
在没有特殊要求的情况下,扭杆的其他区域也可进行喷丸,但不应影响扭杆的其他性能要求。喷丸时不应使用带有锐边的钢丸,扭杆表面喷丸区域的覆盖率不应小于95%,喷丸处理强度应为40AlmenA(拱高0.4mm)到60AlmenA(拱高0.6mm),表面残余应力值应满足以下要求:a)当=0.1mm时,o,≤-500MPa;b)当=0.3mm时,0,≤-100MPa。4.2.12防腐蚀保护
扭杆应进行防腐蚀保护,采用油漆涂装时,漆膜的厚度、颜色、附着力等应符合技术文件的规定,漆膜的网格试验应达到IS02409:2013规定的1级要求。4.2.13重量
扭杆的重量应符合供需双方协商确定的技术文件的要求。4.3性能要求
4.3.1刚度
扭杆装置的抗侧滚刚度应符合产品图样或技术条件的要求。扭杆的抗侧滚刚度值由扭矩和相应的角度偏转来定义,图2及公式(1)表示扭杆刚度的计算方法。3
TB/T3285-—2019
式中:
iiKAa~cJouaKAa-
图2扭杆的刚度计算
R,—扭转刚度,单位为牛米每弧度(N·m/rad);AM—扭矩差值,单位为牛米(N·m);Ag——偏转角度差值,单位为弧度(rad)。4.3.2弹性
扭杆在最大扭转角状态下不应发生永久变形。4.3.3强度
4.3.3.1静强度
扭杆应根据超常载荷工况进行静强度评估。4.3.3.2疲劳强度
扭杆应根据运营载荷工况通过疲劳试验进行疲劳强度评估。4.3.3.3载荷要求
除非另有规定,按以下要求执行:max
a)超常载荷对应于运用过程中车体相对构架最大侧滚角工况下的载荷;b)
疲劳载荷F,对应于侧滚系数α=0.1工况下的载荷。4.3.3.4强度评定
扭杆的强度应满足以下要求:
超常载荷工况测得的应力值不应超过扭杆材料的屈服极限;a)
在试验过程中扭杆和扭臂之间不应有任何形式的相对移动;试验前后扭臂高度差变化不应大于1mm;试验前后整体刚度变化率不应大于5%;在整个疲劳试验过程中,扭杆不应出现裂纹和断裂现象。(1)
5检验方法
5.1原材料检验
5.1,1化学成分检验
iiiKAacJouaKAa-
每炉钢都要进行化学成分的分析,检验按GB/T4336—2016的规定进行。5.1.2超声波探伤
原材料应进行超声波检查,检验按CGB/T4162—2008的规定进行。5.1.3非金属夹杂物检验
采用CB/T10561一2005规定的方法对圆钢中的非金属夹杂物进行显微评级。5.1.4透性
原材料的淬透性按CB/T2252006的规定进行验证。5.2组织检验
5.2.1奥氏体晶粒度检验
奥氏体晶粒度级别应按GB/T6394一2017的规定进行评级。5.2.2扭杆端部锻造纤维流线检验检验时应纵向切开扭杆锻造部位,通过使用剂和自视来检验纤维流线。5.3脱碳层检验
TB/T3285—2019
脱碳层检验在随炉等径试棒(长度大于扭杆中间直径的4倍且不小于200mm)上进行,试验方法采用GB/T224—2008规定的金相测试方法。5.4火和回火后硬度检验
表面硬度在热处理之后精加工之前进行测量。在图纸或技术文件规定的位置按GB/T230.1进行扭杆硬度检验。
5.5拉伸性能试验
材料的拉伸性能试样应在扭杆或随炉等径试棒(长度大于扭杆中间直径的4倍且不小于200mm)热处理后,喷丸前取样。试样的取样方式、尺寸和其他相关要求按CB/T228.1一2010的规定执行,扭杆取样位置及随炉等径试棒取样位置见附录A。5.6冲击性能试验
材料的冲击性能试样应在扭杆或随炉等径试棒(长度大于扭杆中间直径的4倍且不小于200mm)热处理后、喷丸前取样。试样的取样方式、尺寸和其他相关要求按CB/T229一2007执行,扭杆取样位置及随炉等径试棒取样位置见附录A。冲击试验按CB/T229—2007执行。在20℃±2℃时进行缺口深度为5mm的U形缺口全尺寸冲击试样(10mm×10mm×55mm)试验。5.7磁粉探伤检查
扭杆的磁粉探伤检查按CB/T15822(所有部分)的规定进行。探伤磁场强度应达到3.2kA/m,磁粉探伤后应对扭杆进行退磁处理,剩磁强度不大于0.4kA/m。5.8表面质量检验
在对扭杆喷丸处理之前应对其表面质量进行目视检查扭杆的尺寸、空间形状、形位公差与粗箱度等应满足设计图样和技术文件要求,粗糙度检验按GB/T10610一2009的规定进行。5.9喷丸检验
扭杆喷丸时按JB/T10174一2008的规定采用A试片检查喷丸处理覆盖率和喷丸处理强度。扭杆表面残余应力应根据CB/T7704—2017的要求通过X射线衍射来检验。5.10涂装检验
油漆漆膜附着力检验应根据IS02409:2013的规定进行。5
TB/T3285-2019
重量检查
iikAa~cJouakAa-
使用满足检测精度要求的设备对产品进行称重检查。5.12刚度试验
扭杆刚度的测试应按照如下方法进行:记录在施加每一个扭矩M时,扭杆的角度偏转6,或产生每一个扭杆偏转角度时,扭矩的大小。至少完整加载两个循环,加载频率不高于0.05Hz,一个循环为持续不间断的从零位置到最大位移(或从零载荷到最大载荷)的过程,记录第二个循序时的相关参数。5.13弹性试验
应在技术规范中明确扭杆的最大扭转角,并在试验时持续2min以上不发生永久变形,回复自由状态时其位置误差不应大于10°。5.14强度试验
5.14.1静强度试验
扭杆应根据超常载荷工况按照图3进行静强度试验。5.14.2疲劳试验
5.14.2.1只有在5.1~5.13和5.14.1试验完成并合格后,才能进行扭杆的疲劳试验。5.14.2.2图3给出了疲劳试验安装和加载示意图。+Fz
疲劳试验安装和加载示意
5.14.2.3除非另有规定,按照图4所示的疲劳试验载荷谱进行疲劳试验,加载次数为1×10°次。F2载荷
2×100
图4疲劳试验载荷谱
N循环次数
2×106
检验规则
出厂检验
iiKAacJouaKAa
TB/T3285—2019
6.1.1出厂检验项目见表2,其中超声波探伤、淬火和回火后硬度、磁粉探伤、表面质量为全检,其余为抽检。
抽检项目组批规则及抽样方案为:6.1.2
原材料化学成分、非金属夹杂物、淬透性检查的检验批为同一原材料批(同一炉且同一交货时间为同一原材料批),取样在原材料上进行,试样数量为1件。晶粒度、脱碳层、拉伸性能、冲击性能检查的检验批为同一热处理批。取样在随炉等径试棒上进行,冲击性能检查试样数量为3件,其余为1件。如在热处理后采用精加工工艺能完全去除脱碳层,则脱碳层检验仅为型式检验。喷丸检验的检验批为同一喷丸批,试样数量为1件。油漆检查的检验批为同一油漆批,试样数量为1件。表2
检验项目
化学成分
超声波探伤
非金属夹杂物
泽透性
奥氏体晶粒度
扭杆端部粗
脱碳层
率火和回火后硬度
拉伸性能
冲击性能
磁粉探伤
表面质量
型式检验
检验项目
出厂检验
技术要求对应条款
拉伸性能和冲击性能的型式检验在扭杆上取样,出厂检验可在随炉等径试上取样。喷丸检验在出厂检验时仅为A试片检查,残余应力仅作为型式试验。试验方法对应条款
6.1.3出厂抽检项目不合格时,可从原检验批中加倍抽样进行复验,复验仍有不合格时,则判定该批产品不合格。
6.1.4出厂检验合格的产品应有合格证,内容包括:a)
制造广代号;
TB/T3285-—2019
iiiKAacJouaKAa-
产品型号和编号;
出厂年月;
检查人员姓名或代号;
合格印章。
6.2型式检验
在下列情况之一时应进行型式检验:新产品定型或首次生产时;
产品结构、材料和工艺有较大改变,影响产品性能时;转场生产时;
产品停产2年及以上恢复生产时:连续生产满3年时。
型式检验项目见表2。
标志、包装、运输和储存
7.1每件产品应有清晰耐久的标志,标志的位置应在扭杆端部,内容至少包括:a)制造商的标识;
b)生产年月和可追溯的序列号。2扭杆用专用包装箱包装,包装箱内应衬垫减振材料。包装材料应符合有关环保要求。在包装的7.2
外表面至少应标明如下信息:
扭杆名称、型号和编号:
出厂日期;
制造商名称或代号;
产品批次及数量。
7.3在运输过程中,应防止挤压、磕碰和化学物品的侵蚀,码放整齐。扭杆应储存在干燥、通风、周围无腐蚀介质的库房内。7.4
iiikAacJouakAa
附录A
(规范性附录)
扭杆试样取样位置
TB/T32852019
本附录规定了扭杆的力学性能取样位置,所有的试样都应与产品来自同一热处理批次。扭杆本体用于检测力学性能的拉伸试样应取图A.1中区域“e\位置,拉伸试样的轴线应与扭杆的轴线平行,且其径向取样位置见图A.2。随炉等径试棒的径向取样位置见图A.2。用于检测冲击吸收能量的冲击试样应取图A.1中区域“”位置,冲击试样的径向取样位置见图A.3。
对于直径大于50mm的扭杆,冲击试样应取自圆形截面的1/2半径处,试样的纵向轴应与扭杆的轴平行。当棒料的直径较小时,冲击试样的边部距棒料表面不应低于2mm。e
a)直扭杆
b)弯扭杆
取样位置
图A.2拉伸试样的径向取样位置
小提示:此标准内容仅展示完整标准里的部分截取内容,若需要完整标准请到上方自行免费下载完整标准文档。

标准图片预览:
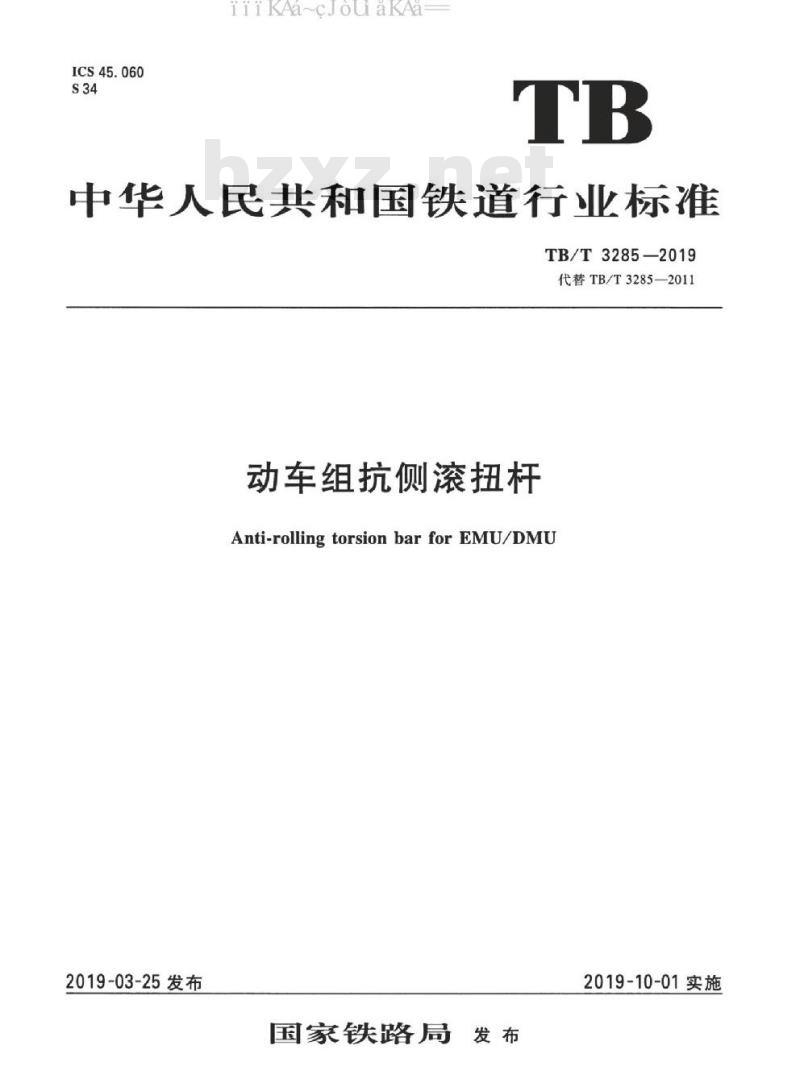
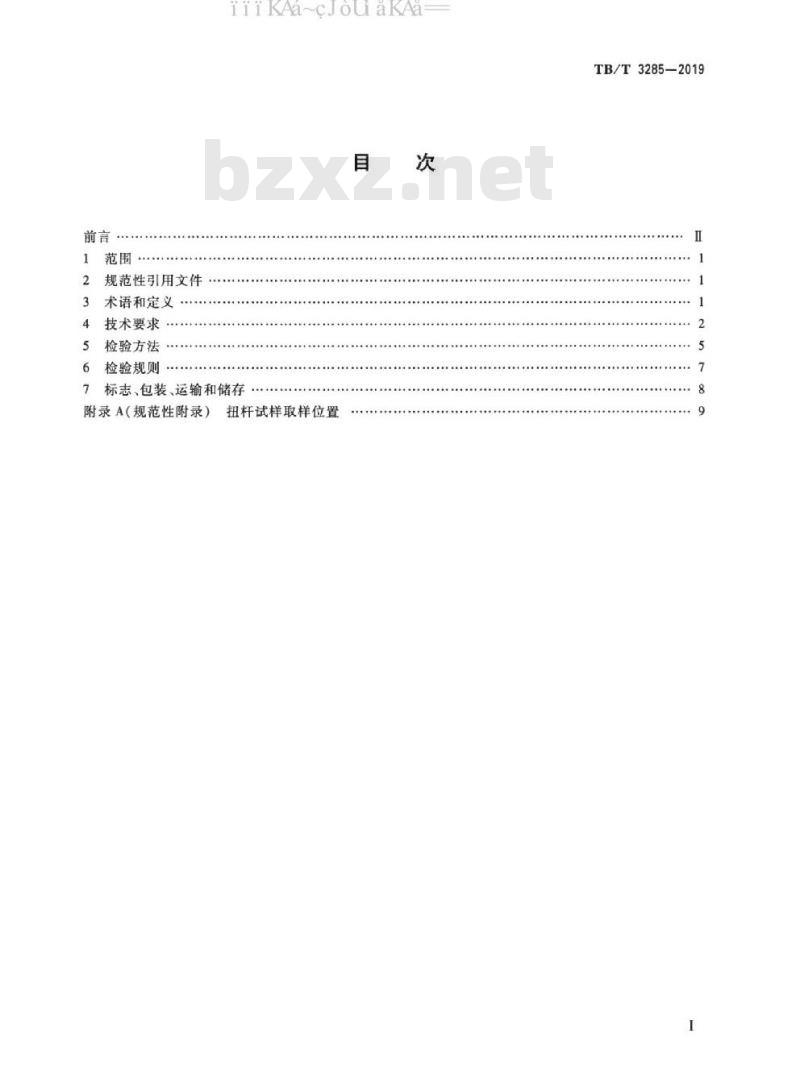
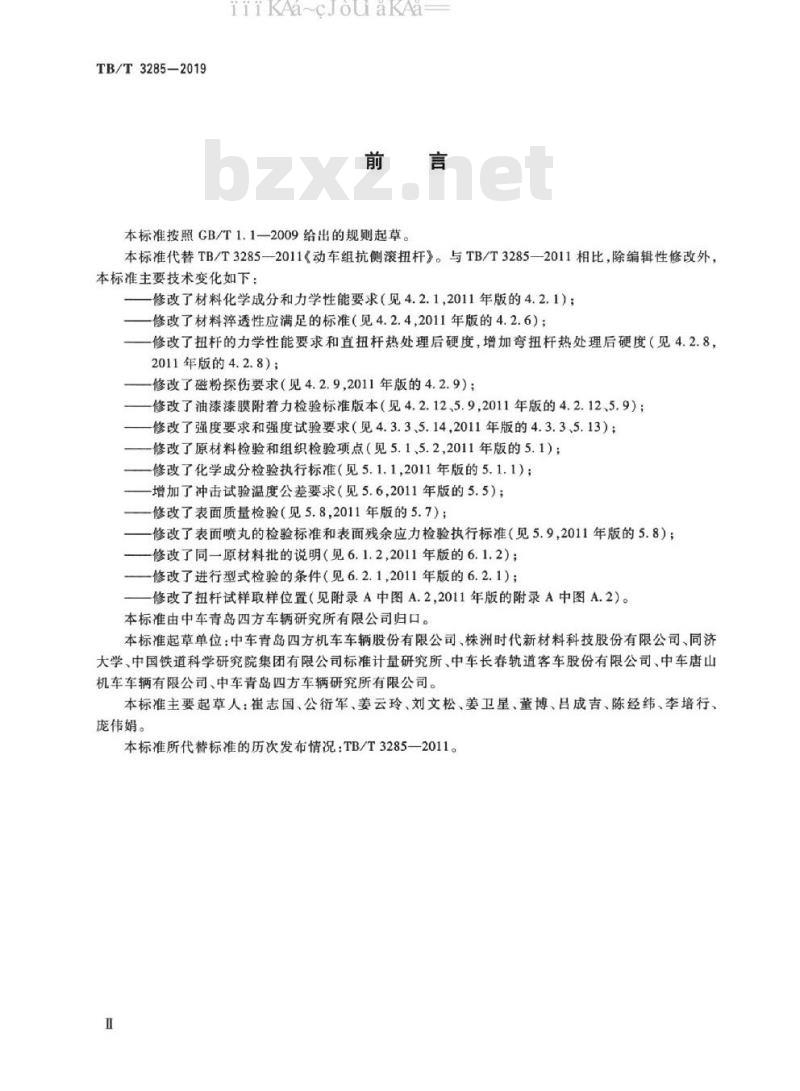
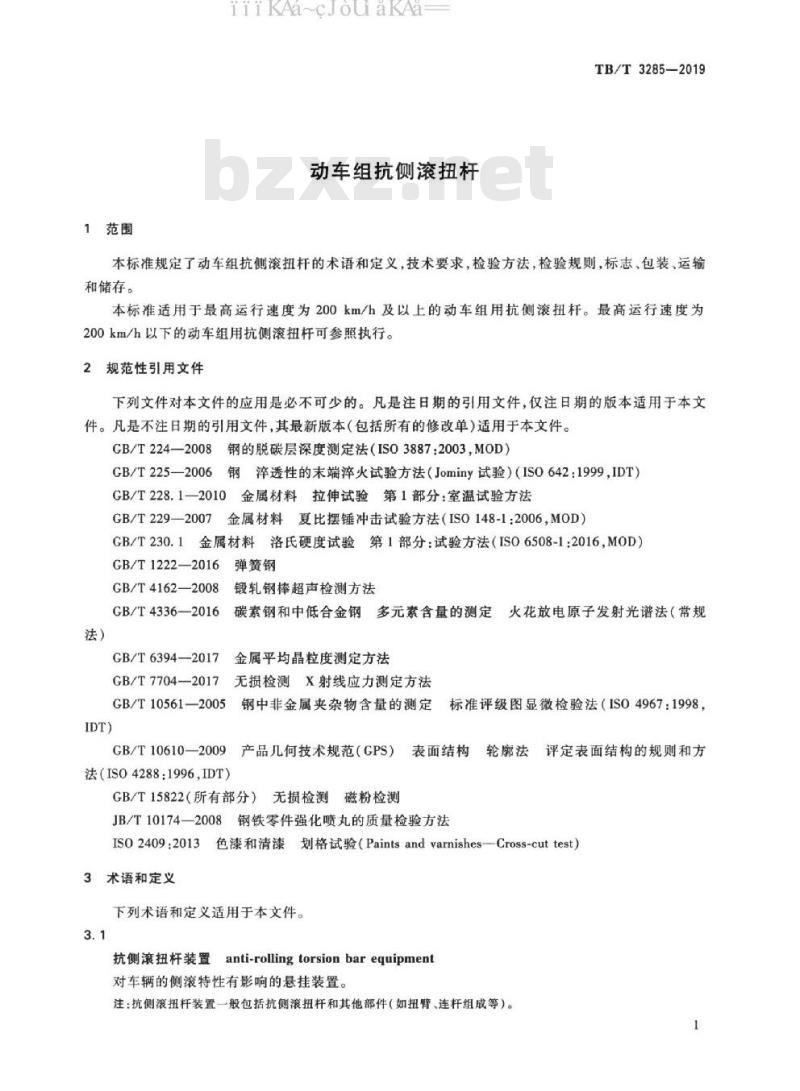
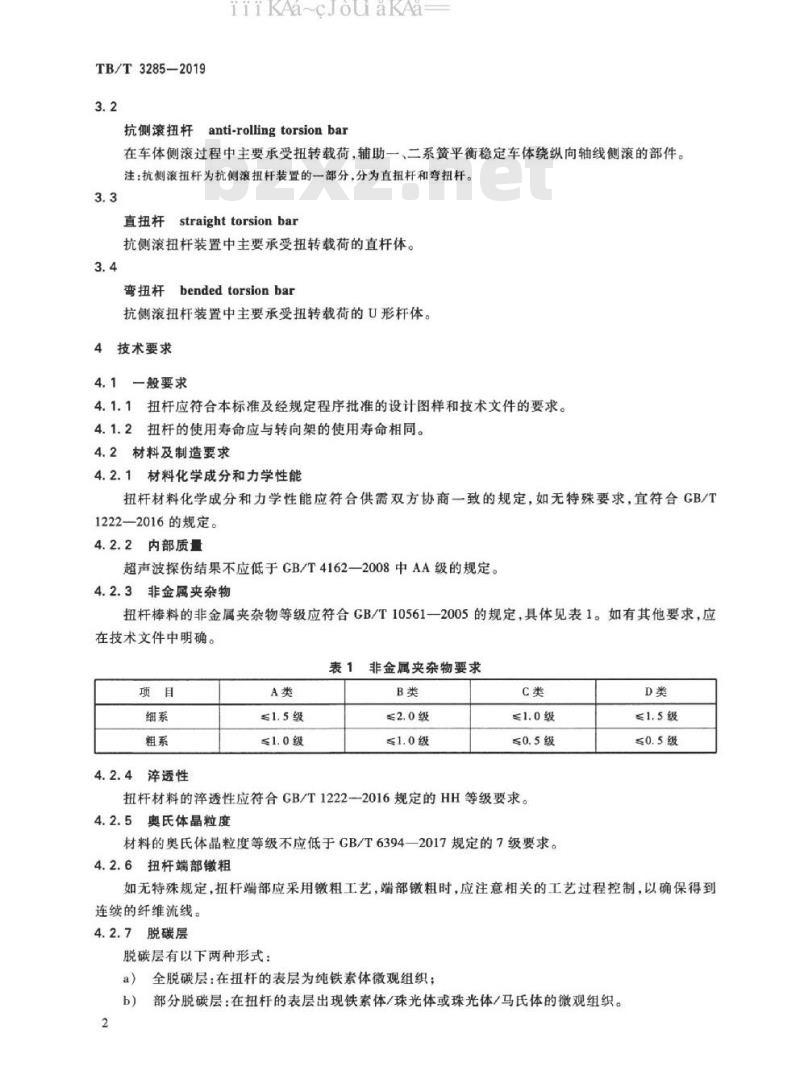
- 其它标准
- 热门标准
- TB铁路运输标准
- TB/T3043-2018 客货共线铁路预制后张法预应力混凝土简支梁
- TB/T3556-2020 铁路桥梁用结构钢
- TB/T2865-1997 铁路升降式投光灯塔技术条件
- TB/T3205.1-2016 扼流变压器钢轨引接线、中点连接线、中点连接板第1部分:钢轨引接线
- TB/T2486-94铁 钢梁涂膜劣化评定
- TB/T1466-91铁 机车车辆用灰铸铁件通用技术条件
- TB1670.10-1985 15号车钩钩体上下耳孔工作样板
- TB/T2073-2020 电气化铁路接触网零部件技术条件
- TB/T1528.1-2018 铁路信号电源系统设备第1部分:通用要求
- TB/T1500.5-2009 接发列车作业第5部分:单双线半自动闭塞色灯电锁器联锁
- TB/T2416-2010 内燃机车柴油机喷油泵试验台
- TB/T2509-2014 电力机车及电动车组牵引效率试验方法
- TB/T3087-2016 机车车辆总风软管连接器
- TB/T3393.2-2015 机车车辆高压互感器第2部分:电磁式电压互感器
- TB/T3259-2011 动车组用铝及铝合金焊接技术条件
- 行业新闻
网站备案号:湘ICP备2023016450号-1