- 您的位置:
- 标准下载网 >>
- 标准分类 >>
- 国家标准(GB) >>
- GB/T 519-2008 充气轮胎物理性能试验方法

【国家标准(GB)】 充气轮胎物理性能试验方法
本网站 发布时间:
2024-06-30 11:55:19
- GB/T519-2008
- 现行
标准号:
GB/T 519-2008
标准名称:
充气轮胎物理性能试验方法
标准类别:
国家标准(GB)
标准状态:
现行-
发布日期:
2008-06-18 -
实施日期:
2009-02-01 出版语种:
简体中文下载格式:
.rar.pdf下载大小:
585.65 KB
替代情况:
替代GB/T 519-2003

点击下载
标准简介:
标准下载解压密码:www.bzxz.net
本标准规定了充气轮胎(外胎、内胎和垫带)物理性能试验方法用术语和定义、试样制备、外胎物理性能试验、轮胎内衬层渗透分析测定方法、内胎物理性能试验、垫带物理性能试验。本标准适用于轿车轮胎、载重汽车轮胎、农业轮胎、工程机械轮胎和工业车辆充气轮胎。本标准不适用于航空轮胎、摩托车轮胎和力车轮胎。 本标准代替GB/T 519-2003《充气轮胎物理性能试验方法》。本标准与GB/T 519-2003的主要差异如下:——增加了子午线轮胎外胎特有部位胶料类型的相关试验内容;——增加了“建议优先选用以切削方式(采用切片机)直接制备标准厚度试样”;——增加了全钢子午线轮胎胎圈部位胎体钢帘线密度的测定;——增加了纤维子午线轮胎纤维冠带层帘线的相关取样及试验内容;——增加了子午线轮胎胎体层、带束层、钢帘线的取样及试验相关内容;——增加了子午线轮胎内衬气密胶层渗透性的分析观测试验内容。 GB/T 519-2008 充气轮胎物理性能试验方法 GB/T519-2008

部分标准内容:
ICS83.160.01
中华人民共和国国家标准
GB/T519—2008
代替GB/T519--2003
充气轮胎物理性能试验方法
Test methods for measuring physical properties of pneumatic tyres2008-06-18发布
中华人民共和国国家质量监督检验检疫总局中国国家标准化管理委员会
2009-02-01实施
本标准代替GB/T519—2003《充气轮胎物理性能试验方法》。本标准与GB/T519—2003的主要差异如下:增加了子午线轮胎外胎特有部位胶料类型的相关试验内容(见5.1.1.1);GB/T519—2008
-增加了“建议优先选用以切削方式(采用切片机)直接制备标准厚度试样”(见5.1.1.1);一增加了全钢子午线轮胎胎圈部位胎体钢帘线密度的测定(见5.3.2.2);-增加了纤维子午线轮胎纤维冠带层帘线的相关取样及试验内容(见5.3.3.1.2);-增加了子午线轮胎胎体层、带束层、钢帘线的取样及试验相关内容(见5.3.3.1.3);增加了子午线轮胎内衬气密胶层渗透性的分析观测试验内容(见第6章)。本标准由中国石油和化学工业协会提出。本标准由全国轮胎轮辆标准化技术委员会(SAC/TC19)归口。本标准起草单位:北京橡胶工业研究设计院、山东玲珑橡胶有限公司、广州市华南橡胶轮胎有限公司、风神轮胎股份有限公司、赛轮有限公司。本标准主要起草人:梅风国、孙艳波、张映红、王良俭、王小菊。本标准所代替标准的历次版本发布情况为:GB/T519—1986,GB/T519—1993,GB/T519—2003。1范围
充气轮胎物理性能试验方法
GB/T519—2008
本标准规定了充气轮胎(外胎、内胎和垫带)物理性能试验方法用术语和定义、试样制备、外胎物理性能试验、轮胎内衬层渗透分析测定方法、内胎物理性能试验、垫带物理性能试验。本标准适用于轿车轮胎、载重汽车轮胎、农业轮胎、工程机械轮胎和工业车辆充气轮胎。本标准不适用于航空轮胎、摩托车轮胎和力车轮胎。2规范性引用文件
下列文件中的条款通过本标准的引用而成为本标准的条款。凡是注日期的引用文件,其随后所有的修改单(不包括勘误的内容)或修订版均不适用于本标准,然而,鼓励根据本标准达成协议的各方研究是否可使用这些文件的最新版本,凡是不注日期的引用文件,其最新版本适用于本标准。GB/T528硫化橡胶或热塑性橡胶拉伸应力应变性能的测定(GB/T528—1998,eqVISO37:1994)
GB/T529硫化橡胶或热塑性橡胶撕裂强度的测定(裤形、直角形和新月形试样)(GB/T529一1999,eqvISO34-1:1994)
GB/T531
橡胶袖珍硬度计压入硬度试验方法(GB/T5311999idtISO7619:1986)GB/T532
硫化橡胶与织物粘合强度的测定(GB/T532—1997,idtISO36:1993)GB/T1682硫化橡胶低温脆性的测定单试样法9硫化橡胶耐磨性能的测定(用阿克除磨耗机)(GB/T1689—1998,neqBS903:PartGB/T1689
A9:1988)
GB/T2941
橡胶物理试验方法试样制备和调节通用程序(GB/T2941-2006,ISO23529:2004,GB/T3512硫化橡胶或热塑性橡胶热空气加速老化和耐热试验(GB/T3512一2001,eqvISO188.1998,Rubber vulcanized or thermoplastic-Accelerated ageing and heat resistance tests)GB/T6039橡胶物理试验和化学试验术语(GB/T6039—1997,eqvISO1382:1996RubberVocabulary)
GB/T6326轮胎术语(GB/T6326—2005,ISO4223-1:2002,DefinitionsofsometermsusedinthetyreindustryPartl:PneumaticTyres,NEQ)GB/T11181子午线轮胎用钢帘线
HG/T3836硫化橡胶滑动磨耗的测定3术语和定义
GB/T6326和GB/T6039确立的术语和定义适用于本标准。4试样制备
4.1硫化后的成品在取样前应在室内进行调节。外胎的调节时间不少于24h;内胎、垫带的调节时间不少于12h。
4.2从成品中所取样品表面不平整或厚度大于相应标准规定时,应按GB/T2941进行切削、打磨。样品厚度小于相应标准规定时,可按样品的实际厚度裁成试样进行试验。1
GB/T519—2008
5外胎物理性能试验
5.1胶料的物理性能试验
5.1.1拉伸性能
5.1.1.1各部位的取样方法:
一胎面部分,以胎冠中心线为基准,沿轮胎周向切取样品。冠部胶厚度小于或等于10mm,切取一层中层试样,厚度在10mm以上的切取中、下两层(冠部花纹特殊、切样方法不在此限)。一胎侧部分,沿轮胎周向在胎侧部位中部切取样品。一有足量胎肩垫胶的轮胎,可沿轮胎周向的胎肩部位切取“胎肩垫胶”样品,其样品应保证胶料部位的准确性。
对于子午线轮胎的子口防护胶部位和三角胶芯部位(包括含有上、下两种胶料三角胶芯类型的轮胎)同样可沿轮胎周向分别切取各部位胶料样品,其样品应保证胶料部位的准确性。建议优先选择按GB/T2941中以切前方式(采用切片机)直接制备标准厚度试样。5.1.1.2从各部位所切取的样品厚度应不超过3.5mm,并应按GB/T2941打磨成试样所需厚度;也可直接按GB/T2941切削为试样所需厚度。其样品不能夹带相邻部位的其他胶料和与橡胶粘合的织物。
5.1.1.3将切削好或打磨好的样品裁切成符合GB/T528中的2型试样,并标明试样的部位及层次。5.1.1.4当胎面胶花纹特殊,不能切取标准尺寸试样时,可按实际情况裁取试样的夹持部分。5.1.1.5按GB/T528进行拉伸性能试验,按GB/T3512进行老化后的拉伸性能试验。5.1.2硬度
5.1.2.1在胎面各层切取厚度不小于6mm,长度不小于40mm,宽度不小于15mm的样品,或用同一层的最多3个样品,叠成试样。
5.1.2.2按GB/T531测定轮胎各部位胶料的硬度。胎面胶表面硬度可直接在轮胎冠部定。仲时,应以在样品制成的试样上所测得的结果为准。5.1.3耐磨性能
5.1.3.1阿克隆磨耗试验
5.1.3.1.1以胎冠中心线为基准,沿轮胎周向切取样品,见图1。胎面胶厚度在10mm及其以下的样品,切取2个长度约250mm,宽度约15mm~20mm的试样,并以胎面层表面为试验面。一胎面胶厚度在10mm以上的样品,切取个长度约250mm,宽度约15mm20mm的样品胶条,再从中间平分相同厚度的上、下两层试样,以中间平分面分别作为上、下层试样的磨面。5.1.3.1.2按GB/T1689的规定裁切,磨削及粘接试样。5.1.3.1.3按GB/T1689进行试验。蘑面
5.1.3.2滑动磨耗试验
5.1.3.2.1按5.1,3.1.1相同步骤和部位切取样品。GB/T519-—-2008
5.1.3.2.2按HG/T3836的规定裁切,磨前及粘接试样。试样应标明纵(轮胎周向)、横(轮胎径向)方向及里、外面,胎面胶的中间平分面(即里面)为磨面,磨耗时的回转方向应与胎面的纵向一致。5.1.3.2.3按HG/T3836进行试验。5.2层间粘合强度试验
5.2.1试样
5.2.1.1去掉胎侧部分,对称于胎冠中心切取试样,斜交轮胎试样宽为30mm士0.5mm;子午线轮胎试样宽为32mm士0.5mm,试样长约150mm~250mm,详见图2。单位为旁米
去掉部分
切下试样
30±0.5(或32±0.5
胎侧胶/
切制部分
5.2.1.2将试样上胎面胶花纹部分去掉,保留4mm~6mm,当轮胎胎面基部胶厚度小于4mm时,可采用实际厚度。
5.2.1.3轮胎断面宽度大于185mm的,试样的有效剥离长度应不小于100mm;断面宽度为185mm及其以下的,试样的有效剥离长度至少为60mm,剥离面的中点位于胎冠中心。5.2.2测定步骤
5.2.2.1帘线层间粘合强度
斜交轮胎通常以2层或3层为一组。仅在测2~3层间粘合强度时,以2层为一组,子午线轮胎以2层为一组,测胎体1~2层间粘合强度时,可采用1层为一组。在5.2.1.1所述的试样一端剥离层间分割开20mm~50mm的剥离口,为防止进行剥离试验时跳线、审层,在试样剥离层两侧开一深度均匀的侧口。斜交轮胎试样割口深度为2.5mm,子午线轮胎试样割口深度为3.5mm,以保证试样的有效剥离宽度为25mm士0.5mm,见图2。在切割试样两侧胶条时不应切断帘线,
按GB/T532测定上述试样的粘合强度,剥离顺序为从内层到外层,层间胶应附在剥离层下方。不应有跳线或接头出现,否则该处剥离值不计入结果。5.2.2.2斜交轮胎胎面胶与缓冲层之间、子午线轮胎胎面胶与带束层之间或子午线轮胎胎面胶与冠带层之间粘合强度
试样同5.2.1.1。夹持试样时,胶层应夹在夹持器上。其步骤同5.2.2.1。5.2.2.3胎侧胶与帘布层间粘合强度试样在轮胎对称部位的胎侧位置并垂直于轮胎周向切取。试样同5.2.1.1,然后将试样自胎肩处将胶与胎体帘线层或胶与胎体钢丝帘线层之间分割开20mm~40mm的剥离口。试验步骤同5.2.2.1.
GB/T519—2008
5.2.2.4斜交轮胎胎体帘线层与缓冲帘线层、缓冲帘线层与缓冲帘线层之间的粘合强度试样见5.2.1.1,以2层或3层线为一组,试验步骤同5.2.2.1。5.2.2.5子午线轮胎胎体帘线层与带束层之间、带束层与带束层之间、带束层与冠带层之间和冠带层与冠带层之间的粘合强度
试样见5.2.1.1,以2层为一组。试验时胎体帘线层应夹在夹持器上,其余试验步骤同5.2.2.1。5.3线性能试验
5.3.1帘线角度的测定
5.3.1.1胎冠的帘线角度
斜交轮胎按图3的C、D胎冠中心位置各切取一块长度为80mm士1mm,宽度为50mm士1mm的矩形样品。样品的长度方向应和轮胎周向相一致,将样品每两层一一组分开制成试样,标明试样层次。子午线轮胎同样按图3的C、D胎冠中心位置各切取一块样品,样品的外形尺寸可参照斜交轮胎,但边长不应小于50mm。
在试样中心线上画一条纵轴,在纵轴中点附近抽出一根帘线,形成一条痕迹线,用分度为0.5的量角器在交点上分别测定痕迹线与纵轴形成的夹角α、β,该夹角即为此层的帘线角。测定时量角器的水平轴与试样纵轴重合,详见图4a)。5.3.1.2胎侧的帘线角度
按图3的A、B部位,分别标出胎侧中心位置点,以轮胎横向通过所标出的胎侧中心点的最短距离划一直线(应与轮胎直径线重合),通过这一直线的胎侧中心点做轮胎横向直线的垂线为试样的织转。斜交轮胎按图3的A,B部位以胎侧中心点为中心,各切取一块边长为50mm主0.5mm的正方形样品,将样品每两层一组分开制成2个试样,标明层次。子午线轮胎同样按图3的A,B部位以胎侧中心点为中心,各切取一块边长大于50mm的样品,分别制备试样。
抽线的痕迹线应通过试样的中心点。斜交轮胎试样上的痕迹线为强形线,道过中心点微痕迹缓的切线(子午线轮胎不做),测夹角α、β,方法同5.3.1.1,详见图4b)。5.3.1.3以2个试样4个夹角的平均值作为胎冠或胎侧的帘线角。c
5.3.2帘线的密度
5.3.2.1胎冠、胎侧部位帘线的密度GB/T519—2008
在5.3.1.1或5.3.1.2的试样上选一根帘线,作该帘线的垂线,并在垂线上标出50mm的宽度,数该宽度内的帘线根数,乘2得到100mm内的帘线根数,即为相应的帘线密度。5.3.2.2全钢于午胎胎圈部位胎体钢帘线的密度a)截取一段长度在100mm以上轮胎的胎圈部位,然后剥除该部位的子口加强骨架层,使其露出胎体层钢帘线。
b)用钢卷尺延胎圈内弧标出100mm的宽度,数出该宽度内钢帘线根数,即为胎圈部位胎体钢帘线的密度。
5.3.3线的拉伸性能
5.3.3.1取样
5.3.3.1.1斜交轮胎
取样分奇数、偶数层两类情况:a)奇数线层取样时,从胎冠帘线层的第1层上抽取2根相距至少为40mm的帘线,从而得到两条痕迹线。沿该痕迹线切取试样,标明层次。b)偶数线层取样时,沿相应层的帘线方向切取宽度至少为50mm的试样,标明层次。5.3.3.1.2半钢丝午线轮胎
取样分胎体帘线、冠带层帘线两类情况:a)半钢丝子午线轮胎胎体帘线取样,从轮胎胎里的子口部位用刀切割分离出帘线端头和层次,依次抽取各层帘线,标明层次。
b)半钢丝子午线轮胎冠带层帘线取样,沿轮胎冠部中心周向以一定的宽度,切穿胎面胶直至带束钢帘线层部位,然后以带束层和冠带层介面剥取长度在350mm以上的冠带层纤维帘线,依层次抽取冠带层帘线并标明层次。5.3.3.1.3全钢丝子午线轮胎
取样分胎体钢帘线、带束层钢帘线两类情况:a)全钢丝子午线轮胎胎体为钢丝线,取样应沿胎体钢丝帘线排列方向,从轮胎胎圈部位胎体钢帘线的反包端点分离出胎体钢帘线并剔除附胶,但不要伤损钢帘线。b)全钢丝子午线轮胎带束层(包括零度带束层)钢帘线取样,应截取一段60mm左右轮胎,剔除其胎面胶使其露出带束层钢丝帘线,然后从轮胎的两肩带束层钢帘线端点部位依层次分离并剥取各带束层层次钢帘线。
5.3.3.2试样要求
所抽取的帘线试样长度应在350mm以上,小规格(断面宽度在185mm及其以下的)轮胎,帘线试样至少长180mm。代表每层的帘线数量不应少于10根。5.3.3.3试验步骤
5.3.3.3.1从纤维子午胎和全钢子午胎上抽取的胎体钢帘线和带束层钢帘线均按GB/T11181进行钢帘线破断力和破断伸长率的测定。5.3.3.3.2纤维帘线试样试验前应置于温度为20℃土2℃,湿度为65%土2%条件下调节24h土2h人造丝帘线试样应在105℃士2℃的温度下烘2h~3h,然后置于干燥器内冷却30min。5.3.3.3.3用测力精度为1N,测伸长值精度为1mm的拉力试验机测定帘线的定负荷伸长率。试验机还应配有自动记录装置。
5.3.3.3.4拉伸前帘线应施加规定的预加张力。5.3.3.3.5按不同的试样长度,规定不同的夹持距离;长度≥350mm的帘线,夹持距离为250mm;180mm≤长度<350mm的帘线,夹持距离为100mm。5
GB/T519—2008
5.3.3.3.6以300mm/min士5mm/min的速度拉伸帘线直至拉断。5.3.3.3.7帘线打滑或断裂在夹具钳口处,其数值应删除。有效试样数不应少于10个。5.3.4数据处理
试验结果表示见式(1):
式中:
L1-Lo×100%
-定负荷伸长率或扯断伸长率,单位为百分率(%);开始试验时,夹持器间的距离(250mm或100mm),单位为毫米(mm);Lo
Li一定负荷时的夹持器间的距离或帘线扯断时的夹持器间的距离,单位为毫米(mm)。(1)
试验结果采用5.3.3.3.7的试样组单根帘线测试记录进行计算。若单根帘线测试记录值与平均值超出土10%,则该数据予以删除。删除后的有效数据应不少于5个。6轮胎内村层淄透分析测定方法
6.1轮胎圆周均勾取四个点按以上方法进行试样切取和观测。6.2在图5所示胎肩防擦线下截断轮胎,按圆周方向切开胎肩,切口要清晰(用虎钳把断块夹住,并只以压力,用新裁力把它切断)。图5
6.3用10倍以上的放大镜下进行检测。将所得结果与图6所示进行对比。以内衬层胶渗人帘线间的程度的百分比进行结果判定。
胎体帘线
内村层
内衬层未渗入胎体帘线间
内村层渗入胎体帘线间
胎体存线
内衬层
7内胎的物理性能试验
7.1单层厚度取样方法和单层厚度值GB/T519-2008
将内胎平叠放在平面上,避开内胎接头和气门嘴部位,相距90°依次横向截取4个宽度为25mm的试样,在所截取的4个试样的外周合模线附近位置、内周合模线附近位置和上下模中心附近位置,用厚度计分别测量其厚度。上述16点测量的算术平均值为单层厚度值。7.2拉伸强度、老化后拉伸强度变化率、扯断伸长率7.2.1在上、下模位置分别沿内胎周向切取样品各10个。内胎周向为试样长度方向。7.2.2将切取好的样品按GB/T2941的规定切削或打磨至标准厚度(胎身厚度小于等于2.2mm的,可直接裁成试样),在标准实验室环境下调节16h后,按GB/T528中规定的1型哑铃状裁刀裁取试样。上、下模位置各裁取10个试样,试样应标明方向,试验报告中应注明试样是否经过打磨。7.2.3将上、下模位置的试样分别平均分成两组,每组5个试样。7.2.4从上、下模位置试样中分别随机抽取1组,按GB/T528的规定分别进行拉伸强度、扯断伸长率试验。
7.2.5将上、下模位置的另一组试样,任选表1规定的试验条件,按照GB/T3512的规定分别进行老化后拉伸强度试验,老化后拉伸强度变化率按式(2)计算。表1老化试验条件
老化试验条件
老化温度
老化时间
式中:
90℃±1℃
Ac-XX×100
Ac一一相对于老化前拉伸强度变化率,%;X。老化前的拉伸强度,单位为兆帕(MPa);X1老化后的拉伸强度,单位为兆帕(MPa)。2
70℃±1r
7.2.6每组试样拉伸强度、扯断伸长率和老化后拉伸强度的试验结果取中值。试验报告的拉伸强度、扯断伸长率值取上、下模位置两个中值的最小值。老化后拉伸强度变化率上模和下模两个值分别计算,取其绝对值中的最大值。
7.3接头部位的拉伸强度
7.3.1在胎身冠部、基部和上、下模四个部位的中心接头位置,沿内胎周向各切取一个样品。内胎周向为试样长度方向。
7.3.2样品应按GB/T2941规定打磨至标准厚度(样品厚度小于等于3mm的,可直接裁成试样),将打磨后样品在标准实验室环境下调节16h后,裁切为GB/T528中规定的1型哑铃状试样,接头位置应处于哑铃状试样的工作标线之内。取接头位置邻近两点厚度的平均值作为试样厚度。7.3.3按GB/T528规定的试验方法试验,试验报告值取四个值的最低值。7.4热拉伸变形
7.4.1采用GB/T528中规定的1型哑铃状裁刀,在内胎上、下模位置,按内胎周向各切取一个试样,印标线间距为25mm士0.1mm的标线。7.4.2将试样拉伸至标线间距为37.5mm时固定,然后在温度为105℃土2℃的热空气老化箱中放置5h。取出后在GB/T2941规定的标准实验室环境下调节2h,去掉张力,并停放8h后,测量标线间距,按式(3)计算热拉伸变形,取两个试样试验结果的最大值。7
GB/T519—2008
式中:
S,热拉伸变形,%;
S. =×100
初始试验标线间距,单位为毫米(mm);试验后的试验标线间距,单位为毫米(mm)。7.5撕裂性能
-(3)
7.5.1在内胎上、下模位置分别沿内胎径向切取撕裂性能样品各5个。内胎径向为试样长度方向。7.5.2将切取的样品按照GB/T2941的规定,切前或打磨成标准厚度样品(胎身厚度小于或等于2.2mm的可直接裁成试样),并在标准实验室环境下调节16h后,按照GB/T529裁切成试样并进行试验。7.6硬度
在内胎上切取长度不小于40mm,宽度不小于15mm的样品,将样品叠成厚度为6mm以上的试样。按GB/T531进行试验。
7.7脆性温度
在内胎上切取样品,按GB/T1682进行试验。7.8气门嘴胶垫与金属气门嘴、气门嘴胶垫与胎身胶的粘合强度7.8.1气门嘴胶垫与金属气门嘴粘合强度。7.8.1.1有底盘弯嘴金属气门嘴与气门嘴胶垫粘合强度,在气门嘴试样的底盘中部保留-条宽15mm士0.5mm胶条,切除其余部分,将带嘴的一面沿底盘边缘切开胶与金属界面,注意不应损伤底盘胶,在底盘中心垂直切断胶条,制成两个试样。将金属气门嘴紧固在一端带有孔径12mm的金属板上(见图7),金属板的另一端夹于试验机上夹持器,把剥离胶条呈180°夹于下夹持器按GB/T532进行试验,两个试样所得的数值都应达到标准规定值,试验结果取其中的最小值。单位为千牛每米(kV/m)。7.8.1.2直杆气门嘴与气门嘴包胶粘合力:在气门嘴胶垫中心部位保留宽15mm士0.5mm的胶条,其余部分去掉(见图8),然后沿胶条宽两侧将胶垫底部和直杆包胶切至金属嘴表面,分别切取对移的两等份(见图9)。
把试样横穿在夹具上(见图10),再将夹具放在拉力试验机的上夹持器上,把试样另一端的胶条夹在下夹持器上。剥离试验的牵引速度为50mm/min士5mm/min。两个试样分别进行剥离试验,在剥离试验中要求保持呈90°角剥离状态,剥离到胶与金属嘴脱离为止。
在试验过程中,若气门嘴包胶被扯断,粘合力以胶扯断时负荷计算。粘合力值以两个试样试验数值的最低值表示,单位为牛顿(N)。单位为毫米
法掉部分
上联接夹具
固定试样锁针
夹持部位
夹持部位
保留胶条
去掉部分
切割线
GB/T519-2008
单位为毫米
单位为毫米bzxZ.net
GB/T519—2008
7.8.2气门嘴胶垫与胎身胶的粘合强度从内胎上切取气门嘴胶垫样品,在气门嘴任意两侧对称并且平行部位的胶垫上制备宽度为10mm士0.5mm的试样各个,在试样的胶垫与胎身胶的结合面分别开20mm~30mm的口,将胶垫与胎身分别夹于上、下夹持器,按GB/T532进行试验,粘合强度值以两个试样试验数值的最低值表示,单位为干牛每米(kN/m)。
剥离中如果胶层被扯断,此时粘合强度大于胶层的拉伸强度,表示结果时应加以说明,8垫带物理性能试验
8.1拉伸性能
8.1.1在垫带中间位置沿垫带周向切取样品,按GB/T2941进行切削或打磨并进行试样调节后,裁切成10个符合GB/T528中规定的1型哑铃状试样。8.1.2按GB/T528进行拉伸性能试验。按GB/T3512进行老化后的拉伸性能试验。8.2硬度
在垫带中间切取长度不小于40mm,宽度不小于15mm的样品,将样品叠成厚度不小于6mm的试样,按GB/T531进行试验。
小提示:此标准内容仅展示完整标准里的部分截取内容,若需要完整标准请到上方自行免费下载完整标准文档。
中华人民共和国国家标准
GB/T519—2008
代替GB/T519--2003
充气轮胎物理性能试验方法
Test methods for measuring physical properties of pneumatic tyres2008-06-18发布
中华人民共和国国家质量监督检验检疫总局中国国家标准化管理委员会
2009-02-01实施
本标准代替GB/T519—2003《充气轮胎物理性能试验方法》。本标准与GB/T519—2003的主要差异如下:增加了子午线轮胎外胎特有部位胶料类型的相关试验内容(见5.1.1.1);GB/T519—2008
-增加了“建议优先选用以切削方式(采用切片机)直接制备标准厚度试样”(见5.1.1.1);一增加了全钢子午线轮胎胎圈部位胎体钢帘线密度的测定(见5.3.2.2);-增加了纤维子午线轮胎纤维冠带层帘线的相关取样及试验内容(见5.3.3.1.2);-增加了子午线轮胎胎体层、带束层、钢帘线的取样及试验相关内容(见5.3.3.1.3);增加了子午线轮胎内衬气密胶层渗透性的分析观测试验内容(见第6章)。本标准由中国石油和化学工业协会提出。本标准由全国轮胎轮辆标准化技术委员会(SAC/TC19)归口。本标准起草单位:北京橡胶工业研究设计院、山东玲珑橡胶有限公司、广州市华南橡胶轮胎有限公司、风神轮胎股份有限公司、赛轮有限公司。本标准主要起草人:梅风国、孙艳波、张映红、王良俭、王小菊。本标准所代替标准的历次版本发布情况为:GB/T519—1986,GB/T519—1993,GB/T519—2003。1范围
充气轮胎物理性能试验方法
GB/T519—2008
本标准规定了充气轮胎(外胎、内胎和垫带)物理性能试验方法用术语和定义、试样制备、外胎物理性能试验、轮胎内衬层渗透分析测定方法、内胎物理性能试验、垫带物理性能试验。本标准适用于轿车轮胎、载重汽车轮胎、农业轮胎、工程机械轮胎和工业车辆充气轮胎。本标准不适用于航空轮胎、摩托车轮胎和力车轮胎。2规范性引用文件
下列文件中的条款通过本标准的引用而成为本标准的条款。凡是注日期的引用文件,其随后所有的修改单(不包括勘误的内容)或修订版均不适用于本标准,然而,鼓励根据本标准达成协议的各方研究是否可使用这些文件的最新版本,凡是不注日期的引用文件,其最新版本适用于本标准。GB/T528硫化橡胶或热塑性橡胶拉伸应力应变性能的测定(GB/T528—1998,eqVISO37:1994)
GB/T529硫化橡胶或热塑性橡胶撕裂强度的测定(裤形、直角形和新月形试样)(GB/T529一1999,eqvISO34-1:1994)
GB/T531
橡胶袖珍硬度计压入硬度试验方法(GB/T5311999idtISO7619:1986)GB/T532
硫化橡胶与织物粘合强度的测定(GB/T532—1997,idtISO36:1993)GB/T1682硫化橡胶低温脆性的测定单试样法9硫化橡胶耐磨性能的测定(用阿克除磨耗机)(GB/T1689—1998,neqBS903:PartGB/T1689
A9:1988)
GB/T2941
橡胶物理试验方法试样制备和调节通用程序(GB/T2941-2006,ISO23529:2004,GB/T3512硫化橡胶或热塑性橡胶热空气加速老化和耐热试验(GB/T3512一2001,eqvISO188.1998,Rubber vulcanized or thermoplastic-Accelerated ageing and heat resistance tests)GB/T6039橡胶物理试验和化学试验术语(GB/T6039—1997,eqvISO1382:1996RubberVocabulary)
GB/T6326轮胎术语(GB/T6326—2005,ISO4223-1:2002,DefinitionsofsometermsusedinthetyreindustryPartl:PneumaticTyres,NEQ)GB/T11181子午线轮胎用钢帘线
HG/T3836硫化橡胶滑动磨耗的测定3术语和定义
GB/T6326和GB/T6039确立的术语和定义适用于本标准。4试样制备
4.1硫化后的成品在取样前应在室内进行调节。外胎的调节时间不少于24h;内胎、垫带的调节时间不少于12h。
4.2从成品中所取样品表面不平整或厚度大于相应标准规定时,应按GB/T2941进行切削、打磨。样品厚度小于相应标准规定时,可按样品的实际厚度裁成试样进行试验。1
GB/T519—2008
5外胎物理性能试验
5.1胶料的物理性能试验
5.1.1拉伸性能
5.1.1.1各部位的取样方法:
一胎面部分,以胎冠中心线为基准,沿轮胎周向切取样品。冠部胶厚度小于或等于10mm,切取一层中层试样,厚度在10mm以上的切取中、下两层(冠部花纹特殊、切样方法不在此限)。一胎侧部分,沿轮胎周向在胎侧部位中部切取样品。一有足量胎肩垫胶的轮胎,可沿轮胎周向的胎肩部位切取“胎肩垫胶”样品,其样品应保证胶料部位的准确性。
对于子午线轮胎的子口防护胶部位和三角胶芯部位(包括含有上、下两种胶料三角胶芯类型的轮胎)同样可沿轮胎周向分别切取各部位胶料样品,其样品应保证胶料部位的准确性。建议优先选择按GB/T2941中以切前方式(采用切片机)直接制备标准厚度试样。5.1.1.2从各部位所切取的样品厚度应不超过3.5mm,并应按GB/T2941打磨成试样所需厚度;也可直接按GB/T2941切削为试样所需厚度。其样品不能夹带相邻部位的其他胶料和与橡胶粘合的织物。
5.1.1.3将切削好或打磨好的样品裁切成符合GB/T528中的2型试样,并标明试样的部位及层次。5.1.1.4当胎面胶花纹特殊,不能切取标准尺寸试样时,可按实际情况裁取试样的夹持部分。5.1.1.5按GB/T528进行拉伸性能试验,按GB/T3512进行老化后的拉伸性能试验。5.1.2硬度
5.1.2.1在胎面各层切取厚度不小于6mm,长度不小于40mm,宽度不小于15mm的样品,或用同一层的最多3个样品,叠成试样。
5.1.2.2按GB/T531测定轮胎各部位胶料的硬度。胎面胶表面硬度可直接在轮胎冠部定。仲时,应以在样品制成的试样上所测得的结果为准。5.1.3耐磨性能
5.1.3.1阿克隆磨耗试验
5.1.3.1.1以胎冠中心线为基准,沿轮胎周向切取样品,见图1。胎面胶厚度在10mm及其以下的样品,切取2个长度约250mm,宽度约15mm~20mm的试样,并以胎面层表面为试验面。一胎面胶厚度在10mm以上的样品,切取个长度约250mm,宽度约15mm20mm的样品胶条,再从中间平分相同厚度的上、下两层试样,以中间平分面分别作为上、下层试样的磨面。5.1.3.1.2按GB/T1689的规定裁切,磨削及粘接试样。5.1.3.1.3按GB/T1689进行试验。蘑面
5.1.3.2滑动磨耗试验
5.1.3.2.1按5.1,3.1.1相同步骤和部位切取样品。GB/T519-—-2008
5.1.3.2.2按HG/T3836的规定裁切,磨前及粘接试样。试样应标明纵(轮胎周向)、横(轮胎径向)方向及里、外面,胎面胶的中间平分面(即里面)为磨面,磨耗时的回转方向应与胎面的纵向一致。5.1.3.2.3按HG/T3836进行试验。5.2层间粘合强度试验
5.2.1试样
5.2.1.1去掉胎侧部分,对称于胎冠中心切取试样,斜交轮胎试样宽为30mm士0.5mm;子午线轮胎试样宽为32mm士0.5mm,试样长约150mm~250mm,详见图2。单位为旁米
去掉部分
切下试样
30±0.5(或32±0.5
胎侧胶/
切制部分
5.2.1.2将试样上胎面胶花纹部分去掉,保留4mm~6mm,当轮胎胎面基部胶厚度小于4mm时,可采用实际厚度。
5.2.1.3轮胎断面宽度大于185mm的,试样的有效剥离长度应不小于100mm;断面宽度为185mm及其以下的,试样的有效剥离长度至少为60mm,剥离面的中点位于胎冠中心。5.2.2测定步骤
5.2.2.1帘线层间粘合强度
斜交轮胎通常以2层或3层为一组。仅在测2~3层间粘合强度时,以2层为一组,子午线轮胎以2层为一组,测胎体1~2层间粘合强度时,可采用1层为一组。在5.2.1.1所述的试样一端剥离层间分割开20mm~50mm的剥离口,为防止进行剥离试验时跳线、审层,在试样剥离层两侧开一深度均匀的侧口。斜交轮胎试样割口深度为2.5mm,子午线轮胎试样割口深度为3.5mm,以保证试样的有效剥离宽度为25mm士0.5mm,见图2。在切割试样两侧胶条时不应切断帘线,
按GB/T532测定上述试样的粘合强度,剥离顺序为从内层到外层,层间胶应附在剥离层下方。不应有跳线或接头出现,否则该处剥离值不计入结果。5.2.2.2斜交轮胎胎面胶与缓冲层之间、子午线轮胎胎面胶与带束层之间或子午线轮胎胎面胶与冠带层之间粘合强度
试样同5.2.1.1。夹持试样时,胶层应夹在夹持器上。其步骤同5.2.2.1。5.2.2.3胎侧胶与帘布层间粘合强度试样在轮胎对称部位的胎侧位置并垂直于轮胎周向切取。试样同5.2.1.1,然后将试样自胎肩处将胶与胎体帘线层或胶与胎体钢丝帘线层之间分割开20mm~40mm的剥离口。试验步骤同5.2.2.1.
GB/T519—2008
5.2.2.4斜交轮胎胎体帘线层与缓冲帘线层、缓冲帘线层与缓冲帘线层之间的粘合强度试样见5.2.1.1,以2层或3层线为一组,试验步骤同5.2.2.1。5.2.2.5子午线轮胎胎体帘线层与带束层之间、带束层与带束层之间、带束层与冠带层之间和冠带层与冠带层之间的粘合强度
试样见5.2.1.1,以2层为一组。试验时胎体帘线层应夹在夹持器上,其余试验步骤同5.2.2.1。5.3线性能试验
5.3.1帘线角度的测定
5.3.1.1胎冠的帘线角度
斜交轮胎按图3的C、D胎冠中心位置各切取一块长度为80mm士1mm,宽度为50mm士1mm的矩形样品。样品的长度方向应和轮胎周向相一致,将样品每两层一一组分开制成试样,标明试样层次。子午线轮胎同样按图3的C、D胎冠中心位置各切取一块样品,样品的外形尺寸可参照斜交轮胎,但边长不应小于50mm。
在试样中心线上画一条纵轴,在纵轴中点附近抽出一根帘线,形成一条痕迹线,用分度为0.5的量角器在交点上分别测定痕迹线与纵轴形成的夹角α、β,该夹角即为此层的帘线角。测定时量角器的水平轴与试样纵轴重合,详见图4a)。5.3.1.2胎侧的帘线角度
按图3的A、B部位,分别标出胎侧中心位置点,以轮胎横向通过所标出的胎侧中心点的最短距离划一直线(应与轮胎直径线重合),通过这一直线的胎侧中心点做轮胎横向直线的垂线为试样的织转。斜交轮胎按图3的A,B部位以胎侧中心点为中心,各切取一块边长为50mm主0.5mm的正方形样品,将样品每两层一组分开制成2个试样,标明层次。子午线轮胎同样按图3的A,B部位以胎侧中心点为中心,各切取一块边长大于50mm的样品,分别制备试样。
抽线的痕迹线应通过试样的中心点。斜交轮胎试样上的痕迹线为强形线,道过中心点微痕迹缓的切线(子午线轮胎不做),测夹角α、β,方法同5.3.1.1,详见图4b)。5.3.1.3以2个试样4个夹角的平均值作为胎冠或胎侧的帘线角。c
5.3.2帘线的密度
5.3.2.1胎冠、胎侧部位帘线的密度GB/T519—2008
在5.3.1.1或5.3.1.2的试样上选一根帘线,作该帘线的垂线,并在垂线上标出50mm的宽度,数该宽度内的帘线根数,乘2得到100mm内的帘线根数,即为相应的帘线密度。5.3.2.2全钢于午胎胎圈部位胎体钢帘线的密度a)截取一段长度在100mm以上轮胎的胎圈部位,然后剥除该部位的子口加强骨架层,使其露出胎体层钢帘线。
b)用钢卷尺延胎圈内弧标出100mm的宽度,数出该宽度内钢帘线根数,即为胎圈部位胎体钢帘线的密度。
5.3.3线的拉伸性能
5.3.3.1取样
5.3.3.1.1斜交轮胎
取样分奇数、偶数层两类情况:a)奇数线层取样时,从胎冠帘线层的第1层上抽取2根相距至少为40mm的帘线,从而得到两条痕迹线。沿该痕迹线切取试样,标明层次。b)偶数线层取样时,沿相应层的帘线方向切取宽度至少为50mm的试样,标明层次。5.3.3.1.2半钢丝午线轮胎
取样分胎体帘线、冠带层帘线两类情况:a)半钢丝子午线轮胎胎体帘线取样,从轮胎胎里的子口部位用刀切割分离出帘线端头和层次,依次抽取各层帘线,标明层次。
b)半钢丝子午线轮胎冠带层帘线取样,沿轮胎冠部中心周向以一定的宽度,切穿胎面胶直至带束钢帘线层部位,然后以带束层和冠带层介面剥取长度在350mm以上的冠带层纤维帘线,依层次抽取冠带层帘线并标明层次。5.3.3.1.3全钢丝子午线轮胎
取样分胎体钢帘线、带束层钢帘线两类情况:a)全钢丝子午线轮胎胎体为钢丝线,取样应沿胎体钢丝帘线排列方向,从轮胎胎圈部位胎体钢帘线的反包端点分离出胎体钢帘线并剔除附胶,但不要伤损钢帘线。b)全钢丝子午线轮胎带束层(包括零度带束层)钢帘线取样,应截取一段60mm左右轮胎,剔除其胎面胶使其露出带束层钢丝帘线,然后从轮胎的两肩带束层钢帘线端点部位依层次分离并剥取各带束层层次钢帘线。
5.3.3.2试样要求
所抽取的帘线试样长度应在350mm以上,小规格(断面宽度在185mm及其以下的)轮胎,帘线试样至少长180mm。代表每层的帘线数量不应少于10根。5.3.3.3试验步骤
5.3.3.3.1从纤维子午胎和全钢子午胎上抽取的胎体钢帘线和带束层钢帘线均按GB/T11181进行钢帘线破断力和破断伸长率的测定。5.3.3.3.2纤维帘线试样试验前应置于温度为20℃土2℃,湿度为65%土2%条件下调节24h土2h人造丝帘线试样应在105℃士2℃的温度下烘2h~3h,然后置于干燥器内冷却30min。5.3.3.3.3用测力精度为1N,测伸长值精度为1mm的拉力试验机测定帘线的定负荷伸长率。试验机还应配有自动记录装置。
5.3.3.3.4拉伸前帘线应施加规定的预加张力。5.3.3.3.5按不同的试样长度,规定不同的夹持距离;长度≥350mm的帘线,夹持距离为250mm;180mm≤长度<350mm的帘线,夹持距离为100mm。5
GB/T519—2008
5.3.3.3.6以300mm/min士5mm/min的速度拉伸帘线直至拉断。5.3.3.3.7帘线打滑或断裂在夹具钳口处,其数值应删除。有效试样数不应少于10个。5.3.4数据处理
试验结果表示见式(1):
式中:
L1-Lo×100%
-定负荷伸长率或扯断伸长率,单位为百分率(%);开始试验时,夹持器间的距离(250mm或100mm),单位为毫米(mm);Lo
Li一定负荷时的夹持器间的距离或帘线扯断时的夹持器间的距离,单位为毫米(mm)。(1)
试验结果采用5.3.3.3.7的试样组单根帘线测试记录进行计算。若单根帘线测试记录值与平均值超出土10%,则该数据予以删除。删除后的有效数据应不少于5个。6轮胎内村层淄透分析测定方法
6.1轮胎圆周均勾取四个点按以上方法进行试样切取和观测。6.2在图5所示胎肩防擦线下截断轮胎,按圆周方向切开胎肩,切口要清晰(用虎钳把断块夹住,并只以压力,用新裁力把它切断)。图5
6.3用10倍以上的放大镜下进行检测。将所得结果与图6所示进行对比。以内衬层胶渗人帘线间的程度的百分比进行结果判定。
胎体帘线
内村层
内衬层未渗入胎体帘线间
内村层渗入胎体帘线间
胎体存线
内衬层
7内胎的物理性能试验
7.1单层厚度取样方法和单层厚度值GB/T519-2008
将内胎平叠放在平面上,避开内胎接头和气门嘴部位,相距90°依次横向截取4个宽度为25mm的试样,在所截取的4个试样的外周合模线附近位置、内周合模线附近位置和上下模中心附近位置,用厚度计分别测量其厚度。上述16点测量的算术平均值为单层厚度值。7.2拉伸强度、老化后拉伸强度变化率、扯断伸长率7.2.1在上、下模位置分别沿内胎周向切取样品各10个。内胎周向为试样长度方向。7.2.2将切取好的样品按GB/T2941的规定切削或打磨至标准厚度(胎身厚度小于等于2.2mm的,可直接裁成试样),在标准实验室环境下调节16h后,按GB/T528中规定的1型哑铃状裁刀裁取试样。上、下模位置各裁取10个试样,试样应标明方向,试验报告中应注明试样是否经过打磨。7.2.3将上、下模位置的试样分别平均分成两组,每组5个试样。7.2.4从上、下模位置试样中分别随机抽取1组,按GB/T528的规定分别进行拉伸强度、扯断伸长率试验。
7.2.5将上、下模位置的另一组试样,任选表1规定的试验条件,按照GB/T3512的规定分别进行老化后拉伸强度试验,老化后拉伸强度变化率按式(2)计算。表1老化试验条件
老化试验条件
老化温度
老化时间
式中:
90℃±1℃
Ac-XX×100
Ac一一相对于老化前拉伸强度变化率,%;X。老化前的拉伸强度,单位为兆帕(MPa);X1老化后的拉伸强度,单位为兆帕(MPa)。2
70℃±1r
7.2.6每组试样拉伸强度、扯断伸长率和老化后拉伸强度的试验结果取中值。试验报告的拉伸强度、扯断伸长率值取上、下模位置两个中值的最小值。老化后拉伸强度变化率上模和下模两个值分别计算,取其绝对值中的最大值。
7.3接头部位的拉伸强度
7.3.1在胎身冠部、基部和上、下模四个部位的中心接头位置,沿内胎周向各切取一个样品。内胎周向为试样长度方向。
7.3.2样品应按GB/T2941规定打磨至标准厚度(样品厚度小于等于3mm的,可直接裁成试样),将打磨后样品在标准实验室环境下调节16h后,裁切为GB/T528中规定的1型哑铃状试样,接头位置应处于哑铃状试样的工作标线之内。取接头位置邻近两点厚度的平均值作为试样厚度。7.3.3按GB/T528规定的试验方法试验,试验报告值取四个值的最低值。7.4热拉伸变形
7.4.1采用GB/T528中规定的1型哑铃状裁刀,在内胎上、下模位置,按内胎周向各切取一个试样,印标线间距为25mm士0.1mm的标线。7.4.2将试样拉伸至标线间距为37.5mm时固定,然后在温度为105℃土2℃的热空气老化箱中放置5h。取出后在GB/T2941规定的标准实验室环境下调节2h,去掉张力,并停放8h后,测量标线间距,按式(3)计算热拉伸变形,取两个试样试验结果的最大值。7
GB/T519—2008
式中:
S,热拉伸变形,%;
S. =×100
初始试验标线间距,单位为毫米(mm);试验后的试验标线间距,单位为毫米(mm)。7.5撕裂性能
-(3)
7.5.1在内胎上、下模位置分别沿内胎径向切取撕裂性能样品各5个。内胎径向为试样长度方向。7.5.2将切取的样品按照GB/T2941的规定,切前或打磨成标准厚度样品(胎身厚度小于或等于2.2mm的可直接裁成试样),并在标准实验室环境下调节16h后,按照GB/T529裁切成试样并进行试验。7.6硬度
在内胎上切取长度不小于40mm,宽度不小于15mm的样品,将样品叠成厚度为6mm以上的试样。按GB/T531进行试验。
7.7脆性温度
在内胎上切取样品,按GB/T1682进行试验。7.8气门嘴胶垫与金属气门嘴、气门嘴胶垫与胎身胶的粘合强度7.8.1气门嘴胶垫与金属气门嘴粘合强度。7.8.1.1有底盘弯嘴金属气门嘴与气门嘴胶垫粘合强度,在气门嘴试样的底盘中部保留-条宽15mm士0.5mm胶条,切除其余部分,将带嘴的一面沿底盘边缘切开胶与金属界面,注意不应损伤底盘胶,在底盘中心垂直切断胶条,制成两个试样。将金属气门嘴紧固在一端带有孔径12mm的金属板上(见图7),金属板的另一端夹于试验机上夹持器,把剥离胶条呈180°夹于下夹持器按GB/T532进行试验,两个试样所得的数值都应达到标准规定值,试验结果取其中的最小值。单位为千牛每米(kV/m)。7.8.1.2直杆气门嘴与气门嘴包胶粘合力:在气门嘴胶垫中心部位保留宽15mm士0.5mm的胶条,其余部分去掉(见图8),然后沿胶条宽两侧将胶垫底部和直杆包胶切至金属嘴表面,分别切取对移的两等份(见图9)。
把试样横穿在夹具上(见图10),再将夹具放在拉力试验机的上夹持器上,把试样另一端的胶条夹在下夹持器上。剥离试验的牵引速度为50mm/min士5mm/min。两个试样分别进行剥离试验,在剥离试验中要求保持呈90°角剥离状态,剥离到胶与金属嘴脱离为止。
在试验过程中,若气门嘴包胶被扯断,粘合力以胶扯断时负荷计算。粘合力值以两个试样试验数值的最低值表示,单位为牛顿(N)。单位为毫米
法掉部分
上联接夹具
固定试样锁针
夹持部位
夹持部位
保留胶条
去掉部分
切割线
GB/T519-2008
单位为毫米
单位为毫米bzxZ.net
GB/T519—2008
7.8.2气门嘴胶垫与胎身胶的粘合强度从内胎上切取气门嘴胶垫样品,在气门嘴任意两侧对称并且平行部位的胶垫上制备宽度为10mm士0.5mm的试样各个,在试样的胶垫与胎身胶的结合面分别开20mm~30mm的口,将胶垫与胎身分别夹于上、下夹持器,按GB/T532进行试验,粘合强度值以两个试样试验数值的最低值表示,单位为干牛每米(kN/m)。
剥离中如果胶层被扯断,此时粘合强度大于胶层的拉伸强度,表示结果时应加以说明,8垫带物理性能试验
8.1拉伸性能
8.1.1在垫带中间位置沿垫带周向切取样品,按GB/T2941进行切削或打磨并进行试样调节后,裁切成10个符合GB/T528中规定的1型哑铃状试样。8.1.2按GB/T528进行拉伸性能试验。按GB/T3512进行老化后的拉伸性能试验。8.2硬度
在垫带中间切取长度不小于40mm,宽度不小于15mm的样品,将样品叠成厚度不小于6mm的试样,按GB/T531进行试验。
小提示:此标准内容仅展示完整标准里的部分截取内容,若需要完整标准请到上方自行免费下载完整标准文档。

标准图片预览:
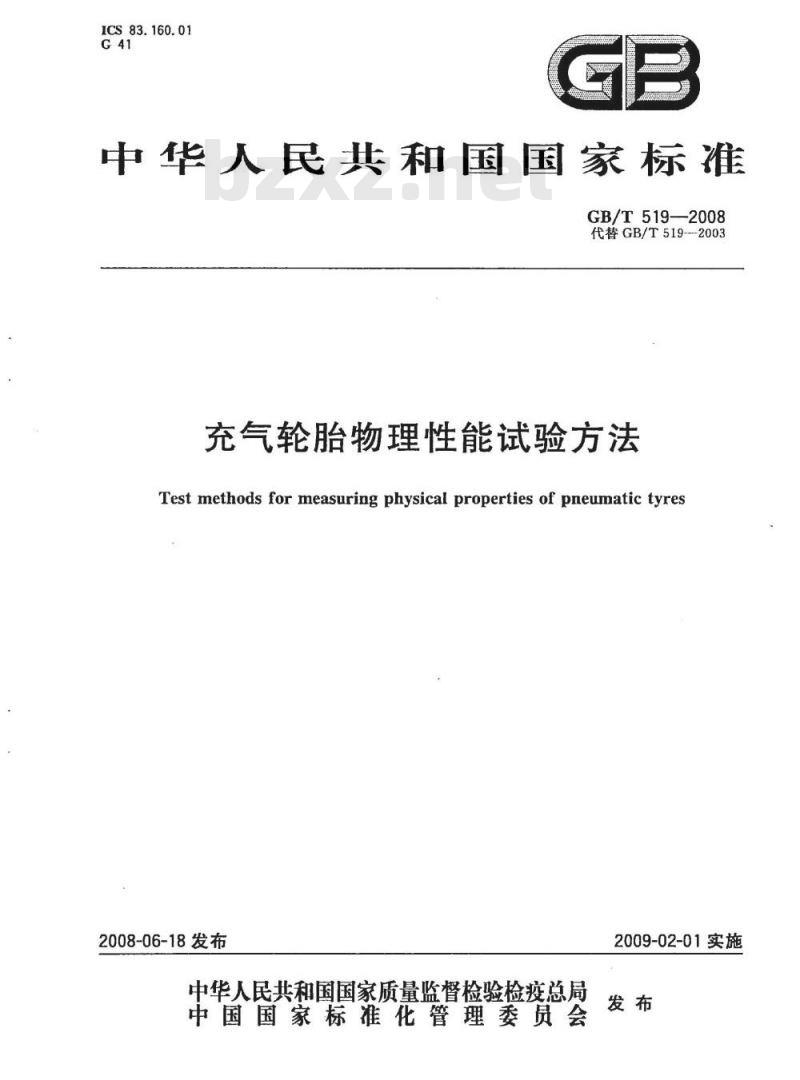
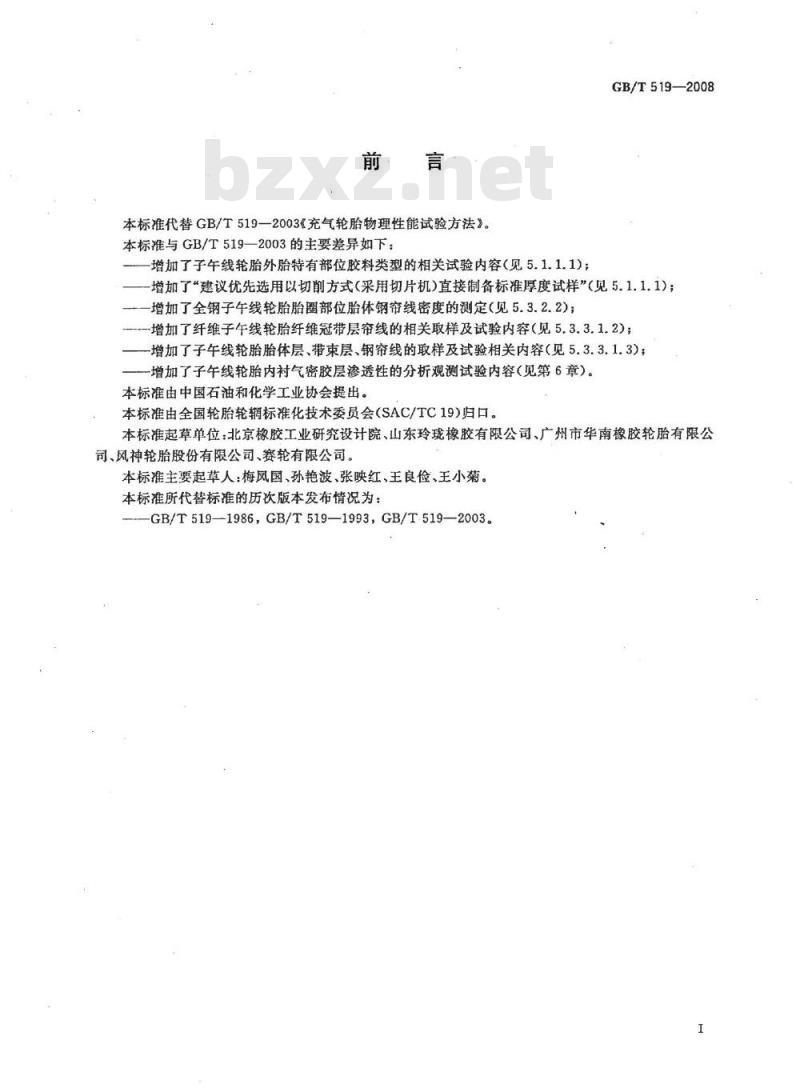
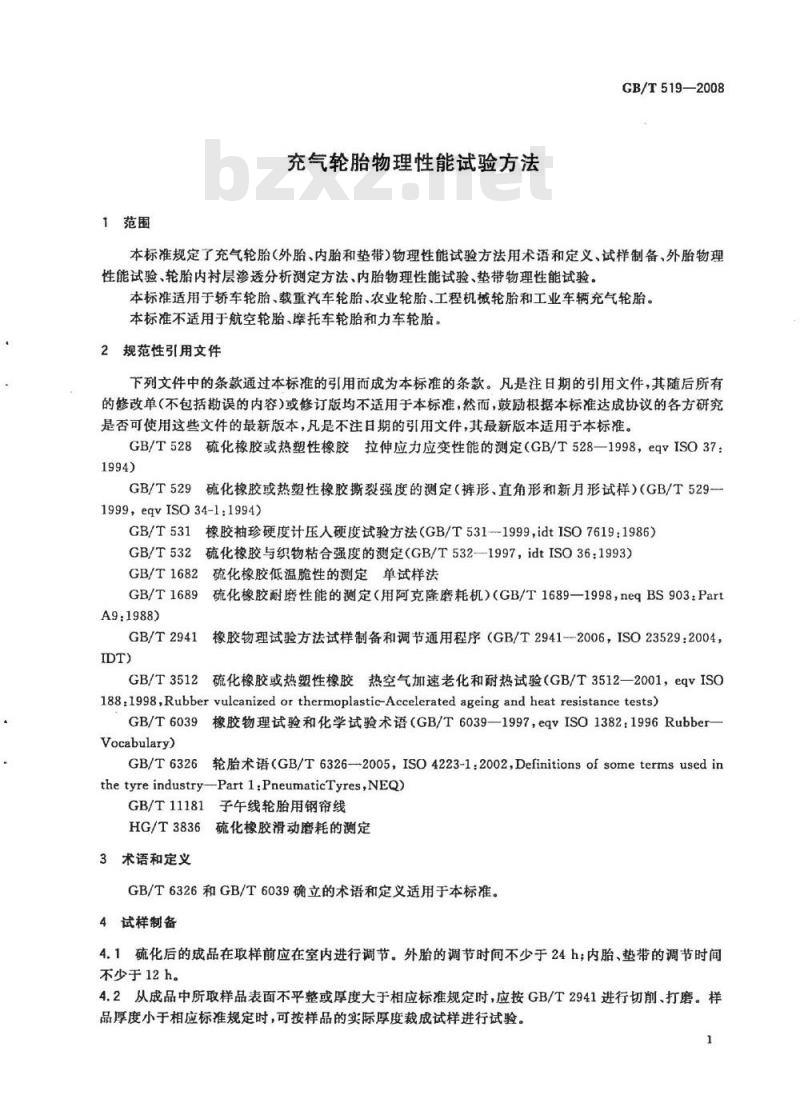
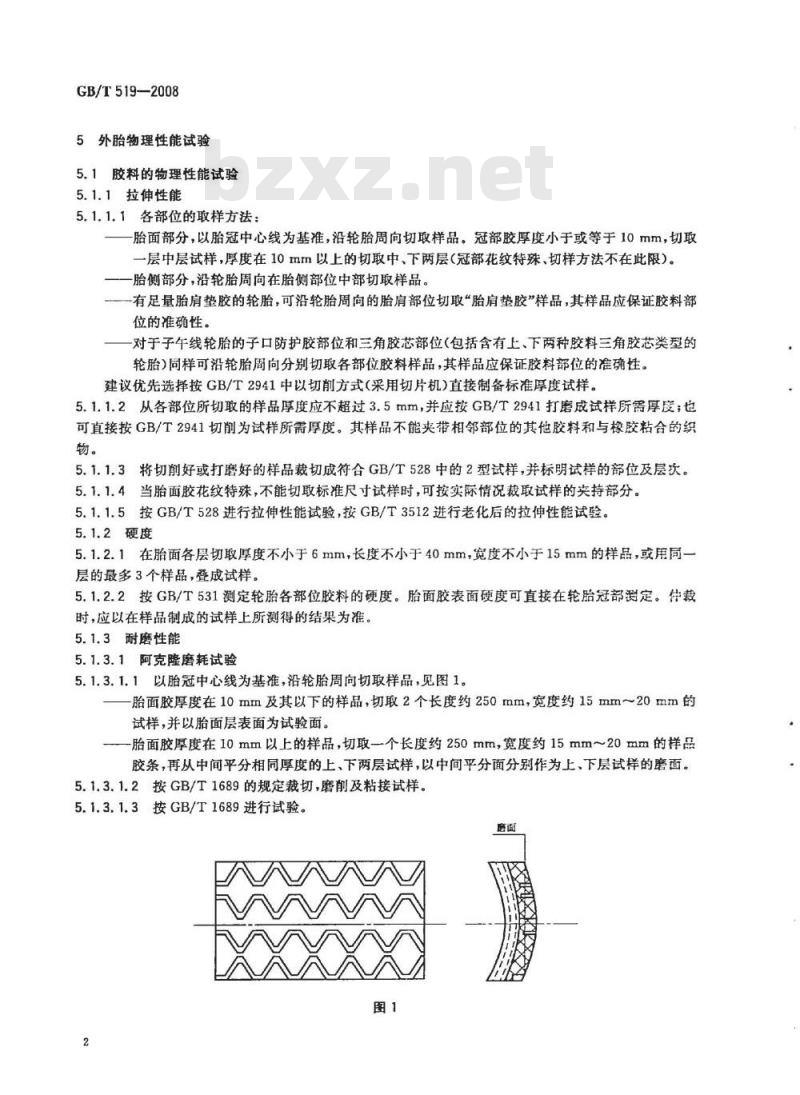
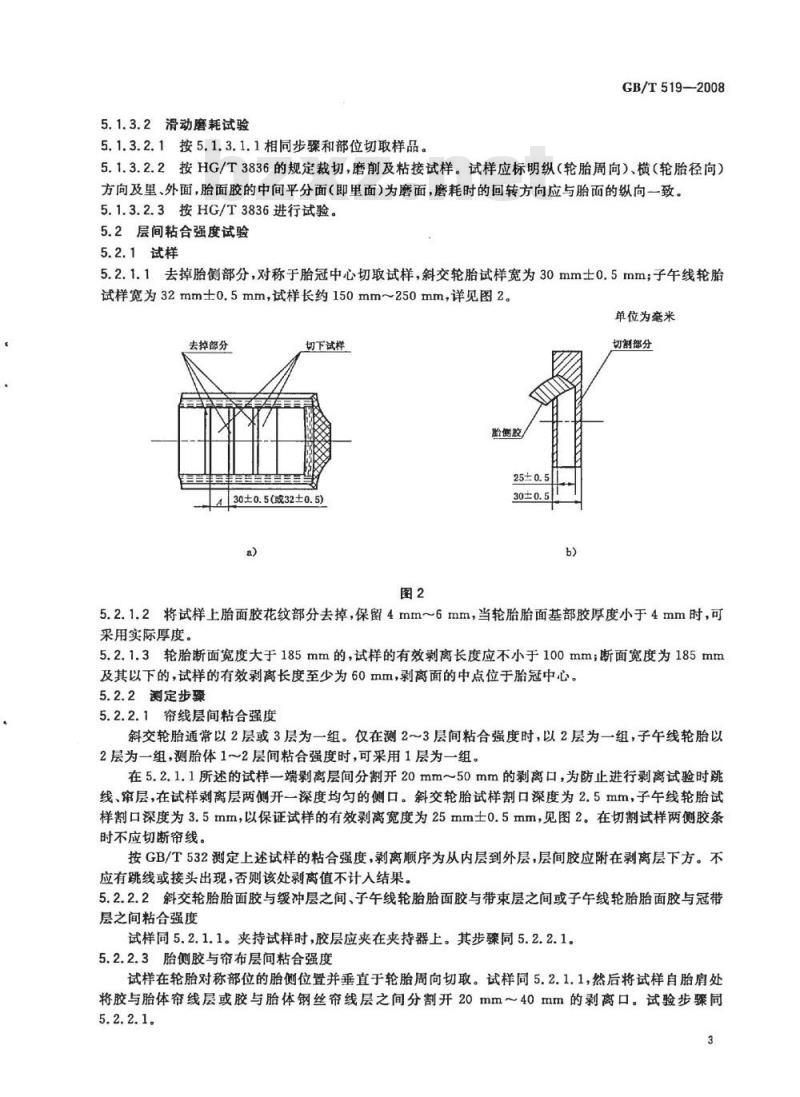
- 其它标准
- 热门标准
- 国家标准(GB)标准计划
- GB/T2828.1-2012 计数抽样检验程序 第1部分:按接收质量限(AQL)检索的逐批检验抽样计划
- GB/T7251.1-2023 低压成套开关设备和控制设备 第1部分:总则
- GB/T50010-2010 混凝土结构设计标准(2024年版)
- GB/T14625.4-2008 篮球、足球、排球、手球试验方法 第4部分:试验条件与试样准备
- GB/T32355.4-2015 电工电子产品可再生利用率评价值 第4部分:复印机和打印机
- GB/T39010-2020 精油 表征
- GB2682-1981 电工成套装置中的指示灯和按钮的颜色
- GB12802.2-2004 电气绝缘用薄膜 第2部分:电气绝缘用聚酯薄膜
- GB13077-2004 铝合金无缝气瓶定期检验与评定
- GB18436-2001 轮机日志和车钟记录簿
- GB/T4789.27-2003 食品卫生微生物学检验 鲜乳中抗生素残留量检验
- GB9123.3-1988 PN1.0MPa(10bar)平面钢制管法兰盖
- GB/T229-2007 金属材料夏比摆锤冲击试验方法
- GB50311-2007 综合布线系统工程设计规范
- GB/T22764.1-2008 低压机柜 第1部分:总规范
请牢记:“bzxz.net”即是“标准下载”四个汉字汉语拼音首字母与国际顶级域名“.net”的组合。 ©2009 标准下载网 www.bzxz.net 本站邮件:[email protected]
网站备案号:湘ICP备2023016450号-1
网站备案号:湘ICP备2023016450号-1